Wie werden hochpräzise Teile bearbeitet?
2023-09-22
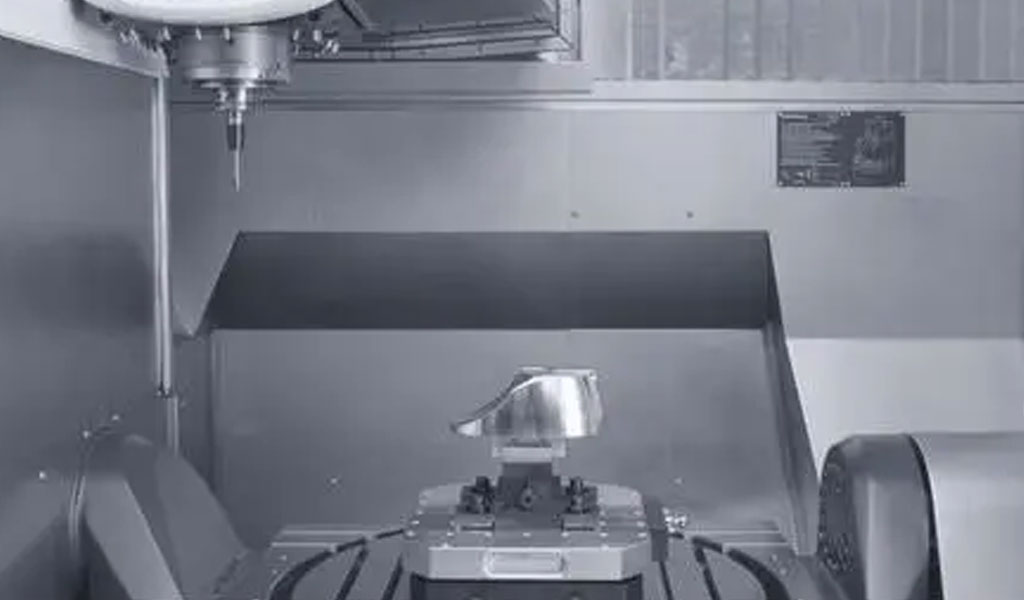
Präzisionsbearbeitung verstehen
Die Präzisionsbearbeitung ist ein Eckpfeiler der modernen Fertigung und verantwortlich für die Herstellung komplizierter und präziser Komponenten, die in einer Vielzahl von Branchen eingesetzt werden. Um ihre Bedeutung vollständig zu verstehen, untersuchen wir die Kernkonzepte der Präzisionsbearbeitung, ihre entscheidende Rolle in verschiedenen Sektoren und den historischen Weg, der zu ihrem aktuellen Stand der Exzellenz geführt hat.A. Was ist Präzisionsbearbeitung?
Unter Präzisionsbearbeitung versteht man eine Reihe von Herstellungsprozessen, bei denen mit einem hohen Maß an Genauigkeit und Kontrolle Material von einem Werkstück entfernt wird, was zu fein gefertigten Bauteilen mit engen Toleranzen führt. Dieser Prozess verwandelt Rohstoffe wie Metalle, Kunststoffe oder Keramik in präzise Teile, die anspruchsvollen Spezifikationen entsprechen. Zu den Hauptmerkmalen der Präzisionsbearbeitung gehören:- Genauigkeit: Durch die Präzisionsbearbeitung wird sichergestellt, dass das Endprodukt mit minimalen Abweichungen genau dem beabsichtigten Design entspricht.
- Enge Toleranzen: Es ermöglicht die Herstellung von Teilen mit extrem engen Toleranzen, was bedeutet, dass die fertigen Komponenten genau den vorgegebenen Maßen entsprechen.
- Hervorragende Oberflächenbeschaffenheit: Die Präzisionsbearbeitung sorgt für außergewöhnliche Oberflächengüten und macht häufig zusätzliche Nachbearbeitungsprozesse überflüssig.
- Komplexe Geometrien: Es kann komplizierte Formen, Konturen und Merkmale erzeugen, was es für die Herstellung von Komponenten mit komplexem Design unverzichtbar macht.
- Wiederholbarkeit: Präzision BearbeitungsprozessSie sind hochgradig wiederholbar und gewährleisten eine gleichbleibende Qualität über mehrere Teile hinweg.
- Vielseitigkeit: Es kann auf eine Vielzahl von Materialien angewendet werden und eignet sich daher für verschiedene Branchen.
B. Bedeutung der Präzisionsbearbeitung
Präzisionsbearbeitung ist in mehreren kritischen Branchen von enormer Bedeutung und wirkt sich auf verschiedene Aspekte unseres täglichen Lebens aus. Hier sind einige überzeugende Gründe für seine Bedeutung:- Luft-und Raumfahrtindustrie: Im Luft- und Raumfahrtsektor ist Präzisionsbearbeitung unverzichtbar, um Komponenten herzustellen, die extremen Bedingungen standhalten. Flugzeugtriebwerke, Landung Gangund Strukturelemente sind für Sicherheit und Leistung auf präzisionsgefertigte Teile angewiesen.
- Medizintechnik: Medizinische Geräte wie chirurgische Instrumente, Prothesen und implantierbare Geräte erfordern eine Präzisionsbearbeitung für Biokompatibilität, Genauigkeit und Patientensicherheit.
- Automobilsektor: Präzisionsgefertigte Teile sind für die Automobilindustrie unerlässlich, um die Zuverlässigkeit und Effizienz von Fahrzeugen sicherzustellen. Komponenten wie Motorteile, Getriebesysteme und Bremsmechanismen sind auf eine präzise Bearbeitung angewiesen.
- Elektronik und Halbleiter: Präzisionsbearbeitung ist von entscheidender Bedeutung bei der Herstellung mikroelektronischer Komponenten und Halbleiterbauelemente, bei denen kleinste Toleranzen für die Funktionalität unerlässlich sind.
