Wie man CNC-Werkzeugmaschinen richtig zusammenbaut und installiert und gute Tipps
2023-10-30
Kapitel 1: CNC-Maschinen verstehen
In diesem Kapitel legen wir den Grundstein, indem wir untersuchen, was CNC-Maschinen sind, welche verschiedenen Typen es gibt und welche Schlüsselkomponenten eine CNC-Maschine ausmacht.A. Was ist eine CNC-Maschine?
Eine CNC-Maschine, kurz für Computer Numerical Control Machine, ist ein hochentwickeltes Gerät, das in der Fertigung und Fertigung verwendet wird Bearbeitungsprozesses. Im Gegensatz zu herkömmlichen Maschinen, die manuell von menschlichen Bedienern bedient werden, werden CNC-Maschinen automatisiert und von Computern gesteuert, was präzise und hochgradig wiederholbare Vorgänge ermöglicht. Diese Maschinen sind in der Lage, komplexe Aufgaben wie Schneiden, Bohren, Fräsen und Formen von Materialien wie Metall, Kunststoff, Holz und mehr auszuführen. Das Herzstück einer CNC-Maschine ist ihre Fähigkeit, Befehle aus Software für computergestütztes Design (CAD) oder computergestützte Fertigung (CAM) zu interpretieren und auszuführen. Diese Software generiert eine Reihe numerischer Codes, oft auch als G-Codes und M-Codes bezeichnet, die der CNC-Maschine Anweisungen geben, wie sie ihre Schneidwerkzeuge und ihr Werkstück bewegen muss, um das gewünschte Ergebnis zu erzielen. CNC-Maschinen haben die Fertigungsindustrie revolutioniert, indem sie die Effizienz steigern, menschliches Versagen reduzieren und die Produktion komplexer und kundenspezifischer Komponenten ermöglichen.B. Arten von CNC-Maschinen
CNC-Maschinen gibt es in verschiedenen Ausführungen, die jeweils für bestimmte Anwendungen und Branchen konzipiert sind. Hier sind einige gängige Arten von CNC-Maschinen:- CNC Fräsen Maschinen: Mit diesen Maschinen werden Materialien durch rotierende Schneidwerkzeuge geschnitten und geformt. Sie werden häufig in Branchen wie der Luft- und Raumfahrt, der Automobilindustrie und der Metallverarbeitung für Aufgaben wie Bohren, Fräsen und Gravieren eingesetzt.
- CNC-Drehmaschinen: CNC-Drehmaschinen sind so konzipiert, dass sie das Werkstück drehen, während mit einem Schneidwerkzeug Material daraus entfernt wird. Sie sind unverzichtbar für die Herstellung zylindrischer Bauteile, wie z Welles und Buchses.
- CNC-Fräser: Diese Maschinen werden hauptsächlich zum Schneiden und Formen von Materialien wie Holz, Kunststoff und Verbundwerkstoffen verwendet. CNC-Fräsmaschinen sind in der Holzverarbeitungs- und Schilderindustrie weit verbreitet.
- CNC-Plasmaschneider: CNC-Plasmaschneider eignen sich ideal zum Schneiden von Metallblechen und verwenden einen Hochgeschwindigkeitsstrahl aus ionisiertem Gas, um Material zu schmelzen und zu entfernen. Sie sind in der Metallverarbeitung und der Automobilindustrie beschäftigt.
- CNC-Laserschneider: Laserschneidmaschinen verwenden einen leistungsstarken Laserstrahl, um verschiedene Materialien, darunter Metalle, Kunststoffe und Textilien, präzise zu schneiden oder zu gravieren. Sie finden Anwendung in Branchen, die von der Schmuckherstellung bis zur industriellen Fertigung reichen.
- CNC-Wasserstrahlschneider: Wasserstrahlschneider verwenden einen Hochdruckwasserstrahl, der mit Schleifpartikeln vermischt ist, um Materialien zu durchtrennen. Sie eignen sich zum Schneiden verschiedenster Materialien, darunter Stein, Glas und Metalle.
- CNC-Erodiermaschinen: Elektroerosionsmaschinen (EDM) nutzen elektrische Entladungen, um Material vom Werkstück zu erodieren. Sie werden für filigrane und hochpräzise Aufgaben insbesondere im Werkzeug- und Formenbau eingesetzt.
C. Komponenten einer CNC-Maschine
Das Verständnis der Komponenten einer CNC-Maschine ist für einen effektiven Betrieb und eine effektive Wartung von entscheidender Bedeutung. Hier sind die Schlüsselkomponenten, die in den meisten CNC-Maschinen zu finden sind:- Maschinenrahmen: Der Maschinenrahmen dient als struktureller Träger für die gesamte CNC-Maschine. Es besteht in der Regel aus hochbelastbaren Materialien, um Stabilität und Steifigkeit während des Betriebs zu gewährleisten.
- Spindel: Die Spindel ist eine motorisierte Komponente, die für das Halten und Drehen von Schneidwerkzeugen oder Anbaugeräten verantwortlich ist. Es spielt eine entscheidende Rolle für die Präzision und Geschwindigkeit des Bearbeitungsprozesses.
- Achsensystem: CNC-Maschinen arbeiten entlang mehrerer Achsen, die üblicherweise mit X, Y und Z bezeichnet werden. Diese Achsen definieren die Bewegung der Maschine im dreidimensionalen Raum. Einige Maschinen verfügen möglicherweise über zusätzliche Rotationsachsen, z. B. A, B und C, für komplexere Vorgänge.
- Werkzeugwechsler: Viele CNC-Maschinen sind mit automatischen Werkzeugwechslern ausgestattet, die einen schnellen Wechsel der Schneidwerkzeuge während eines Bearbeitungsprozesses ermöglichen. Dies verbessert die Effizienz und reduziert Ausfallzeiten.
- Schalttafel: Das Bedienfeld enthält die Schnittstelle, über die Bediener oder Programmierer Befehle eingeben, Programme laden und den Maschinenstatus überwachen können.
- Arbeitstisch oder Werkstückhaltesystem: Auf dem Arbeitstisch wird das Werkstück während der Bearbeitung sicher fixiert. Verschiedene Werkstückhaltevorrichtungen wie Zwingen, Schraubstöcke usw Armaturen, werden verwendet, um sicherzustellen, dass das Werkstück stabil und richtig positioniert bleibt.
- Fahrsystem: Das Antriebssystem besteht aus Motoren und Aktoren, die für die Bewegung der Maschinenkomponenten entlang der vorgegebenen Achsen verantwortlich sind. Eine präzise Steuerung des Antriebssystems ist für eine präzise Bearbeitung unerlässlich.
- Kühlmittelsystem: Kühlung ist dabei unerlässlich Mehrachsige CNC-Bearbeitung um eine Überhitzung von Werkzeugen und Werkstücken zu verhindern. CNC-Maschinen verfügen häufig über ein Kühlmittelsystem, um die optimale Temperatur aufrechtzuerhalten.
- Steuerrechner: Der Steuerrechner beherbergt die für den Betrieb der CNC-Maschine erforderliche Hardware und Software. Es interpretiert die von CAD/CAM-Software generierten G-Codes und M-Codes und wandelt sie in Bewegungen und Aktionen um.
Kapitel 2: Vorbereitung vor der Installation
Bevor Sie mit der Installation Ihrer CNC-Maschine beginnen, ist es wichtig, gründliche Vorbereitungen zu treffen. Dieses Kapitel führt Sie durch die wesentlichen Überlegungen vor der Installation, einschließlich der Einrichtung des Arbeitsplatzes, der Strom- und Elektroanforderungen sowie Sicherheitsmaßnahmen, um einen reibungslosen und sicheren Installationsprozess zu gewährleisten.A. Überlegungen zum Arbeitsplatz
- Platzanforderungen: Beginnen Sie mit der Beurteilung des verfügbaren Platzes in Ihrer Werkstatt oder Einrichtung. Stellen Sie sicher, dass der Bereich groß genug für die Unterbringung Ihrer CNC-Maschine ist und ausreichend Platz für sicheren Zugang und Wartung bietet. Berücksichtigen Sie die Abmessungen der Maschine, den Platzbedarf für die Materialhandhabung und etwaige zusätzliche Geräte oder Arbeitsplätze.
- Lüftung: Eine ausreichende Belüftung ist entscheidend, um die bei der Bearbeitung entstehende Wärme abzuleiten und potenziell schädliche Dämpfe oder Staubpartikel zu entfernen. Installieren Sie bei Bedarf geeignete Belüftungssysteme oder Luftfiltergeräte, um eine saubere und sichere Arbeitsumgebung zu gewährleisten.
- Bodenbelag: Stellen Sie sicher, dass der Bodenbelag im vorgesehenen Bereich eben und stabil ist und das Gewicht der CNC-Maschine tragen kann. Unebene oder schwache Bodenbeläge können zu Maschinenvibrationen und Ungenauigkeiten im Betrieb führen.
- Einfache Anwendung: Planen Sie einen einfachen Zugang zur CNC-Maschine für Installation, Wartung und Reparatur ein. Stellen Sie sicher, dass freie Wege und ausreichend Platz zum Manövrieren schwerer Maschinen und Materialien vorhanden sind.