- Energie Sektor: Die Energiewirtschaft ist bei der Herstellung wichtiger Teile für die Stromerzeugung, darunter Turbinen, Generatoren und Getriebekomponenten, auf Präzisionsbearbeitung angewiesen.
- Werkzeug- und Formenbau: Präzisionsbearbeitung ist bei der Herstellung von Werkzeugen und Formen von entscheidender Bedeutung, die wiederum zur Herstellung unzähliger anderer Produkte verwendet werden.
- Consumer Elektronik: Die Produktion von Smartphones, Laptops und anderer Unterhaltungselektronik profitiert von der Präzisionsbearbeitung, um schlankes Design und optimale Funktionalität zu gewährleisten.
- Forschung und Entwicklung: Forscher und Wissenschaftler sind auf präzisionsgefertigte Komponenten für Experimente, Prototypen und Laborgeräte angewiesen.
C. Historische Perspektive
Die Reise der Präzisionsbearbeitung reicht bis in alte Zivilisationen zurück, in denen geschickte Handwerker rudimentäre Werkzeuge zur Formung von Materialien verwendeten. Allerdings war die damals erreichte Präzision im Vergleich zu heutigen Standards begrenzt.- Frühe Präzisionsbearbeitung: Die industrielle Revolution des 18. und 19. Jahrhunderts markierte eine entscheidende Periode in der Entwicklung der Präzisionsbearbeitung. Die Erfindung von Werkzeugmaschinen wie Dreh- und Fräsmaschinen revolutionierte die Fertigung, indem sie eine höhere Genauigkeit und Konsistenz ermöglichte.
- Dem Zweiten Weltkrieg: Die Präzisionsbearbeitung spielte im Zweiten Weltkrieg eine entscheidende Rolle, da sie für die Herstellung militärischer Ausrüstung mit der erforderlichen Präzision und Einheitlichkeit unerlässlich war. In dieser Ära gab es Fortschritte bei den Bearbeitungstechniken und die Entstehung neuer Materialien.
- Fortschritte der Nachkriegszeit: In der Nachkriegszeit kam es zu einem Anstieg technologischer Innovationen, einschließlich der Verwendung von CNC-Maschinen (Computer Numerical Control). CNC-Bearbeitung ermöglichte automatisierte und hochpräzise Abläufe und läutete eine neue Ära der Fertigung ein.
- Das digitale Zeitalter: Die Integration von Computern und Software in Bearbeitungsprozesse hat die Präzisionsbearbeitung weiter gesteigert. Moderne CNC-Maschinen können komplexe Vorgänge mit beispielloser Genauigkeit ausführen und sind daher in der heutigen Fertigungslandschaft unverzichtbar.
Materialien und ihre Bedeutung
Materialien sind die Grundlage der Präzisionsbearbeitung, und die Auswahl des richtigen Materials spielt eine entscheidende Rolle bei der Herstellung hochpräziser Teile. In diesem Abschnitt befassen wir uns mit der Bedeutung der Auswahl geeigneter Materialien, verstehen die Bedeutung der Materialeigenschaften und untersuchen die verschiedenen Faktoren, die sich auf die Bearbeitbarkeit auswirken.A. Auswahl der Materialien
Die Wahl der Materialien bei der Präzisionsbearbeitung ist eine entscheidende Entscheidung, die sich direkt auf die Leistung, Haltbarkeit und Funktionalität des Endprodukts auswirkt. Hersteller müssen bei der Materialauswahl mehrere Faktoren berücksichtigen:- Materialeignung: Das Material muss für den vorgesehenen Einsatzzweck geeignet sein. Unterschiedliche Branchen und Anwendungen stellen unterschiedliche Anforderungen, wie z. B. Temperaturbeständigkeit, Korrosionsbeständigkeit und elektrische Leitfähigkeit.
- Mechanische Eigenschaften: Mechanische Eigenschaften wie Zugfestigkeit, Härte und Duktilität sind entscheidend. Beispielsweise werden in der Luft- und Raumfahrt Materialien mit hoher Zugfestigkeit für Strukturbauteile bevorzugt.
- Thermische Eigenschaften: Einige Anwendungen erfordern Materialien mit ausgezeichneter Wärmeleitfähigkeit oder Beständigkeit gegenüber hohen Temperaturen. Dies ist besonders wichtig in Branchen wie der Energieerzeugung und der Elektronik.
- Korrosionsbeständigkeit: In Umgebungen, in denen Korrosion ein Problem darstellt, werden Materialien mit hoher Korrosionsbeständigkeit wie Edelstahl oder Titan bevorzugt.
- Überlegungen zum Gewicht: Branchen wie die Automobil- und die Luft- und Raumfahrtindustrie legen häufig Wert auf leichte Materialien wie Aluminium oder Kohlefaserverbundwerkstoffe, um den Kraftstoffverbrauch zu senken und die Leistung zu steigern.
- Kostenbeschränkungen: Die Kosten sind ein wesentlicher Faktor bei der Materialauswahl. Hochleistungsmaterialien können teuer sein, daher müssen Hersteller ein Gleichgewicht zwischen Leistung und Kosteneffizienz finden.
- Erfüllung gesetzlicher Auflagen: In Branchen wie dem Gesundheitswesen müssen Materialien strenge regulatorische Standards für Biokompatibilität und Sicherheit erfüllen.
- Verfügbarkeit: Auch die Verfügbarkeit von Materialien und deren Quellen beeinflussen die Auswahl. Einige Speziallegierungen oder Verbundwerkstoffe sind möglicherweise nur begrenzt verfügbar.
B. Materialeigenschaften
Das Verständnis der Materialeigenschaften ist für die Präzisionsbearbeitung von entscheidender Bedeutung. Hier sind einige wichtige Materialeigenschaften und ihre Bedeutung:- Zugfestigkeit: Die Zugfestigkeit misst die Fähigkeit eines Materials, einer Zugkraft standzuhalten, ohne zu brechen. Es ist für Strukturbauteile und Teile, die mechanischer Beanspruchung ausgesetzt sind, unerlässlich.
- Härte: Die Härte gibt den Widerstand eines Materials gegen Verformung und Verschleiß an. Harte Materialien eignen sich für Schneidwerkzeuge, während für bestimmte Anwendungen, beispielsweise Dichtungen, weichere Materialien bevorzugt werden können.
- Duktilität: Unter Duktilität versteht man die Fähigkeit eines Materials, sich unter Zugbeanspruchung zu verformen, ohne zu brechen. Duktile Materialien lassen sich leichter formen, sind jedoch möglicherweise nicht für Anwendungen geeignet, die Steifigkeit erfordern.
- Wärmeleitfähigkeit: Materialien mit hoher Wärmeleitfähigkeit leiten Wärme effizient ab. Diese Eigenschaft ist bei Anwendungen von entscheidender Bedeutung, bei denen die Temperaturkontrolle von entscheidender Bedeutung ist.
- Elektrische Leitfähigkeit: Elektrische Leitfähigkeit ist in elektronischen und elektrischen Komponenten von entscheidender Bedeutung, wo Materialien den Stromfluss ermöglichen müssen.
- Magnetische Eigenschaften: Magnetische Eigenschaften sind in Branchen wie Elektromagnetik und Elektronik von Bedeutung, in denen Materialien möglicherweise ferromagnetisch oder nicht magnetisch sein müssen.
- Chemische Resistenz: Materialien müssen chemischer Korrosion in Umgebungen widerstehen, in denen sie Säuren, Basen oder anderen korrosiven Substanzen ausgesetzt sind.
C. Bearbeitbarkeitsfaktoren
Bearbeitbarkeit bezieht sich auf die Leichtigkeit, mit der ein Material bearbeitet, geschnitten oder geformt werden kann. Es wird von verschiedenen Faktoren beeinflusst, darunter:- Materialhärte: Weichere Materialien lassen sich im Allgemeinen leichter bearbeiten, während härtere Materialien möglicherweise spezielle Werkzeuge und Techniken erfordern.
- Spanbildung: Die Bildung und Abfuhr von Spänen während der Bearbeitung beeinträchtigt die Effizienz und Oberflächengüte des Prozesses.
- Werkzeugverschleiß: Unterschiedliche Materialien können zu unterschiedlich starkem Werkzeugverschleiß führen, was sich auf die Bearbeitungsgeschwindigkeit und die Kosten auswirkt.
- Kühlmittel und Schmierung: Richtiges Kühlmittel und Schmierung sind unerlässlich, um Reibung, Hitze und Werkzeugverschleiß während der Bearbeitung zu reduzieren.
- Schneidgeschwindigkeit: Die Geschwindigkeit, mit der sich das Schneidwerkzeug durch das Material bewegt, beeinflusst sowohl die Produktivität als auch die Qualität der bearbeiteten Oberfläche.
- Werkzeugmaterial: Die Wahl des Schneidwerkzeugmaterials, z. B. Hartmetall oder Schnellarbeitsstahl, hängt vom zu bearbeitenden Material ab.
- Schnittparameter: Durch Anpassen von Schnittparametern wie Vorschubgeschwindigkeit und Schnitttiefe kann der Bearbeitungsprozess für bestimmte Materialien optimiert werden.
Werkzeugmaschinen für die Präzisionsbearbeitung
Werkzeugmaschinen sind das Herzstück der Präzisionsbearbeitung und ermöglichen die Umwandlung von Rohmaterialien in hochpräzise Teile. In diesem Abschnitt werden wir vier Haupttypen von Werkzeugmaschinen untersuchen, die in der Präzisionsbearbeitung verwendet werden: CNC-Bearbeitungszentren, Drehmaschinen, Schleifmaschinen und EDM (Elektroerosionsbearbeitung). Jede dieser Maschinen spielt eine einzigartige Rolle bei der Herstellung präziser Bauteile.A. CNC-Bearbeitungszentren
CNC-Bearbeitungszentren (Computer Numerical Control) sind vielseitig und werden häufig in der Präzisionsbearbeitung eingesetzt. Dabei handelt es sich um automatisierte Systeme, die die Bewegung von Schneidwerkzeugen und Werkstücken mit außergewöhnlicher Präzision steuern. Hier ein Überblick über CNC-Bearbeitungszentren und ihre Bedeutung:- Vielseitigkeit: CNC-Bearbeitungszentren können verschiedene Bearbeitungsvorgänge ausführen, darunter Fräsen, Bohren und Gewindeschneiden. Diese Vielseitigkeit ermöglicht die Herstellung komplexer Teile mit mehreren Funktionen.
- Hohe Präzision: Die computergestützte Steuerung von CNC-Maschinen sorgt für eine präzise Werkzeugpositionierung und konsistente Ergebnisse und macht sie ideal für Teile mit engen Toleranzen.
- Automation: CNC-Bearbeitungszentren können kontinuierlich und mit minimalem menschlichen Eingriff arbeiten. Diese Automatisierung erhöht die Effizienz und verringert das Fehlerrisiko.
- Komplexe Geometrien: Sie zeichnen sich durch die Bearbeitung komplizierter Formen und Konturen aus und eignen sich daher für Branchen wie die Luft- und Raumfahrt, in denen komplexe Komponenten üblich sind.
- Wiederholbare Ergebnisse: CNC-Maschinen bieten eine hervorragende Wiederholgenauigkeit und stellen sicher, dass jedes produzierte Teil genau den Spezifikationen des Designs entspricht.