- Beleuchtung: Für einen sicheren und präzisen Betrieb ist eine ausreichende Beleuchtung unerlässlich. Stellen Sie sicher, dass der Arbeitsbereich gut beleuchtet ist, um Unfälle zu vermeiden und eine klare Sicht auf den Bearbeitungsprozess zu gewährleisten.
B. Strom- und elektrische Anforderungen
- Stromversorgung: Ermitteln Sie die spezifischen elektrischen Anforderungen Ihrer CNC-Maschine. Überprüfen Sie die technischen Spezifikationen der Maschine und wenden Sie sich an den Hersteller oder Lieferanten, um sicherzustellen, dass die Stromversorgung Ihrer Einrichtung diese Anforderungen erfüllt.
- Spannung und Phase: CNC-Maschinen erfordern möglicherweise unterschiedliche Spannungsniveaus (z. B. 110 V, 220 V, 440 V) und Phasen (einphasig oder dreiphasig). Stellen Sie sicher, dass die Stromversorgung den Spezifikationen der Maschine entspricht.
- Schalttafel: Installieren Sie eine spezielle Schalttafel für die CNC-Maschine, um eine Überlastung vorhandener Schaltkreise zu verhindern. Beauftragen Sie einen zugelassenen Elektriker mit der professionellen Verkabelung und den Anschlüssen.
- Überspannungsschutz: Investieren Sie in Überspannungsschutzgeräte, um die empfindlichen elektronischen Komponenten der CNC-Maschine vor Spannungsschwankungen und Überspannungen zu schützen.
- Erdung: Stellen Sie sicher, dass sowohl die CNC-Maschine als auch das elektrische System ordnungsgemäß geerdet sind, um das Risiko elektrischer Gefahren und Geräteschäden zu verringern.
C. Sicherheitsmaßnahmen
- Sicherheitsausrüstung: Geben Sie der Sicherheit Vorrang, indem Sie Bedienern und Technikern geeignete persönliche Schutzausrüstung (PSA) zur Verfügung stellen. Dazu können Schutzbrillen, Gehörschutz, Handschuhe und Schutzkleidung gehören.
- Notfallmaßnahmen: Entwickeln und dokumentieren Sie Notabschaltverfahren, die die CNC-Maschine bei unvorhergesehenen Ereignissen oder Unfällen schnell stoppen können. Stellen Sie sicher, dass das gesamte Personal in diesen Verfahren geschult ist.
- Brandschutz: Installieren Sie Feuerlöscher und Rauchmelder in der Nähe der CNC-Maschine. Implementieren Sie Brandschutzprotokolle, indem Sie beispielsweise brennbare Materialien von der Maschine fernhalten und einen Notausgangsplan einhalten.
- Lockout/Tagout (LOTO): Implementieren Sie LOTO-Verfahren, um einen versehentlichen Maschinenstart während der Wartung oder Reparatur zu verhindern. Verwenden Sie Schlösser und Schilder, um anzuzeigen, wann eine Maschine gewartet wird.
- Sicherheitstraining: Führen Sie umfassende Sicherheitsschulungen für alle Mitarbeiter durch, die die CNC-Maschine bedienen, warten oder in deren Nähe arbeiten. Betonen Sie sichere Praktiken und die Wichtigkeit der Einhaltung von Sicherheitsprotokollen.
- Erste Hilfe: Halten Sie einen gut gefüllten Erste-Hilfe-Kasten in der Nähe der CNC-Maschine bereit. Stellen Sie sicher, dass geschultes Personal zur Verfügung steht, um bei Verletzungen sofort Erste Hilfe leisten zu können.
Kapitel 3: Zusammenbau der CNC-Maschine
Sobald Sie die Vorbereitungen vor der Installation abgeschlossen haben, ist es Zeit, mit der Montagephase fortzufahren. In diesem Kapitel stellen wir Ihnen eine Schritt-für-Schritt-Anleitung zum Zusammenbau Ihrer CNC-Maschine vor und decken dabei wichtige Aufgaben vom Auspacken und Überprüfen bis hin zum Kabelmanagement ab.A. Auspacken und Inspektion
- Unboxing: Beginnen Sie mit dem sorgfältigen Auspacken aller Komponenten Ihrer CNC-Maschine. Befolgen Sie beim Auspacken die Anweisungen des Herstellers, um Schäden während des Vorgangs zu vermeiden. Verwenden Sie bei Bedarf geeignete Werkzeuge und Hebezeuge.
- Komponentenbestand: Erstellen Sie eine Inventarcheckliste, um sicherzustellen, dass Sie alle im Handbuch oder in der Dokumentation der Maschine aufgeführten Komponenten erhalten haben. Stellen Sie sicher, dass nichts fehlt oder beschädigt ist.
- Auf Schäden prüfen: Untersuchen Sie jede Komponente gründlich auf Anzeichen von Beschädigungen wie Dellen, Kratzer oder verbogene Teile. Dokumentieren Sie etwaige Probleme und benachrichtigen Sie umgehend den Hersteller oder Lieferanten.
B. Komponenten organisieren
- Arbeitsbereich organisieren: Stellen Sie vor der Montage sicher, dass Ihr Arbeitsplatz sauber und gut organisiert ist. Beseitigen Sie Unordnung und bieten Sie ausreichend Platz zum Anordnen und Organisieren von Komponenten.
- Ähnliche Teile gruppieren: Gruppieren Sie ähnliche Teile, um den Montageprozess zu erleichtern. Komponenten wie z VerschlussTeile, Halterungen und Hardware sollten für einen einfachen Zugriff in separaten Behältern oder Tabletts untergebracht werden.
- Siehe Handbücher: Lesen Sie die vom Hersteller bereitgestellten Montagehandbücher und Dokumentationen. Machen Sie sich mit den Montageschritten, Diagrammen und etwaigen spezifischen Anweisungen vertraut.
C. Zusammenbau des Maschinenrahmens
- Basisbaugruppe: Beginnen Sie mit der Basis der CNC-Maschine. Befolgen Sie die Anweisungen des Herstellers, um das Grundgestell sicher zu montieren. Stellen Sie sicher, dass es eben und stabil ist.
- Säulen- und Stützstrukturen: Montieren Sie die Säulen und Stützstrukturen und richten Sie sie genau auf die Basis aus. Ziehen Sie alle Schrauben und Befestigungselemente mit den empfohlenen Drehmomentwerten an.
- Führungen und Schienen: Installieren Sie die Führungsbahnen und Schienen, die die Bewegung der Schneid- oder Werkzeughaltekomponenten der Maschine führen. Stellen Sie sicher, dass sie richtig ausgerichtet und sicher befestigt sind.
D. Anbringen von Motoren und Antrieben
- Motorinstallation: Montieren Sie die Motoren an den vorgesehenen Positionen gemäß den Anweisungen des Herstellers. Stellen Sie sicher, dass die Motoren sicher befestigt und auf die Antriebsmechanismen ausgerichtet sind.
- Fahrsystem: Verbinden Sie die Motoren über entsprechende Kupplungen oder Riemen mit den Antriebsmechanismen. Sorgen Sie für die richtige Spannung und Ausrichtung, um Spiel und Ungenauigkeiten zu vermeiden.
e. Installieren des Control Panels
- Schalttafelmontage: Installieren Sie das Bedienfeld an einem geeigneten Ort, normalerweise in Reichweite des Bedieners. Stellen Sie sicher, dass es sicher montiert und positioniert ist, um optimale Sicht und Zugänglichkeit zu gewährleisten.
- Elektrische Anschlüsse: Schließen Sie das Bedienfeld gemäß den Schaltplänen in der Herstellerdokumentation an das elektrische System der Maschine an. Überprüfen Sie alle Verbindungen noch einmal auf Richtigkeit.
F. Kabelmanagement
- Kabelführung: Verlegen Sie alle Kabel, Drähte und Schläuche sorgfältig und geordnet, um ein Verheddern oder eine Behinderung beweglicher Teile zu vermeiden. Verwenden Sie Kabelrinnen oder Clips, um Kabel zu sichern und zu schützen.
- Beschriftung: Beschriften Sie Kabel und Leitungen mit Kennzeichnungen oder Schildern, um die Fehlerbehebung und Wartung zu vereinfachen. Markieren Sie deutlich den Zweck und das Ziel jedes Kabels.
- Testing: Führen Sie vor dem Schließen von Gehäusen oder Schalttafeln einen Vortest durch, um sicherzustellen, dass alle elektrischen Anschlüsse ordnungsgemäß funktionieren. Stellen Sie sicher, dass Motoren und Sensoren wie erwartet reagieren.
Kapitel 4: Ausrichten und Nivellieren
In Kapitel 4 befassen wir uns mit dem entscheidenden Prozess der Ausrichtung und Nivellierung Ihrer CNC-Maschine. Die richtige Ausrichtung und Nivellierung ist von grundlegender Bedeutung für die Gewährleistung der Genauigkeit und Präzision des Maschinenbetriebs. Dieses Kapitel behandelt die Bedeutung der Ausrichtung und Nivellierung, die benötigten Werkzeuge und Geräte sowie eine Schritt-für-Schritt-Anleitung für den Ausrichtungs- und Nivellierungsprozess.A. Bedeutung der Ausrichtung und Nivellierung
- Genauigkeit und Präzision: Ausrichtung und Nivellierung sind unerlässlich, um das hohe Maß an Genauigkeit und Präzision zu erreichen, das bei der CNC-Bearbeitung erforderlich ist. Fluchtungsfehler oder Unebenheiten können zu Maßfehlern bei den fertigen Werkstücken führen.