- Reduzierte Rüstzeiten: CNC-Bearbeitungszentren können so programmiert werden, dass sie schnell zwischen verschiedenen Aufgaben wechseln können, wodurch Rüstzeiten minimiert und die Produktionseffizienz gesteigert werden.
B. Drehmaschinen
Mit Drehmaschinen werden zylindrische Teile hergestellt, indem ein Werkstück gedreht wird, während ein Schneidwerkzeug Material von seiner Außenfläche entfernt. Sie sind für die Produktion unerlässlich Welles, Stifte und andere Komponenten mit Rotationssymmetrie. Zu den wichtigsten Punkten zu Drehmaschinen gehören:- Zylindrische Teile: Drehmaschinen sind auf die Herstellung von zylindrischen oder rohrförmigen Bauteilen spezialisiert, auch solche mit Gewinden oder komplizierten Nuten.
- Hohe Geschwindigkeiten: Sie arbeiten mit hohen Geschwindigkeiten und eignen sich daher für Teile, die eine glatte und präzise Oberfläche erfordern.
- Einachsiger Betrieb: Die meisten Drehmaschinen sind einachsig und konzentrieren sich auf die Formung der Außenfläche des Werkstücks.
- Effizient für die Massenproduktion: Drehen ist äußerst effizient für die Massenproduktion von Teilen mit minimalem Materialabfall.
- Drehmaschinen: Manuelle und CNC-gesteuerte Drehmaschinen sind häufig verwendete Drehmaschinen und bieten eine Reihe von Funktionen.
C. Schleifmaschinen
Schleifmaschinen sind für die präzise Oberflächenbearbeitung und Formgebung harter oder abrasiver Materialien konzipiert. Sie sind entscheidend für die Erzielung extrem enger Toleranzen und hervorragender Oberflächengüten. Deshalb sind Schleifmaschinen wichtig:- Präzision im Mikrometerbereich: Schleifmaschinen können eine Präzision im Mikrometerbereich erreichen und sind daher unverzichtbar für Anwendungen, die ein Höchstmaß an Genauigkeit erfordern.
- Materialentfernung: Sie entfernen Material durch Abrieb, ermöglichen die Korrektur von Oberflächenfehlern und erzielen eine außergewöhnliche Glätte.
- Werkzeug- und Fräserschleifen: Neben dem Flachschleifen gibt es spezielle Schleifmaschinen zum Schärfen von Schneidwerkzeugen und zur Herstellung präziser Profile.
- Verschiedene Schleifmethoden: Verschiedene Arten von Schleifmaschinen, darunter Flachschleifmaschinen, Rundschleifmaschinen und Spitzenlosschleifmaschinen, erfüllen unterschiedliche Bearbeitungsanforderungen.
- Gehärtete Materialien: Schleifen eignet sich besonders für gehärtete Materialien wie Werkzeugstahl und Keramik, bei denen herkömmliche Bearbeitungsmethoden möglicherweise unwirksam sind.
D. EDM (elektrische Entladungsbearbeitung)
EDM oder Electrical Discharge Machining ist ein nicht-traditioneller Bearbeitungsprozess, bei dem elektrische Entladungen zum Formen von Materialien verwendet werden. Es ist ideal für die Herstellung komplizierter und empfindlicher Teile, bei denen herkömmliche Schneidwerkzeuge Schäden verursachen können. Zu den wichtigsten Aspekten von EDM gehören:- Kein physischer Kontakt: Beim EDM kommt es nicht zu einem direkten physischen Kontakt zwischen Werkzeug und Werkstück, wodurch das Risiko von Werkzeugverschleiß und Beschädigung zerbrechlicher Materialien minimiert wird.
- Hohe Präzision: Selbst bei außergewöhnlich harten Materialien kann eine hohe Präzision und Oberflächengüte erzielt werden.
- Drahterodieren und Senkerodieren: Es gibt zwei Haupttypen von Erodiermaschinen: Kabel schneiden Erodieren, bei dem eine Drahtelektrode verwendet wird, und Senkerodieren, bei dem eine geformte Elektrode verwendet wird.
- Komplexe Formen: Mit der Funkenerosion können komplexe Formen wie Matrizen und Gussformen mit komplizierten Details und feinen Merkmalen hergestellt werden.
- Wärmeeinflusszone: Da EDM am Werkstück keine Wärme erzeugt, eignet es sich für wärmeempfindliche Materialien wie Luftfahrtlegierungen.
- Langsamer Prozess: EDM ist im Vergleich zu anderen Bearbeitungsmethoden relativ langsam und eignet sich daher am besten für Arbeiten mit geringer Stückzahl und hoher Präzision.
Schneidwerkzeuge und Werkzeuge
Schneidwerkzeuge stehen an der Spitze der Präzisionsbearbeitung und dienen als Instrumente, die Rohmaterialien formen und in hochpräzise Teile umwandeln. In diesem Abschnitt befassen wir uns mit den verschiedenen Arten von Schneidwerkzeugen, der Bedeutung von Werkzeugbeschichtungen und den Faktoren, die sich auf die Lebensdauer und den Verschleiß von Werkzeugen auswirken.A. Arten von Schneidwerkzeugen
Die Präzisionsbearbeitung basiert auf einer Vielzahl von Schneidwerkzeugen, die jeweils für bestimmte Aufgaben und Materialien entwickelt wurden. Die Wahl des Schneidwerkzeugs hat großen Einfluss auf die Effizienz und Genauigkeit des Bearbeitungsprozesses. Hier sind einige gängige Arten von Schneidwerkzeugen:- End Mills: Schaftfräser sind vielseitige Werkzeuge für Fräsarbeiten. Sie verfügen über mehrere Schneidkanten und können auf verschiedene Arten Material vom Werkstück entfernen, einschließlich Planen, Konturieren und Schlitzen.
- Bohrer: Bohrer sind für die Herstellung von Löchern in Werkstücken konzipiert. Es gibt sie in verschiedenen Formen, darunter Spiralbohrer, Zentrierbohrer und Wendeschneidplattenbohrer.
- Wendeeinsätze: Diese werden in Drehmaschinen verwendet, um zylindrische Teile zu formen. Dreheinsätze sind in verschiedenen Formen und Materialien für unterschiedliche Anwendungen erhältlich.
- Fräser: Fräser gibt es in verschiedenen Formen, z. B. als Planfräser, Kugelfräser und Schlitzfräser, und werden in Fräsmaschinen verwendet, um verschiedene Merkmale am Werkstück zu erzeugen.
- Reibahlen: Reibahlen werden zum Fertigstellen und Anpassen zuvor gebohrter Löcher auf präzise Abmessungen verwendet. Sie sorgen für glatte und präzise Lochoberflächen.
- Gewindebohrer und Matrizen: Diese Schneidwerkzeuge werden zum Gewindeschneiden verwendet. Gewindebohrer erzeugen Innengewinde, während Matrizen Außengewinde erzeugen.
- Schleifscheiben: Schleifscheiben sind Schleifwerkzeuge, die zum Präzisionsschleifen von Oberflächen verwendet werden. Sie sind in verschiedenen Schleifmaterialien und Körnungen erhältlich.
- Broschen: Räumnadeln sind Spezialwerkzeuge zum Schneiden von Innen- und Außenformen und Profilen wie Keilnuten und Keilnuten.
- Senker und Senker: Mit diesen Werkzeugen werden Aussparungen oder Fasen um Löcher herum erstellt Verschlusss.
- Bohrstangen: Bohrstangen werden bei Bohrvorgängen verwendet, um vorhandene Löcher präzise zu vergrößern.
B. Werkzeugbeschichtungen
Werkzeugbeschichtungen sind dünne Materialschichten, die auf Schneidwerkzeuge aufgetragen werden, um deren Leistung und Haltbarkeit zu verbessern. Diese Beschichtungen bieten mehrere Vorteile:- Reduzierte Reibung: Beschichtungen wie Titannitrid (TiN) und Titancarbonitrid (TiCN) verringern die Reibung zwischen Werkzeug und Werkstück und führen so zu einem gleichmäßigeren Schnitt und einer längeren Werkzeuglebensdauer.
- Erhöhte Härte: Beschichtungen erhöhen die Härte der Werkzeugoberfläche, machen sie widerstandsfähiger gegen Verschleiß und verlängern die Lebensdauer des Werkzeugs.
- Verbesserte Hitzebeständigkeit: Beschichtungen halten hohen Temperaturen stand, die bei der Bearbeitung entstehen, wodurch der hitzebedingte Werkzeugverschleiß reduziert und die Schnittgeschwindigkeit erhöht wird.
- Anti-Aufbau-Eigenschaften: Einige Beschichtungen haben Antihafteigenschaften und verhindern so die Ansammlung von Material an den Schneidkanten des Werkzeugs.
- Erhöhte Schmierfähigkeit: Beschichtete Werkzeuge verfügen über eine verbesserte Schmierfähigkeit, wodurch der Bedarf an übermäßigem Kühlmittel verringert und die Spanabfuhr verbessert wird.
C. Standzeit und Verschleiß
Das Verständnis der Werkzeuglebensdauer und des Verschleißes ist entscheidend für die Optimierung von Bearbeitungsprozessen und die Minimierung der Produktionskosten. Unter Werkzeuglebensdauer versteht man die Dauer, die ein Schneidwerkzeug wirksam bleibt, bevor es ausgetauscht oder überholt werden muss. Mehrere Faktoren beeinflussen die Standzeit und den Verschleiß von Werkzeugen:- Schneidgeschwindigkeit: Höhere Schnittgeschwindigkeiten können aufgrund der bei der Bearbeitung entstehenden höheren Temperaturen zu einem erhöhten Werkzeugverschleiß führen. Die richtige Auswahl der Schnittgeschwindigkeiten ist für das Gleichgewicht zwischen Werkzeugstandzeit und Produktivität von entscheidender Bedeutung.
- Vorschubgeschwindigkeit: Die Geschwindigkeit, mit der das Schneidwerkzeug in das Werkstück vordringt, beeinflusst den Werkzeugverschleiß. Hohe Vorschübe können den Verschleiß beschleunigen, während niedrigere Vorschübe die Standzeit des Werkzeugs verlängern können.
- Schnitttiefe: Die Schnitttiefe beeinflusst die Menge des pro Durchgang entfernten Materials. Tiefere Schnitte können den Werkzeugverschleiß erhöhen, daher ist die Optimierung der Tiefe von entscheidender Bedeutung.
- Materialhärte: Das Schneiden harter Materialien kann den Werkzeugverschleiß beschleunigen. Zur effektiven Bearbeitung harter Werkstoffe werden spezielle Werkzeuge und Beschichtungen eingesetzt.
- Kühlmittel und Schmierung: Richtiges Kühlmittel und Schmierung tragen zur Wärmeableitung bei, verringern die Reibung und verlängern so die Lebensdauer des Werkzeugs.
- Werkzeugmaterial: Das Material, aus dem das Schneidwerkzeug besteht, beeinflusst seine Verschleißfestigkeit. Materialien wie Hartmetall und Keramik bieten eine hervorragende Verschleißfestigkeit.
- Werkzeuggeometrie: Die Geometrie des Schneidwerkzeugs, einschließlich Spanwinkel, Freiwinkel und Spanbrecherdesign, spielt eine wichtige Rolle bei den Verschleißmustern.
- Werkstückmaterial: Die Art des bearbeiteten Materials beeinflusst den Werkzeugverschleiß. Abrasive Materialien können zu einem schnelleren Werkzeugverschleiß führen.