- Reduzierter Verschleiß: Die richtige Ausrichtung reduziert unnötige Belastungen von Maschinenkomponenten, wie z Lagers und Führungen. Dies verlängert die Lebensdauer der Maschine und reduziert die Wartungskosten.
- Minimierte Vibration: Eine gut ausgerichtete und nivellierte Maschine erzeugt weniger Vibrationen, was zu besseren Oberflächengüten und geringerem Werkzeugverschleiß führt. Auch Vibrationen können die Lebensdauer empfindlicher elektronischer Bauteile beeinträchtigen.
- Sicherheit: Falsch ausgerichtete oder unebene Maschinen können ein Sicherheitsrisiko darstellen. Beispielsweise kann eine nicht waagerechte Maschine während des Betriebs umkippen oder sich unerwartet bewegen.
B. Benötigte Werkzeuge und Ausrüstung
Für die korrekte Ausrichtung und Nivellierung benötigen Sie folgende Werkzeuge und Geräte:- Präzisionsstufen: Hochwertige Präzisionswasserwaagen sind entscheidend für die genaue Messung der Ausrichtung und Nivellierung der Maschine.
- Einstellwerkzeuge: Abhängig vom Design Ihrer Maschine benötigen Sie möglicherweise spezielle Werkzeuge wie Schraubenschlüssel, Unterlegscheiben oder Einstellschrauben.
- Messuhren: Messuhren helfen bei der Messung der Ausrichtung verschiedener Maschinenkomponenten, einschließlich der Werkzeugspindel und des Arbeitstisches.
- Fühlerlehren: Fühlerlehren dienen zur Messung von Spalten und Spielräumen zwischen Maschinenkomponenten beim Ausrichten.
- Ausrichtungslaser: Zur Beurteilung der Geradheit von Führungsbahnen und anderen linearen Bauteilen kann ein Ausrichtlaser hilfreich sein.
C. Schrittweiser Ausrichtungs- und Nivellierungsprozess
Befolgen Sie diese Schritte, um Ihre CNC-Maschine auszurichten und zu nivellieren:Schritt 1: Bereiten Sie den Arbeitsbereich vor
Stellen Sie sicher, dass der Arbeitsbereich sauber, frei von Schmutz und gut beleuchtet ist. Beseitigen Sie alle Hindernisse, die den Ausrichtungs- und Nivellierungsvorgang behindern könnten.Schritt 2: Festlegung des Referenzpunkts
Wählen Sie einen stabilen Referenzpunkt am Maschinenrahmen oder -sockel, der normalerweise vom Hersteller bereitgestellt wird. Dieser Punkt dient als Startreferenz für alle Messungen.Schritt 3: Nivellieren Sie die Maschine
- Platzieren Sie Präzisionswasserwaagen auf verschiedenen Oberflächen der Maschine, z. B. auf dem Sockel, den Säulen und dem Arbeitstisch.
- Passen Sie die Nivellierschrauben oder Unterlegscheiben nach Bedarf an, um eine perfekte horizontale Ausrichtung zu erreichen. Überprüfen Sie die Präzision der Blasenanzeigen an den Wasserwaagen.
Schritt 4: Ausrichtung der Führungsschienen und Schlitten
- Verwenden Sie Messuhren und Ausrichtungslaser, um die Geradheit und Parallelität von Führungen, Schlitten und anderen linearen Komponenten zu überprüfen.
- Passen Sie die entsprechenden Komponenten an, um festgestellte Fehlausrichtungen zu korrigieren.
Schritt 5: Spindelausrichtung
- Montieren Sie eine Messuhr an der Spindel oder dem Werkzeughalter der Maschine.
- Drehen Sie die Spindel, um den Rundlauf und die Konzentrizität zu prüfen. Passen Sie die Spindel nach Bedarf an, um Unrundheit zu minimieren.
Schritt 6: Ausrichtung des Arbeitstisches
- Überprüfen Sie die Ausrichtung des Arbeitstisches oder der Werkstückhaltevorrichtung mithilfe von Messuhren.
- Passen Sie die Positionierung des Arbeitstisches an, um sicherzustellen, dass er senkrecht zu den Achsen der Maschine steht.
- Überprüfen Sie nach den Anpassungen erneut alle Ausrichtungen, um sicherzustellen, dass sie den angegebenen Toleranzen entsprechen.
- Führen Sie Testläufe durch, um sicherzustellen, dass die Maschine genau funktioniert und die gewünschten Ergebnisse liefert.
Schritt 8: Dokumentation
Führen Sie detaillierte Aufzeichnungen über den Ausrichtungs- und Nivellierungsprozess, einschließlich Messungen, vorgenommener Anpassungen und aufgetretener Probleme. Diese Dokumentation wird für zukünftige Referenz- und Wartungszwecke von großem Nutzen sein.Schritt 9: Endkontrolle und Zertifizierung
Erwägen Sie, eine Endkontrolle und Zertifizierung von einem qualifizierten Techniker oder Ingenieur durchführen zu lassen, um sicherzustellen, dass die CNC-Maschine den Industriestandards und Sicherheitsanforderungen entspricht. Die richtige Ausrichtung und Nivellierung ist für den zuverlässigen und genauen Betrieb Ihrer CNC-Maschine unerlässlich. Nehmen Sie sich bei diesem Vorgang Zeit, denn Präzision ist oberstes Gebot. Wenn Sie diese Schritte befolgen und die richtigen Werkzeuge verwenden, können Sie sicherstellen, dass sich Ihre Maschine in einem optimalen Zustand für erfolgreiche Bearbeitungsvorgänge befindet. Im nächsten Kapitel werden wir die Anforderungen an die elektrische Verkabelung Ihrer CNC-Maschine untersuchen.Kapitel 5: Elektrische Verkabelung
In diesem Kapitel befassen wir uns mit den Aspekten der elektrischen Verkabelung Ihrer CNC-Maschineninstallation. Eine ordnungsgemäße elektrische Verkabelung ist für den sicheren und effizienten Betrieb der Maschine von entscheidender Bedeutung. In diesem Kapitel geht es um das Verständnis elektrischer Systeme, die Verkabelung der CNC-Maschine und wichtige Sicherheitsvorkehrungen.A. Elektrische Systeme verstehen
- Energieversorgung: CNC-Maschinen benötigen eine stabile und angemessene Stromversorgung. Machen Sie sich mit den vom Maschinenhersteller angegebenen Spannungs-, Frequenz- und Phasenanforderungen vertraut. Stellen Sie sicher, dass die Stromversorgung zuverlässig ist und über eine ausreichende Kapazität zur Bewältigung der elektrischen Last der Maschine verfügt.
- Schalttafel: Die meisten CNC-Maschinen verfügen über eine Schalttafel, in der verschiedene Komponenten untergebracht sind, darunter Leistungsschalter, Relais, Schütze und Klemmenblöcke. Machen Sie sich mit den Komponenten im Panel und ihren Funktionen vertraut.
- Schaltplan: Überprüfen Sie die vom Maschinenhersteller bereitgestellten Schaltpläne. Diese Diagramme veranschaulichen die Verbindungen zwischen Komponenten und sind für die korrekte Verkabelung unerlässlich.
- Erdung: Eine ordnungsgemäße Erdung ist für die Sicherheit von entscheidender Bedeutung. Stellen Sie sicher, dass die Maschine und das elektrische System gemäß den örtlichen Elektrovorschriften und den Empfehlungen des Herstellers geerdet sind.