Präzisionsbearbeitungsprozesse
Präzisionsbearbeitungsprozesse sind die Methoden, mit denen Rohmaterialien in hochpräzise Teile mit engen Toleranzen und außergewöhnlichen Oberflächengüten umgewandelt werden. In diesem Abschnitt werden wir fünf wichtige Präzisionsbearbeitungsprozesse untersuchen: Drehen, Fräsen, Bohren, Schleifen und Funkenerosion (EDM). Jeder dieser Prozesse dient einem einzigartigen Zweck und wird basierend auf den spezifischen Anforderungen des Werkstücks eingesetzt.A. Drehen
Drehen ist ein Bearbeitungsverfahren, das hauptsächlich zur Formung zylindrischer Teile eingesetzt wird. Dabei wird ein Werkstück gedreht, während ein Einschneidewerkzeug Material von der Außenfläche entfernt. Hier sind die wichtigsten Aspekte des Drehens:- Zylindrische Teile: Drehen ist ideal für die Herstellung zylindrischer Bauteile wie Wellen, Stifte und Hülsen.
- Rotationssymmetrie: Es eignet sich gut für Teile, die Rotationssymmetrie erfordern, da das Werkstück auf einer Drehmaschine rotiert, während das Schneidwerkzeug es formt.
- Verschiedene Operationen: Beim Drehen können verschiedene Vorgänge durchgeführt werden, darunter Plandrehen, Drehen (Durchmesserreduzierung), Kegeldrehen und Gewindeschneiden.
- Einpunktschneiden: Ein einzelnes Schneidwerkzeug entfernt Material in einer kontinuierlichen Bewegung, was zu einem effizienten Materialabtrag führt.
- Drehmaschinen: Für Dreharbeiten werden üblicherweise sowohl manuelle als auch CNC-gesteuerte Drehmaschinen eingesetzt.
B. Fräsen
Fräsen ist ein vielseitiger Präzisionsbearbeitungsprozess, bei dem Mehrpunkt-Schneidwerkzeuge eingesetzt werden, um Material von einem Werkstück zu entfernen. Es eignet sich gut für die Gestaltung verschiedenster Formen und Merkmale. Zu den wichtigsten Aspekten des Fräsens gehören:- Vielseitigkeit: Durch Fräsen können ebene Flächen, Schlitze, Taschen und komplexe Konturen erzeugt werden. Es wird sowohl für die 2D- als auch für die 3D-Bearbeitung verwendet.
- Mehrpunktschneiden: Mehrere Schneidkanten am Werkzeug interagieren gleichzeitig mit dem Werkstück und ermöglichen so einen effizienten Materialabtrag.
- Arten des Fräsens: Das Fräsen kann mit verschiedenen Arten von Fräsern durchgeführt werden, darunter Schaftfräser, Planfräser und Kugelfräser.
- CNC-Bearbeitungszentren: CNC-gesteuerte Fräsmaschinen bieten eine präzise Kontrolle über die Werkzeugbewegung und werden häufig in der modernen Bearbeitung eingesetzt.
- Hohe Geschwindigkeiten: Das Fräsen kann mit hohen Geschwindigkeiten durchgeführt werden, was eine effiziente Produktion ermöglicht.
C. Bohren
Bohren ist ein Präzisionsbearbeitungsverfahren zur Herstellung von Löchern in Werkstücken. Es ist ein grundlegender Vorgang in verschiedenen Branchen. Zu den wichtigsten Aspekten des Bohrens gehören:- Locherstellung: Bohrmaschinen verwenden spezielle Werkzeuge, sogenannte Bohrer, um Material zu entfernen und Löcher mit bestimmten Durchmessern zu erzeugen.
- Arten von Bohrern: Es stehen verschiedene Bohrertypen zur Verfügung, darunter Spiralbohrer, Zentrierbohrer und Wendeschneidplattenbohrer, die jeweils für bestimmte Anwendungen konzipiert sind.
- Genauigkeit: Präzise Positionierung und Ausrichtung sind beim Bohren unerlässlich, um sicherzustellen, dass Löcher präzise erstellt werden.
- Geschwindigkeit und Vorschub: Bohrparameter wie Drehzahl und Vorschub sind entscheidend für das Erreichen der gewünschten Lochabmessungen.
- Kühlmittel und Schmierung: Um die Wärme abzuleiten und die Reibung beim Bohren zu verringern, werden geeignete Kühlmittel und Schmiermittel verwendet.
D. Schleifen
Schleifen ist ein Präzisionsbearbeitungsprozess, bei dem Schleifscheiben eingesetzt werden, um Material abzutragen und extrem enge Toleranzen und Oberflächengüten zu erzielen. Zu den wichtigsten Aspekten des Schleifens gehören:- Außergewöhnliche Präzision: Beim Schleifen kann eine Präzision im Mikrometerbereich erreicht werden, was es ideal für Anwendungen macht, die höchste Genauigkeit erfordern.
- Oberflächenfinish: Es erzeugt hervorragende Oberflächengüten und macht häufig zusätzliche Nachbearbeitungsprozesse überflüssig.
- Materialien: Das Schleifen eignet sich für harte und abrasive Materialien, einschließlich gehärtetem Stahl, Keramik und Karbiden.
- Verschiedene Schleifmethoden: Verschiedene Arten von Schleifmaschinen, wie z. B. Flachschleifmaschinen, Rundschleifmaschinen und Spitzenlosschleifmaschinen, erfüllen unterschiedliche Bearbeitungsanforderungen.
- Kühlmittel: Beim Schleifen ist das richtige Kühlmittel unerlässlich, um eine Überhitzung zu verhindern und die Integrität der Scheibe aufrechtzuerhalten.
E. Funkenerosion (EDM)
EDM oder Electrical Discharge Machining ist ein nicht-traditionelles Präzisionsbearbeitungsverfahren, bei dem elektrische Entladungen zum Abtragen von Material verwendet werden. Sie eignet sich besonders für die Bearbeitung komplexer und komplizierter Formen sowie harter und hitzebeständiger Materialien. Zu den wichtigsten Aspekten von EDM gehören:- Berührungslose Bearbeitung: Beim EDM kommt es nicht zu einem direkten Kontakt zwischen Werkzeug und Werkstück, wodurch das Risiko von Werkzeugverschleiß und -schäden verringert wird.
- Hohe Präzision: EDM kann eine hohe Präzision erreichen und eignet sich daher für Anwendungen, bei denen enge Toleranzen unerlässlich sind.
- Komplexe Formen: Es zeichnet sich durch die Bearbeitung komplexer Formen, Matrizen, Gussformen und Komponenten mit feinen Details aus.
- Drahterodieren und Senkerodieren: Es gibt zwei Haupttypen von Erodiermaschinen: Drahterodiermaschine, die eine Drahtelektrode verwendet, und Senkerodiermaschine, die eine geformte Elektrode verwendet.
- Langsamer Prozess: EDM ist im Vergleich zu anderen Bearbeitungsmethoden relativ langsam und eignet sich daher am besten für Arbeiten mit geringer Stückzahl und hoher Präzision.
Toleranzen und Qualitätskontrolle
Präzisionsbearbeitung erfordert viel Liebe zum Detail und eine strikte Verpflichtung zur Qualitätskontrolle, um sicherzustellen, dass die Teile den festgelegten Standards entsprechen. In diesem Abschnitt werden wir drei kritische Aspekte der Qualitätskontrolle bei der Präzisionsbearbeitung untersuchen: Geometrische Bemaßung und Toleranz (GD&T), statistische Prozesskontrolle (SPC) und Qualitätssicherung.A. Geometrische Bemaßung und Toleranzen (GD&T)
Geometrische Bemaßung und Toleranz, oft als GD&T abgekürzt, ist ein System zur Definition und Kommunikation der zulässigen Abweichungen in Größe, Form, Ausrichtung und Position von Merkmalen an einem Teil. GD&T ist aus folgenden Gründen für die Präzisionsbearbeitung von entscheidender Bedeutung:- Präzise Kommunikation: GD&T bietet eine standardisierte Sprache für Ingenieure, Designer und Maschinisten, um Konstruktionsabsichten und Maßanforderungen genau zu kommunizieren.
- Toleranzklärung: Es hilft bei der Definition der akzeptablen Abweichung in kritischen Dimensionen und stellt sicher, dass alle Beteiligten die zulässigen Abweichungen verstehen.
- Verbesserte Qualität: GD&T fördert eine verbesserte Qualität, indem Unklarheiten in den Konstruktionsspezifikationen reduziert und das Risiko von Fehlern während der Bearbeitung minimiert werden.
- Kosteneffizienz: Klare GD&T-Spezifikationen können zu geringeren Herstellungskosten führen, da die Wahrscheinlichkeit geringer ist, dass Teile verschrottet werden oder aufgrund von Missverständnissen oder Fehlinterpretationen nachgearbeitet werden müssen.
- Komplexe Geometrie: Dies ist besonders nützlich für Teile mit komplexen Geometrien und stellt sicher, dass alle Merkmale gemäß den gewünschten Spezifikationen hergestellt werden.
B. Statistische Prozesskontrolle (SPC)
Statistische Prozesskontrolle (SPC) ist eine Qualitätskontrollmethode, die statistische Techniken zur Überwachung und Steuerung des Bearbeitungsprozesses verwendet. SPC ist aus folgenden Gründen für die Präzisionsbearbeitung unerlässlich:- Prozessüberwachung: SPC hilft, Bearbeitungsprozesse in Echtzeit zu überwachen und Variationen oder Abweichungen von den gewünschten Parametern zu identifizieren.
- Früherkennung von Problemen: Durch die kontinuierliche Überwachung des Prozesses ermöglicht SPC die frühzeitige Erkennung von Problemen, die zu Teilen führen könnten, die nicht den Spezifikationen entsprechen, wodurch Abfall und Nacharbeit reduziert werden.
- Datengesteuerte Entscheidungsfindung: SPC stützt sich auf Daten und statistische Analysen, um fundierte Entscheidungen über Prozessanpassungen zu treffen und sicherzustellen, dass der Bearbeitungsprozess innerhalb akzeptabler Grenzen bleibt.
- Verbesserte Konsistenz: SPC fördert die Prozesskonsistenz und verringert die Wahrscheinlichkeit, fehlerhafte Teile zu produzieren.
- Reduzierter Ausschuss und Nacharbeit: Durch die sofortige Identifizierung und Behebung von Prozessabweichungen minimiert SPC die Produktion fehlerhafter Teile und reduziert Ausschuss- und Nacharbeitskosten.
C. Qualitätssicherung in der Präzisionsbearbeitung
Die Qualitätssicherung in der Präzisionsbearbeitung umfasst einen umfassenden Ansatz, um sicherzustellen, dass hergestellte Teile bestimmte Qualitätsstandards erfüllen oder übertreffen. Es umfasst verschiedene Elemente, darunter:- Prozessdokumentation: Eine detaillierte Dokumentation der Bearbeitungsprozesse, einschließlich Standardarbeitsanweisungen (SOPs) und Arbeitsanweisungen, stellt sicher, dass jeder Schritt konsistent ausgeführt wird.
- Inspektion und Messung: Durch strenge Inspektionen und Messungen mithilfe von Präzisionsinstrumenten und Messtechniken wird sichergestellt, dass die Teile den festgelegten Toleranzen und Qualitätsstandards entsprechen.
- Kalibrierung: Eine regelmäßige Kalibrierung von Bearbeitungsgeräten und Messgeräten ist für die Aufrechterhaltung der Genauigkeit und Rückverfolgbarkeit unerlässlich.