B. Verkabelung der CNC-Maschine
Befolgen Sie diese Schritte, um Ihre CNC-Maschine zu verkabeln:Schritt 1: Ausschalten
Stellen Sie sicher, dass die Maschine und die Stromquelle ausgeschaltet sind, bevor Sie mit den Verkabelungsarbeiten beginnen. Trennen Sie die Maschine von der Stromquelle.Schritt 2: Verkabelungsplan
Erstellen Sie einen Verdrahtungsplan basierend auf den Verdrahtungsplänen des Herstellers. Identifizieren Sie die Komponenten wie Motoren, Sensoren, Schalter und das Bedienfeld und bestimmen Sie deren Verbindungen.Schritt 3: Kabelauswahl
Verwenden Sie geeignete Kabel und Leitungen, die den Spannungs- und Stromanforderungen der Maschine entsprechen. Stellen Sie sicher, dass die Kabel den richtigen Durchmesser und die richtige Isolationsart haben.Schritt 4: Kabelführung
Verlegen Sie die Kabel und Leitungen sorgfältig entlang der Kabelkanäle oder Leitungen der Maschine. Halten Sie sie organisiert und getrennt von beweglichen Komponenten, um Schäden zu vermeiden.Schritt 5: Terminalverbindungen
Verbinden Sie die Drähte mit den entsprechenden Anschlüssen an Komponenten wie Motoren, Sensoren und Schaltern. Stellen Sie bei Bedarf sichere Verbindungen durch Crimpen oder Löten sicher. Verwenden Sie Kabeletiketten zur einfachen Identifizierung.Schritt 6: Verkabelung des Bedienfelds
Schließen Sie die Drähte im Bedienfeld an die entsprechenden Klemmenblöcke, Leistungsschalter, Schütze und Relais an, wie in den Schaltplänen angegeben. Seien Sie bei Ihrer Arbeit sorgfältig, um Querverbindungen oder lose Drähte zu vermeiden.Schritt 7: Stromversorgungsanschluss
Schließen Sie die Maschine gemäß den Richtlinien des Herstellers an die Stromversorgung an. Überprüfen Sie die Spannungs-, Phasen- und Frequenzeinstellungen noch einmal, um sicherzustellen, dass sie den Anforderungen der Maschine entsprechen.Schritt 8: Sicherheitsmaßnahmen
Implementieren Sie bei Bedarf Sicherheitsfunktionen wie Not-Aus-Schalter und Sicherheitsverriegelungen. Stellen Sie sicher, dass diese Sicherheitseinrichtungen korrekt verdrahtet und auf Funktionalität geprüft sind.Schritt 9: Testen
Bevor Sie das Bedienfeld schließen und die Maschine einschalten, führen Sie einen Durchgangstest durch, um zu prüfen, ob Verkabelungsfehler oder Kurzschlüsse vorliegen. Stellen Sie sicher, dass alle Verbindungen sicher und frei von losen Litzen sind.C. Sicherheitsvorkehrungen
- Lockout/Tagout (LOTO): Implementieren Sie LOTO-Verfahren, um ein versehentliches Anlaufen der Maschine während der Verkabelung oder Wartungsarbeiten zu verhindern. Zur Isolierung von Stromquellen sollten Sperrvorrichtungen verwendet werden.
- Qualifizierter Elektriker: Elektrische Arbeiten sollten von einem qualifizierten Elektriker oder Techniker durchgeführt werden, der mit den elektrischen Anforderungen der Maschine und den örtlichen Elektrovorschriften vertraut ist.
- Überspannungschutz: Installieren Sie geeignete Überlastschutzeinrichtungen, wie z. B. Schutzschalter oder Sicherungen, um Schäden bei elektrischen Störungen zu verhindern.
- Erdung: Stellen Sie sicher, dass die Maschine und alle elektrischen Komponenten ordnungsgemäß geerdet sind, um elektrische Gefahren zu vermeiden.
- Beschriftung: Beschriften Sie alle Drähte, Kabel und Komponenten deutlich, um die Fehlerbehebung und zukünftige Wartung zu erleichtern.
- Regelmäßige Inspektionen: Überprüfen Sie das elektrische System regelmäßig auf Anzeichen von Verschleiß, Beschädigung oder lockeren Anschlüssen. Beheben Sie alle Probleme umgehend.
- Notfallmaßnahmen: Legen Sie Notfallmaßnahmen für elektrische Probleme, einschließlich elektrischer Brände oder Stromschläge, fest und kommunizieren Sie diese.
Kapitel 6: Installation der Steuerungssoftware
In diesem Kapitel untersuchen wir den Installationsprozess der Steuerungssoftware für Ihre CNC-Maschine. Die Steuerungssoftware ist das Gehirn Ihres CNC-Systems und für die Interpretation und Ausführung der Bearbeitungsanweisungen verantwortlich. Dieses Kapitel bietet einen Überblick über CNC-Maschinensteuerungssoftware, eine Schritt-für-Schritt-Anleitung für die Softwareinstallation sowie die Kalibrierungs- und Testverfahren.A. Übersicht über die CNC-Maschinensteuerungssoftware
- Rolle der Steuerungssoftware: Die CNC-Maschinensteuerungssoftware ist für die Umsetzung der Konstruktions- und Werkzeugwegdaten aus der CAD/CAM-Software in spezifische Maschinenbewegungen verantwortlich. Es generiert die G-Codes und M-Codes, die die Motoren und Aktoren der Maschine steuern.
- Arten von Steuerungssoftware: Es gibt verschiedene Arten von CNC-Steuerungssoftware, von proprietärer Software von Maschinenherstellern bis hin zu Open-Source-Lösungen und Lösungen von Drittanbietern. Wählen Sie eine Software, die den Anforderungen Ihrer Maschine und Ihrer Vertrautheit mit der Benutzeroberfläche entspricht.
- Merkmale: Steuerungssoftware kann in Bezug auf Funktionen und Fähigkeiten variieren. Suchen Sie nach Software, die die notwendigen Funktionen für Ihre spezifischen Bearbeitungsanforderungen bietet, wie z. B. Werkzeugweggenerierung, Werkzeugwechsel und Spindeldrehzahlsteuerung.
B. Schritt-für-Schritt-Softwareinstallation
Befolgen Sie diese Schritte, um die Steuerungssoftware für Ihre CNC-Maschine zu installieren:Schritt 1: Systemanforderungen
Überprüfen Sie die vom Hersteller der Steuerungssoftware angegebenen Systemanforderungen. Stellen Sie sicher, dass Ihr Computer diese Anforderungen hinsichtlich Hardware, Betriebssystem und verfügbarem Speicher erfüllt.Schritt 2: Software-Download oder Installationsmedium
Besorgen Sie sich die Steuerungssoftware, indem Sie sie entweder von der Website des Herstellers herunterladen oder die vom Hersteller bereitgestellten Installationsmedien verwenden.Schritt 3: Installation
- Doppelklicken Sie auf die Softwareinstallationsdatei, um den Installationsvorgang zu starten.
- Befolgen Sie die Anweisungen auf dem Bildschirm des Installationsprogramms. Dazu kann das Auswählen von Installationsverzeichnissen, das Akzeptieren von Lizenzvereinbarungen und das Konfigurieren von Softwareeinstellungen gehören.
- Stellen Sie sicher, dass die Installation erfolgreich ist und keine Fehler auftreten.
Schritt 4: Lizenzierung und Aktivierung
Wenn für die Steuerungssoftware eine Lizenzierung oder Aktivierung erforderlich ist, befolgen Sie die Richtlinien des Herstellers, um diesen Vorgang abzuschließen. Stellen Sie sicher, dass Sie über die erforderlichen Lizenzschlüssel oder Aktivierungscodes verfügen.Schritt 5: Maschinenkonfiguration
Konfigurieren Sie die Steuerungssoftware passend zu den Spezifikationen Ihrer CNC-Maschine. Dies kann das Einstellen von Parametern für die Achsen, Motortypen und andere Hardwarekomponenten der Maschine umfassen.Schritt 6: Werkzeug- und Materialdatenbank
Erstellen oder importieren Sie eine Werkzeug- und Materialdatenbank in die Steuerungssoftware. Diese Informationen sind für die Werkzeugweggenerierung und die Auswahl geeigneter Bearbeitungsparameter von entscheidender Bedeutung.C. Kalibrierung und Prüfung
Befolgen Sie nach der Installation der Steuerungssoftware die folgenden Schritte zur Kalibrierung und zum Testen:Schritt 1: Referenzpunkt- und Referenzpunkt-Einrichtung
- Bringen Sie die Maschine in die Ausgangsposition, indem Sie alle Achsen in ihre Referenz- oder Ausgangspositionen bewegen. Dadurch wird ein bekannter Ausgangspunkt für die Bewegungen der Maschine festgelegt.
- Stellen Sie sicher, dass die Maschine genau zur Referenzposition zurückkehrt.
Schritt 2: Werkzeugkalibrierung
- Kalibrieren Sie die Werkzeuglänge und den Werkzeugdurchmesser. Dadurch wird sichergestellt, dass die Maschine die genauen Abmessungen der zu verwendenden Werkzeuge kennt.
- Führen Sie Testschnitte oder Werkzeugabsetzroutinen durch, um die Werkzeugkalibrierung zu validieren.
Schritt 3: Werkstückeinrichtung
- Befestigen Sie ein Testwerkstück oder -material auf dem Arbeitstisch oder dem Werkstückhaltesystem der Maschine.
- Stellen Sie sicher, dass das Werkstück richtig ausgerichtet und befestigt ist.
Schritt 4: Testläufe
- Laden Sie ein einfaches Testprogramm in die Steuerungssoftware.
- Führen Sie das Testprogramm aus, um die Bewegungen und Bearbeitungsergebnisse der Maschine zu beobachten.
- Überprüfen Sie, ob Probleme wie unerwartete Bewegungen, Werkzeugkollisionen oder Ungenauigkeiten vorliegen.
Schritt 5: Feinabstimmung
Wenn beim Testen Probleme festgestellt werden, passen Sie die Einstellungen der Steuerungssoftware, die Werkzeugversätze oder die Werkstückeinrichtung nach Bedarf an. Wiederholen Sie die Testläufe, bis die Maschine präzise und zuverlässig arbeitet.Schritt 6: Dokumentation
Dokumentieren Sie alle Kalibrierungs- und Testergebnisse, einschließlich aller an der Steuerungssoftware vorgenommenen Anpassungen. Diese Dokumentation ist für zukünftige Referenzzwecke und zur Fehlerbehebung hilfreich. Die Installation der Steuerungssoftware ist ein entscheidender Schritt bei der Einrichtung einer CNC-Maschine. Indem Sie die Anweisungen des Herstellers befolgen, die Maschine kalibrieren und gründliche Tests durchführen, können Sie sicherstellen, dass Ihre CNC-Maschine produktionsbereit ist und präzise und genaue Ergebnisse liefern kann. Im nächsten Kapitel werden wir die Bedeutung von Schmierung und Wartung für die Aufrechterhaltung der Leistung und Langlebigkeit Ihrer CNC-Maschine untersuchen.Kapitel 7: Schmierung und Wartung
In diesem Kapitel konzentrieren wir uns auf die kritischen Aspekte der Schmierung und Wartung Ihrer CNC-Maschine. Eine ordnungsgemäße Schmierung und regelmäßige Wartung sind für die Gewährleistung der Langlebigkeit, Genauigkeit und Zuverlässigkeit Ihrer CNC-Ausrüstung unerlässlich. Wir besprechen die Bedeutung von Schmierung, Schmierstellen und der Erstellung eines Wartungsplans.A. Warum Schmierung wichtig ist
Die Schmierung spielt aus mehreren Gründen eine entscheidende Rolle für die Leistung und Langlebigkeit Ihrer CNC-Maschine:- Reibungsreduzierung: Durch die Schmierung wird die Reibung zwischen beweglichen Teilen wie Lagern, Führungen und Kugelumlaufspindeln verringert. Dies minimiert den Verschleiß der Komponenten und verlängert deren Lebensdauer.
- Wärmeableitung: Schmierstoffe leiten die bei der Bearbeitung entstehende Wärme ab und verhindern so eine Überhitzung kritischer Komponenten. Dadurch bleibt die Maßhaltigkeit erhalten und das Risiko einer Wärmeausdehnung wird verringert.
- Reibungslosen Betrieb: Die richtige Schmierung sorgt für sanftere und präzisere Bewegungen der Maschinenkomponenten. Dies ist unerlässlich, um die hohe Präzision zu erreichen, die bei der CNC-Bearbeitung erforderlich ist.
- Korrosion verhindern: Schmierstoffe bilden eine Schutzbarriere gegen Feuchtigkeit und Verunreinigungen und verringern so das Korrosionsrisiko auf Metalloberflächen.
- Rauschunterdrückung: Durch die Schmierung kann der beim Maschinenbetrieb entstehende Lärm reduziert und so eine ruhigere und komfortablere Arbeitsumgebung geschaffen werden.
B. Schmierstellen
Verschiedene CNC-Maschinen verfügen über unterschiedliche Schmierstellen, die Aufmerksamkeit erfordern. Hier sind einige häufige Schmierpunkte, die Sie berücksichtigen sollten:- Linearführungen: Tragen Sie Schmiermittel auf die Linearführungen auf, die die Bewegung der Maschinenachsen erleichtern. Dazu können Kugelumlaufspindeln, Linearlager und Gleitführungen gehören.
- Spindellager: Schmieren Sie die Spindellager, um eine reibungslose Drehung zu gewährleisten und die Reibung bei Schneid- oder Bearbeitungsvorgängen zu verringern.
- Werkzeugwechslermechanismus: Wenn Ihre Maschine über einen automatischen Werkzeugwechsler verfügt, stellen Sie sicher, dass die beweglichen Teile des Mechanismus ausreichend geschmiert sind, um Blockaden oder Fehlfunktionen zu vermeiden.
- Getriebe: Getriebe, sofern in Ihrer Maschine vorhanden, müssen möglicherweise in bestimmten Abständen geschmiert werden, um die Effizienz aufrechtzuerhalten und den Verschleiß zu reduzieren.
- Kugelgewindetriebe: Kugelumlaufspindeln sind entscheidende Komponenten in CNC-Maschinen. Die ordnungsgemäße Schmierung von Kugelumlaufspindeln und den dazugehörigen Komponenten ist für eine genaue Positionierung und Bewegung unerlässlich.
- Kühlmittelpumpe: Wenn Ihre Maschine ein Kühlmittelsystem verwendet, stellen Sie sicher, dass die Pumpe ordnungsgemäß geschmiert ist und dass das Kühlmittel sauber und frei von Verunreinigungen ist.
- Achsmotoren: Befolgen Sie je nach Art der für die Achsenbewegung verwendeten Motoren (z. B. Schrittmotor oder Servomotor) die Empfehlungen des Herstellers zur Schmierung oder Wartung.
- Dichtungen und Dichtungen: Überprüfen Sie verschlissene oder beschädigte Dichtungen und ersetzen Sie diese bei Bedarf, um Schmiermittellecks und Verunreinigungen zu verhindern.
C. Wartungsplan
Um Ihre CNC-Maschine in optimalem Zustand zu halten, ist die Erstellung eines regelmäßigen Wartungsplans unerlässlich. Hier sind die Schritte zum Erstellen eines Wartungsplans:Schritt 1: Herstellerrichtlinien
Informationen zu Wartungsintervallen, Schmierungsarten und spezifischen Verfahren finden Sie in der Dokumentation und den Empfehlungen des Herstellers.Schritt 2: Tägliche Wartung
Implementieren Sie tägliche Wartungsroutinen, die Aufgaben wie das Entfernen von Schmutz, die Überprüfung auf lockere Befestigungselemente und die Überprüfung des Kühlmittelstands umfassen. Diese Aufgaben tragen dazu bei, eine Eskalation kleinerer Probleme zu verhindern.Schritt 3: Wöchentliche oder monatliche Wartung
Planen Sie umfangreichere Wartungsaufgaben wöchentlich oder monatlich ein, abhängig von der Nutzung Ihrer Maschine. Dies kann eine gründliche Reinigung, Schmierung und Inspektion kritischer Komponenten umfassen.Schritt 4: Vierteljährliche oder halbjährliche Wartung
Führen Sie umfangreichere Wartungsaufgaben durch, z. B. die Überprüfung und Einstellung der Ausrichtung, die Prüfung elektrischer Verbindungen und den Austausch verschlissener oder beschädigter Teile.Schritt 5: Jährliche Wartung
Erwägen Sie einmal jährlich eine umfassende Inspektion durch einen qualifizierten Techniker oder Ingenieur. Dies sollte einen vollständigen Schmierzyklus, Kalibrierungsprüfungen und alle notwendigen Reparaturen oder Ersetzungen umfassen.Schritt 6: Dokumentation
Führen Sie detaillierte Aufzeichnungen aller Wartungsaktivitäten, einschließlich Daten, durchgeführter Aufgaben und festgestellter Probleme. Diese Dokumentation ist von unschätzbarem Wert für die Verfolgung der Maschinenhistorie und die Planung zukünftiger Wartungsarbeiten.Schritt 7: Training
Stellen Sie sicher, dass das für die Wartung verantwortliche Personal ausreichend geschult ist und Zugang zu den erforderlichen Werkzeugen und Ressourcen hat. Regelmäßige Schmierung und Wartung sind für die Maximierung der Lebensdauer und Leistung Ihrer CNC-Maschine unerlässlich. Indem Sie einen gut etablierten Wartungsplan einhalten und sich mit den Schmierstellen befassen, können Sie vorzeitigem Verschleiß vorbeugen und sicherstellen, dass Ihre Maschine weiterhin präzise und qualitativ hochwertige Werkstücke produziert. Im nächsten Kapitel besprechen wir Sicherheitsverfahren und Richtlinien für den Betrieb Ihrer CNC-Maschine.Kapitel 8: Sicherheitsverfahren für CNC-Maschinen
Sicherheit ist bei der Arbeit mit CNC-Maschinen von größter Bedeutung. In diesem Kapitel befassen wir uns mit den wichtigsten Sicherheitsverfahren und -richtlinien für den Betrieb von CNC-Maschinen, einschließlich der Sicherheit von CNC-Maschinen, Notabschaltverfahren und der Verwendung persönlicher Schutzausrüstung (PSA).A. CNC-Maschinensicherheit
- Ausbildung: Stellen Sie sicher, dass das gesamte Personal, das CNC-Maschinen bedient oder in deren Nähe arbeitet, eine umfassende Sicherheitsschulung erhalten hat. Dies sollte maschinenspezifische Schulungen, sichere Betriebsabläufe und Gefahrenerkennung umfassen.
- Maschinenschutz: Sorgen Sie dafür, dass alle Maschinenschutzvorrichtungen und Sicherheitsverriegelungen vorhanden sind und ordnungsgemäß funktionieren. Diese Sicherheitsfunktionen sollen den Bediener vor beweglichen Teilen und möglichen Gefahren schützen.
- Sicherheitsetiketten: Stellen Sie sicher, dass Sicherheitsaufkleber und Warnschilder gut sichtbar an der Maschine angebracht sind. Diese Etiketten geben wichtige Informationen über mögliche Gefahren und Sicherheitsvorkehrungen.