- Materialprüfung: Die Überprüfung der Materialeigenschaften, der Zusammensetzung und der Qualität ist entscheidend, um sicherzustellen, dass das verwendete Material den Designanforderungen entspricht.
- Angestellten Training: Schulungs- und Kompetenzentwicklungsprogramme für Maschinisten und Qualitätskontrollpersonal stellen sicher, dass sie ihre Rollen und Verantwortlichkeiten beherrschen.
- Ursachenanalyse: Wenn nicht konforme Teile identifiziert werden, wird eine Ursachenanalyse durchgeführt, um die Ursache des Problems zu ermitteln und Korrekturmaßnahmen umzusetzen.
- FORTLAUFENDE VERBESSERUNGEN: Eine Kultur der kontinuierlichen Verbesserung fördert Innovation und treibt die kontinuierliche Verbesserung der Bearbeitungsprozesse und Qualitätskontrollverfahren voran.
- Kundenfeedback: Das Sammeln und Analysieren von Kundenfeedback hilft dabei, Verbesserungsmöglichkeiten zu identifizieren und Bearbeitungsprozesse an den Kundenerwartungen auszurichten.
Zusammenfassung
A. Die Kunst und Wissenschaft der Präzisionsbearbeitung
Die Präzisionsbearbeitung steht an der Schnittstelle von Kunst und Wissenschaft, wo Kreativität, Können und Innovation zusammenkommen, um hochpräzise Teile herzustellen, die Industrien vorantreiben und die moderne Welt prägen. Es handelt sich sowohl um eine Kunstform, die das handwerkliche Können und die Fachkenntnis von Maschinisten erfordert, die Rohstoffe in technische Spitzenleistungen verwandeln, als auch um eine Wissenschaft, die sich auf modernste Technologie, Materialwissenschaft und fortschrittliche Prozesse verlässt, um beispiellose Präzision zu erreichen. Der Weg der Präzisionsbearbeitung führt uns durch das Verständnis von Materialien und ihren Eigenschaften, die Beherrschung von Schneidwerkzeugen und -maschinen sowie die sorgfältige Kontrolle von Prozessen und Toleranzen. Es umfasst die Sprache der geometrischen Bemaßung und Toleranzen, die Wachsamkeit der statistischen Prozesskontrolle und die Verpflichtung zur Qualitätssicherung. Die Präzisionsbearbeitung spielt in verschiedenen Branchen eine zentrale Rolle, von der Luft- und Raumfahrt über die Automobilindustrie bis hin zu medizinischen Geräten und Elektronik, und formt alles von Flugzeugtriebwerken bis hin zu künstlichen Gelenken und Mikrochips. Es ermöglicht die Herstellung von Komponenten, die mit unübertroffener Genauigkeit und Zuverlässigkeit arbeiten und oft die Grenzen des Möglichen überschreiten.B. Abschließende Gedanken
Am Ende dieser Untersuchung der Präzisionsbearbeitung wird deutlich, dass es in diesem Bereich nicht nur um die Herstellung von Teilen geht; es geht um die Schaffung von Möglichkeiten. Das Streben nach Präzision treibt Innovationen voran und verschiebt die Grenzen des Machbaren. Ganz gleich, ob es sich um die feine Handwerkskunst handelt, die zur Herstellung der komplizierten Zahnräder einer Uhr erforderlich ist, oder um die fortschrittliche Technologie, die zur Herstellung komplexer Komponenten für die Luft- und Raumfahrt erforderlich ist – die Präzisionsbearbeitung steht im Mittelpunkt. Die Zukunft der Präzisionsbearbeitung ist vielversprechend. Fortschritte in der Materialwissenschaft, Automatisierung und digitalen Technologien verändern die Landschaft weiterhin. Miniaturisierung, 3D-Druck und nachhaltige Herstellungsverfahren gewinnen zunehmend an Bedeutung und eröffnen der Branche neue Horizonte. In einer Welt, in der Präzision wichtiger denn je ist, bleibt die Präzisionsbearbeitung eine unverzichtbare Säule der modernen Technik. Es ist ein Beweis für den menschlichen Einfallsreichtum und unser unnachgiebiges Streben nach Exzellenz in allen Aspekten der Fertigung. Da die Nachfrage nach höherer Präzision und komplexeren Komponenten wächst, wird sich die Präzisionsbearbeitung weiterentwickeln und die Herausforderungen von morgen mit der gleichen Hingabe und Präzision meistern, die sie seit Jahrhunderten auszeichnen.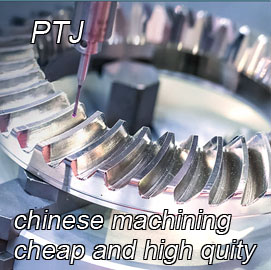
Unsere Leistungen
- 5-Achsen-Bearbeitung
- CNC-Fräsen
- CNC drehen
- Bearbeitungsindustrie
- Bearbeitungsprozess
- Oberflächenbearbeitung
- Metallbearbeitung
- Kunststoffbearbeitung
- Pulvermetallurgie-Form
- Druckguss
- Teile Galerie
Fallstudien
- Autoteile aus Metall
- Maschinenteile
- LED-Kühlkörper
- Gebäudeteile
- Mobilteile
- Medizinische Teile
- Electronic Parts
- Maßgeschneiderte Bearbeitung
- Fahrradteile
Material Liste
- Aluminiumbearbeitung
- Titanbearbeitung
- Edelstahlbearbeitung
- Kupferbearbeitung
- Messingbearbeitung
- Bearbeitung von Superlegierungen
- Peek-Bearbeitung
- UHMW-Bearbeitung
- Einzelbearbeitung
- PA6-Bearbeitung
- PPS-Bearbeitung
- Teflon-Bearbeitung
- Inconel-Bearbeitung
- Werkzeugstahlbearbeitung
- Mehr Material
Teile Galerie