- Not-Halt: Machen Sie die Bediener mit der Position und Verwendung des Not-Aus-Schalters vertraut. Stellen Sie sicher, dass es im Notfall leicht zugänglich ist.
- Arbeitsbereich löschen: Sorgen Sie für einen aufgeräumten Arbeitsplatz rund um die CNC-Maschine. Entfernen Sie alle unnötigen Werkzeuge, Materialien oder Fremdkörper, die eine Stolpergefahr darstellen oder den Maschinenbetrieb beeinträchtigen könnten.
- Maschinensperre/Tagout (LOTO): Implementieren Sie Sperr-/Kennzeichnungsverfahren, um die Maschine stromlos zu machen und zu sichern, bevor Sie Wartungs- oder Reparaturarbeiten durchführen. Sperrvorrichtungen verhindern ein versehentliches Anlaufen der Maschine.
- Spindel- und Werkzeugsicherheit: Gehen Sie vorsichtig mit Schneidwerkzeugen und Werkzeugwechseln um. Stellen Sie sicher, dass die Werkzeuge ordnungsgemäß in den Werkzeughaltern befestigt sind und dass der Werkzeugwechsel nach sicheren Verfahren durchgeführt wird.
- Materialhandhabung: Verwenden Sie beim Umgang mit schweren Materialien oder Werkstücken geeignete Hebegeräte und -techniken. Vermeiden Sie eine Überlastung der Gewichtskapazität der Maschine.
- Brandschutz: Halten Sie Feuerlöscher und Rauchmelder in der Nähe. Entwickeln und kommunizieren Sie Brandschutzprotokolle, einschließlich der Lage von Notausgängen und Evakuierungsverfahren.
B. Verfahren zur Notabschaltung
- Notaus-Knopf: Im Notfall oder wenn eine sofortige Abschaltung erforderlich ist, drücken Sie die Not-Aus-Taste. Diese Schaltfläche ist normalerweise groß, rot und leicht zugänglich.
- Stoppen Sie alle Bewegungen: Der Not-Aus-Knopf sollte alle Maschinenbewegungen anhalten und die Stromversorgung der Maschine unterbrechen. Stellen Sie sicher, dass die Maschine vollständig zum Stillstand kommt.
- Lockout / Tagout: Befolgen Sie nach der Betätigung des Not-Aus-Schalters die Sperr-/Kennzeichnungsverfahren, um die Maschine zu sichern und versehentliche Neustarts zu verhindern.
- Benachrichtigen Sie die Behörden: Wenn ein Unfall oder eine gefährliche Situation auftritt, wenden Sie sich an die zuständigen Behörden, z. B. an Wartungspersonal oder Vorgesetzte, um das Problem zu beheben und sicherzustellen, dass die Maschine wieder sicher betrieben werden kann.
C. Persönliche Schutzausrüstung (PPE)
- Schutzbrille: Bediener und Personal in der Nähe der CNC-Maschine sollten Schutzbrillen mit angemessener Schlagfestigkeit tragen, um ihre Augen vor umherfliegenden Trümmern zu schützen.
- Gehörschutz: In lauten Werkstätten sollte ein Gehörschutz wie Ohrstöpsel oder Ohrenschützer getragen werden, um Gehörschäden vorzubeugen.
- Handschuhe: Tragen Sie beim Umgang mit Materialien oder bei Wartungsarbeiten geeignete Handschuhe. Stellen Sie sicher, dass Handschuhe in der Nähe von beweglichen Maschinenteilen keine Gefahr darstellen.
- Atemschutz: If Bearbeitungsmaterials Staub oder Dämpfe erzeugen, verwenden Sie Atemschutzgeräte wie Staubmasken oder Atemschutzgeräte, um sich vor Gefahren durch Einatmen zu schützen.
- Sicherheitsschuhe: Tragen Sie feste Sicherheitsschuhe oder Stiefel mit rutschfester Sohle, um Fußverletzungen vorzubeugen und eine gute Traktion am Arbeitsplatz zu gewährleisten.
- Schutzkleidung: Tragen Sie je nach Bearbeitungsverfahren und verwendeten Materialien entsprechende Schutzkleidung, wie z. B. Schürzen oder Ganzkörperoveralls.
- Sicherheitshelm: Tragen Sie in Umgebungen, in denen herabfallende Gegenstände ein Risiko darstellen, Schutzhelme oder Schutzhelme als Kopfschutz.
- Gesichtsschutz: Bei Arbeiten, die potenzielle Gefahren für das Gesicht mit sich bringen, z. B. verspritzendes Kühlmittel oder Späne, verwenden Sie zusätzlich zur Schutzbrille einen Gesichtsschutz.
Kapitel 9: Fehlerbehebung bei häufigen Installationsproblemen
In diesem Kapitel werden wir häufige Probleme untersuchen, die bei der Installation von CNC-Maschinen auftreten können, und Lösungen für diese Probleme bereitstellen. Darüber hinaus besprechen wir Fehlerbehebungstechniken, die Ihnen dabei helfen können, Probleme effektiv zu erkennen und zu lösen.A. Häufige Probleme und Lösungen
-
Elektrische Probleme:
- Problem: Die CNC-Maschine lässt sich nicht einschalten.
- Lösung: Überprüfen Sie die Stromquelle, die elektrischen Anschlüsse und die Sicherungen. Stellen Sie sicher, dass der Not-Aus-Knopf freigegeben ist.
-
Mechanische Fehlausrichtung:
- Problem: Die Maschine erzeugt ungenaue Schnitte oder Werkstückabmessungen.
- Lösung: Richten Sie die Maschine neu aus und nivellieren Sie sie. Auf lose Komponenten oder verschlissene Führungsbahnen prüfen und bei Bedarf ersetzen.
-
Werkzeugrattern oder Vibration:
- Problem: Die Maschine erzeugt Vibrationen oder Werkzeugrattern, die sich auf die Oberflächenbeschaffenheit auswirken.
- Lösung: Werkzeughalter und Spindelspannzange auf korrekten Sitz prüfen. Passen Sie Schnittparameter und Werkzeugwegeinstellungen an.
-
Kommunikationsfehler:
- Problem: Die CNC-Steuerung kann nicht mit dem Computer oder der CAD/CAM-Software kommunizieren.
- Lösung: Überprüfen Sie die Kabelverbindungen, Baudraten und Einstellungen sowohl am Gerät als auch am Computer. Stellen Sie sicher, dass die Software und Treiber ordnungsgemäß installiert sind.
-
Werkzeugbruch:
- Problem: Bei der Bearbeitung kommt es häufig zu Werkzeugbrüchen.
- Lösung: Überprüfen Sie die Werkzeugausrichtung, den Zustand des Werkzeughalters und den Spindelrundlauf. Passen Sie Vorschübe und Geschwindigkeiten je nach Werkzeugmaterial und Werkstück an.
-
Probleme mit Kühlmittel oder Schmierung:
- Problem: Unzureichender oder ungleichmäßiger Kühlmittel-/Schmiermittelfluss.
- Lösung: Überprüfen Sie die Komponenten des Kühl- und Schmiersystems wie Pumpen, Schläuche und Düsen. Reinigen oder ersetzen Sie die Filter und achten Sie auf den richtigen Flüssigkeitsstand.
-
Softwarefehler:
- Problem: Die Steuerungssoftware zeigt Fehlermeldungen oder unerwartetes Verhalten an.
- Lösung: Überprüfen Sie Fehlermeldungen und konsultieren Sie die Softwaredokumentation. Suchen Sie nach Kompatibilitätsproblemen und aktualisieren Sie die Software oder Firmware nach Bedarf.
B. Techniken zur Fehlerbehebung
- Systematischer Ansatz: Gehen Sie bei der Fehlerbehebung systematisch vor, indem Sie die Ursache des Problems identifizieren und isolieren. Beginnen Sie mit den einfachsten Kontrollen und untersuchen Sie nach und nach komplexere Ursachen.
- Dokumentation: Informationen zur Fehlerbehebung und zur Interpretation von Fehlercodes finden Sie in den Maschinenhandbüchern, der Dokumentation und den vom Hersteller bereitgestellten Ressourcen.
- Messung und Prüfung: Verwenden Sie Messinstrumente wie Messuhren, Messschieber und Mikrometer, um Ausrichtung, Abmessungen und Werkzeugrundlauf zu beurteilen. Führen Sie Testschnitte durch, um die Bearbeitungsgenauigkeit zu überprüfen.
- Visuelle Inspektion: Führen Sie eine gründliche Sichtprüfung der Maschine durch und achten Sie auf lockere Befestigungselemente, beschädigte Komponenten oder sichtbare Verschleißerscheinungen.
- Protokolle und Aufzeichnungen: Überprüfen Sie Wartungsprotokolle, Fehlerprotokolle und Aufzeichnungen früherer Probleme, um wiederkehrende Probleme oder Muster zu identifizieren.
- Konsultieren Sie Experten: Wenn Sie auf komplexe oder anhaltende Probleme stoßen, wenden Sie sich an Experten, z. B. an den technischen Support des Herstellers, an qualifizierte Techniker oder an erfahrene Mechaniker, die möglicherweise auf ähnliche Probleme gestoßen sind.
- Sichere Fehlerbehebung: Achten Sie bei der Fehlerbehebung stets auf Sicherheit. Befolgen Sie die Sperr-/Kennzeichnungsverfahren, schalten Sie die Maschine aus und verwenden Sie geeignete persönliche Schutzausrüstung (PSA).
- Dokumentation: Führen Sie detaillierte Aufzeichnungen über Fehlerbehebungsaktivitäten, einschließlich der durchgeführten Schritte, Beobachtungen und angewendeten Lösungen. Diese Aufzeichnungen können für zukünftige Referenzzwecke wertvoll sein.
- Fortlaufendes Lernen: Fördern Sie eine Kultur des kontinuierlichen Lernens und Wissensaustauschs in Ihrem Team. Die bei der Fehlerbehebung gesammelten Erfahrungen können zu verbesserten vorbeugenden Wartungspraktiken führen.
Kapitel 10: Endkontrollen und Tests
In diesem abschließenden Kapitel besprechen wir die wesentlichen Schritte zum Ausführen von Testprogrammen, zum Sicherstellen der Genauigkeit und zum Feinabstimmen Ihrer CNC-Maschineninstallation, um eine optimale Leistung zu erzielen.A. Ausführen von Testprogrammen
- Auswahl an Testprogrammen: Bereiten Sie Testprogramme vor, die eine Reihe von Bearbeitungsvorgängen umfassen, die Ihre CNC-Maschine ausführen wird. Diese Programme sollten grundlegende Bewegungen, Werkzeugwechsel und verschiedene Schneidszenarien umfassen.
- Werkzeug- und Werkstückeinrichtung: Montieren Sie die entsprechenden Werkzeuge und befestigen Sie ein Testwerkstück auf dem Arbeitstisch oder der Vorrichtung der Maschine. Stellen Sie sicher, dass Werkzeugversätze und Werkstückversätze korrekt programmiert sind.
- Probelauf: Führen Sie zunächst einen Trockenlauf ohne Schnitt durch. Dadurch können Sie die Bewegungen der Maschine, Werkzeugwechsel und den gesamten Programmablauf auf Fehler oder unerwartetes Verhalten überprüfen.
- Materialauswahl: Wählen Sie ein Testmaterial, das dem ähnelt, das Sie für Ihre tatsächlichen Bearbeitungsprojekte verwenden möchten. Dadurch wird sichergestellt, dass die Testergebnisse den realen Bedingungen möglichst nahe kommen.
- Schneidtests: Führen Sie die Testprogramme mit Schneidvorgängen aus. Überwachen Sie die Leistung der Maschine und achten Sie dabei genau auf die Genauigkeit des Werkzeugwegs, die Spindelgeschwindigkeit und die Vorschubgeschwindigkeiten.
B. Genauigkeit sicherstellen
- Messung und Inspektion: Messen Sie nach dem Ausführen der Testprogramme die Abmessungen und die Oberflächenbeschaffenheit der Testwerkstücke mit Präzisionsmessgeräten. Vergleichen Sie die Ergebnisse mit den beabsichtigten Designspezifikationen.
- Werkzeuginspektion: Untersuchen Sie die Schneidwerkzeuge auf Anzeichen von Abnutzung, wie z. B. abgebrochene Kanten oder übermäßigen Werkzeugverschleiß. Ersetzen oder schärfen Sie die Werkzeuge nach Bedarf.
- Werkstückinspektion: Untersuchen Sie das Testwerkstück auf etwaige Mängel, Probleme mit der Oberflächenbeschaffenheit oder Abweichungen von der gewünschten Geometrie. Beheben Sie alle bei der Inspektion festgestellten Probleme.
- Feedback und Analyse: Analysieren Sie die Testergebnisse, um etwaige Diskrepanzen oder Abweichungen von den erwarteten Ergebnissen festzustellen. Bestimmen Sie, ob Anpassungen erforderlich sind, um die Genauigkeit zu verbessern.
C. Feinabstimmung
- Werkzeugwegoptimierung: Wenn die Testergebnisse Ungenauigkeiten oder Probleme mit der Oberflächengüte aufdecken, sollten Sie die Optimierung der Werkzeugwege in Ihrer CAM-Software in Betracht ziehen. Passen Sie die Werkzeugwegparameter, die Werkzeugauswahl sowie die Schnittgeschwindigkeiten und Vorschübe nach Bedarf an.
- Anpassungen der Maschinenparameter: Konsultieren Sie die Dokumentation der Maschine, um bestimmte Parameter wie Beschleunigung, Verzögerung und Spielkompensation zu optimieren. Diese Anpassungen können die Genauigkeit verbessern.
- Werkzeug-Offset-Kalibrierung: Werkzeugversätze bei Bedarf neu kalibrieren. Stellen Sie sicher, dass die Maschine die Länge und den Durchmesser des Werkzeugs genau ausgleicht und so Fehler bei der Bearbeitung reduziert.
- Arbeitsversatzkorrektur: Überprüfen und korrigieren Sie Werkstückversätze, um sicherzustellen, dass die Maschine das Werkzeug präzise relativ zum Werkstück positioniert. Kleine Fehler bei der Nullpunktverschiebung können zu erheblichen Ungenauigkeiten führen.
- Erneutes Testen: Nachdem Sie Anpassungen und Feinabstimmungen vorgenommen haben, führen Sie die Testprogramme erneut aus, um die Verbesserungen bei Genauigkeit und Oberflächenbeschaffenheit zu überprüfen.
- Dokumentation: Dokumentieren Sie alle Feinabstimmungsaktivitäten, Anpassungen und Testergebnisse zur späteren Bezugnahme. Diese Dokumentation ist für die Aufrechterhaltung der Konsistenz Ihrer Bearbeitungsvorgänge von großem Wert.
Kapitel 11: Schulung und Kompetenzentwicklung
In diesem Kapitel werden wir die Bedeutung der Schulung und Kompetenzentwicklung sowohl für Maschinenbediener als auch für Wartungspersonal hervorheben. Um einen sicheren und effizienten Betrieb von CNC-Maschinen zu gewährleisten und die Ausrüstung effektiv zu warten und Fehler zu beheben, sind eine ordnungsgemäße Schulung und die Verbesserung der Fähigkeiten von entscheidender Bedeutung.A. Bedienerschulung
- Grundlegende Maschinenbedienung: Bediener sollten eine umfassende Schulung zu den grundlegenden Aspekten des CNC-Maschinenbetriebs erhalten, einschließlich Starten, Herunterfahren, Referenzieren und Tippen der Maschine.
- G-Codes und M-Codes verstehen: Bediener sollten mit der Interpretation und Änderung von G- und M-Codes vertraut sein, die die Bewegungen und Funktionen der Maschine steuern.
- Werkzeughandhabung: Richtige Werkzeughandhabungstechniken, einschließlich Werkzeugwechsel, Werkzeugversätze und Werkzeugkalibrierung, sind unerlässlich, um Unfälle zu vermeiden und die Bearbeitungsgenauigkeit sicherzustellen.
- Werkstückeinrichtung: Die Schulung sollte die Einrichtung des Werkstücks abdecken, einschließlich der Werkstückhalterung, des Materialladens und der Befestigung der Werkstücke am Arbeitstisch oder der Vorrichtung der Maschine.
- Sicherheitsmassnahmen: Bediener müssen mit den Sicherheitsverfahren für CNC-Maschinen, Notabschaltprotokollen und der Verwendung persönlicher Schutzausrüstung (PSA) vertraut sein.
- Grundlagen der Fehlerbehebung: Grundlegende Fähigkeiten zur Fehlerbehebung, wie z. B. das Erkennen häufiger Probleme und das Wissen, wann Hilfe benötigt wird, können Betreibern dabei helfen, kleinere Probleme umgehend zu beheben.
- Qualitätskontrolle: Eine Schulung in Qualitätskontroll- und Inspektionstechniken ist von entscheidender Bedeutung, um sicherzustellen, dass fertige Werkstücke bestimmte Toleranzen und Anforderungen an die Oberflächengüte erfüllen.
- Simulation und Praxis: Bediener sollten Gelegenheit zu praktischen Übungen und Simulationsübungen haben, um ihre Fähigkeiten zu verbessern und Vertrauen in die Bedienung der CNC-Maschine aufzubauen.
B. Wartungsschulung
- Vorbeugende Wartung: Das Wartungspersonal sollte in den routinemäßigen vorbeugenden Wartungsaufgaben speziell für die CNC-Maschine geschult werden, einschließlich Schmier-, Reinigungs- und Inspektionsroutinen.
- Maschinenkomponenten: Damit das Wartungspersonal Probleme effektiv diagnostizieren und lösen kann, ist ein tiefes Verständnis der Maschinenkomponenten, einschließlich Motoren, Sensoren, Antriebe und elektrische Systeme, erforderlich.
- Techniken zur Fehlerbehebung: Fortgeschrittene Fähigkeiten zur Fehlerbehebung, wie z. B. die Diagnose elektrischer, mechanischer und softwarebezogener Probleme, sind für die Minimierung von Ausfallzeiten und die Optimierung der Maschinenleistung unerlässlich.
- Schmierung und Flüssigkeitsmanagement: Die richtige Kenntnis der Schmierstellen, Flüssigkeitstypen und Filtersysteme ist für die Aufrechterhaltung der mechanischen Integrität der Maschine von entscheidender Bedeutung.
- Elektrische Systeme: Das Wartungspersonal sollte in elektrischen Systemen geschult sein, einschließlich des Verständnisses von Schaltplänen, elektrischen Sicherheitsprotokollen und dem Austausch elektrischer Komponenten.
- Erweiterte Kalibrierung: Schulungen zu fortgeschrittenen Kalibrierungstechniken wie Laserausrichtung und Spindelrundlaufmessung können die Genauigkeit der CNC-Maschine verbessern.
- Software-Updates: Um die Steuerungssoftware und die Maschinenfirmware auf dem neuesten Stand zu halten, ist es wichtig, mit Software-Updates und Firmware-Upgrades vertraut zu sein.
C. Verbesserung der Fähigkeiten
- Weiterlernen: Fördern Sie eine Kultur des kontinuierlichen Lernens sowohl bei Bedienern als auch beim Wartungspersonal. Dazu kann die Teilnahme an Workshops, Seminaren und Online-Kursen rund um die CNC-Technologie gehören.
- Fähigkeitsbewertung: Bewerten Sie regelmäßig die Fähigkeiten und Kenntnisse der Bediener und des Wartungspersonals, um Bereiche für Verbesserungen und gezielte Schulungen zu ermitteln.
- Cross-Training: Erwägen Sie die übergreifende Schulung von Bedienern in grundlegenden Wartungsaufgaben und umgekehrt. Dies kann das allgemeine Verständnis und die Zusammenarbeit innerhalb des Teams verbessern.
- Mentorship: Implementieren Sie Mentoring-Programme, bei denen erfahrene Mitarbeiter Anleitung geben und ihr Wissen mit weniger erfahrenen Teammitgliedern teilen können.
- Probleme lösen: Ermutigen Sie Ihre Mitarbeiter, sich aktiv an Problemlösungsübungen und Ursachenanalysen zu beteiligen, und fördern Sie so eine Kultur der proaktiven Fehlerbehebung.
- Rückkopplungsschleife: Richten Sie eine Feedbackschleife ein, in der Bediener und Wartungspersonal Probleme kommunizieren, Erkenntnisse austauschen und Verbesserungen für den Maschinenbetrieb und die Wartung vorschlagen können.
Zusammenfassung
In diesem umfassenden Leitfaden haben wir den komplizierten Prozess der CNC-Maschineninstallation untersucht und ein breites Themenspektrum abgedeckt, um sicherzustellen, dass Ihre CNC-Maschine effektiv und sicher montiert, installiert und betrieben wird. Fassen wir die wichtigsten Punkte zusammen, betonen wir die Bedeutung einer ordnungsgemäßen CNC-Maschineninstallation und blicken wir in die Zukunft der CNC-Technologie.A. Zusammenfassung der wichtigsten Punkte
In diesem Leitfaden haben wir die folgenden wichtigen Punkte behandelt:- CNC-Maschinen verstehen: Wir begannen mit der Diskussion darüber, was CNC-Maschinen sind, welche verschiedenen Typen es gibt und welche wesentlichen Komponenten sie haben.
- Vorbereitung vor der Installation: Wir haben betont, wie wichtig es ist, vor der Installation den Arbeitsbereich vorzubereiten, die Strom- und Elektroanforderungen zu erfüllen und Sicherheitsmaßnahmen umzusetzen.
- Zusammenbau der CNC-Maschine: Es wurden detaillierte Schritte zum Auspacken, Ordnen der Komponenten, Zusammenbau des Maschinenrahmens, Anbringen von Motoren und Antrieben, Installieren des Bedienfelds und Verwalten von Kabeln bereitgestellt.
- Ausrichten und Nivellieren: Wir besprachen die Bedeutung der Ausrichtung und Nivellierung, die erforderlichen Werkzeuge und den schrittweisen Prozess zur Erzielung einer präzisen Ausrichtung.
- Elektroverkabelung: Das Verständnis elektrischer Systeme, die Verkabelung der CNC-Maschine und die Einhaltung von Sicherheitsvorkehrungen bei Elektroarbeiten wurden ausführlich behandelt.
- Installation der Steuerungssoftware: Die Installation von Steuerungssoftware, Kalibrierung und Testverfahren wurden besprochen, um sicherzustellen, dass die CNC-Maschine ordnungsgemäß funktioniert.
- Schmierung und Wartung: Die Bedeutung von Schmierung und Wartung für die Langlebigkeit und Leistung der Maschine wurde hervorgehoben, einschließlich Schmierstellen und Wartungsplänen.
- Sicherheitsmassnahmen: Sicherheitsverfahren, Notabschaltprotokolle und die Verwendung persönlicher Schutzausrüstung (PSA) wurden berücksichtigt, um eine sichere Arbeitsumgebung zu schaffen.
- Fehlerbehebung bei häufigen Installationsproblemen: Es wurden allgemeine Probleme und Fehlerbehebungstechniken bereitgestellt, um Probleme effektiv zu identifizieren und zu lösen.
- Endkontrollen und Tests: Es wurden die Durchführung von Testprogrammen, die Sicherstellung der Genauigkeit und die Feinabstimmung der Maschine besprochen, um eine optimale Leistung zu erzielen.
- Schulung und Kompetenzentwicklung: Hervorgehoben wurde die Bedeutung der Schulung des Bedien- und Wartungspersonals sowie der kontinuierlichen Weiterentwicklung seiner Fähigkeiten.
B. Die Bedeutung einer ordnungsgemäßen CNC-Maschineninstallation
Die ordnungsgemäße Installation einer CNC-Maschine ist die Grundlage für einen erfolgreichen Bearbeitungsvorgang. Es ist aus folgenden Gründen unerlässlich:- Genauigkeit: Eine gut installierte CNC-Maschine produziert mit größerer Wahrscheinlichkeit genaue und präzise Teile und reduziert Ausschuss und Nacharbeit.
- Sicherheit: Eine Installation, die den Sicherheitsstandards und -verfahren entspricht, gewährleistet das Wohlbefinden von Maschinenbedienern und Wartungspersonal.
- Langlebigkeit: Eine ordnungsgemäße Installation und regelmäßige Wartung verlängern die Lebensdauer Ihrer CNC-Maschine und schützen Ihre Investition.
- Effizienz: Eine ordnungsgemäß installierte Maschine arbeitet effizient, minimiert Ausfallzeiten und maximiert die Produktivität.
- Qualität: Die Qualität der Installation wirkt sich direkt auf die Qualität der bearbeiteten Teile aus und führt zu zufriedenen Kunden und einem verbesserten Ruf.
C. Vorausschauen
Mit fortschreitender Technologie werden CNC-Maschinen immer leistungsfähiger und vielseitiger. Es ist wichtig, über die neuesten Entwicklungen, Software-Updates und Best Practices in der CNC-Bearbeitung auf dem Laufenden zu bleiben. Da die CNC-Technologie außerdem immer zugänglicher wird, können mehr Branchen und Unternehmen von ihren Vorteilen profitieren. Zusammenfassend lässt sich sagen, dass die Installation einer CNC-Maschine ein komplexer, aber lohnender Prozess ist. Indem Sie die in diesem Leitfaden beschriebenen Richtlinien und Best Practices befolgen, können Sie die Voraussetzungen für einen erfolgreichen CNC-Bearbeitungsvorgang schaffen. Denken Sie daran, dass kontinuierliches Lernen, Schulung und laufende Wartung der Schlüssel zur Aufrechterhaltung und Verbesserung der Leistung Ihrer CNC-Maschinen sind, während Sie in eine Zukunft voller Möglichkeiten in der Welt der Präzisionsfertigung blicken.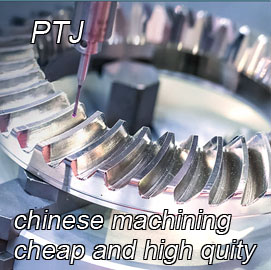
Unsere Dienstleistungen
- 5-Achsen-Bearbeitung
- CNC-Fräsen
- CNC drehen
- Bearbeitungsindustrie
- Bearbeitungsprozess
- Oberflächenbearbeitung
- Metallbearbeitung
- Kunststoffbearbeitung
- Pulvermetallurgie-Form
- Druckguss
- Teile Galerie
Fallstudien
- Autoteile aus Metall
- Maschinenteile
- LED-Kühlkörper
- Gebäudeteile
- Mobilteile
- Medizinische Teile
- Electronic Parts
- Maßgeschneiderte Bearbeitung
- Fahrradteile
Material Liste
- Aluminiumbearbeitung
- Titanbearbeitung
- Edelstahlbearbeitung
- Kupferbearbeitung
- Messingbearbeitung
- Bearbeitung von Superlegierungen
- Peek-Bearbeitung
- UHMW-Bearbeitung
- Einzelbearbeitung
- PA6-Bearbeitung
- PPS-Bearbeitung
- Teflon-Bearbeitung
- Inconel-Bearbeitung
- Werkzeugstahlbearbeitung
- Mehr Material
Teile Galerie