Eine umfassende Anleitung zum Einrichten eines Drehschneidwerkzeugs
Das Einrichten eines Drehwerkzeugs ist eine grundlegende Fähigkeit für jeden Maschinisten, insbesondere wenn es um CNC-Drehmaschinen (Computer Numerical Control) geht. Die richtige Werkzeugeinstellung ist entscheidend für die Erzielung präziser und genauer Bearbeitungsergebnisse. In diesem umfassenden Leitfaden befassen wir uns ausführlich mit der Einrichtung eines Drehschneidwerkzeugs für das CNC-Drehen. Von den Grundlagen der Drehwerkzeugkomponenten bis hin zu fortgeschrittenen Techniken zur Optimierung der Schneidleistung soll dieser Artikel ein umfassendes Verständnis des Prozesses vermitteln. Am Ende dieses Leitfadens verfügen Sie über die erforderlichen Kenntnisse und Fähigkeiten, um ein Drehschneidwerkzeug sicher und präzise einzurichten und so optimale Ergebnisse bei Ihren CNC-Drehvorgängen sicherzustellen.
Drehschneidewerkzeuge verstehen
In der Welt der Zerspanung sind Drehschneidwerkzeuge unverzichtbare Komponenten für die Formung und Umwandlung von Rohmaterialien in präzisionsgefertigte Teile. Unabhängig davon, ob Sie mit herkömmlichen manuellen Drehmaschinen oder modernen CNC-Drehmaschinen arbeiten, ist es unerlässlich, über umfassende Kenntnisse der Schneidwerkzeuge von Drehmaschinen zu verfügen. In diesem Abschnitt werden wir tiefer auf die Eigenschaften, Funktionen und Typen von Drehschneidwerkzeugen eingehen.
Eigenschaften von Drehschneidwerkzeugen
Drehschneidwerkzeuge sind für die Durchführung einer Vielzahl von Bearbeitungsvorgängen konzipiert, wie z. B. Drehen, Plandrehen, Einstechen, Gewindeschneiden und mehr. Diese Tools haben mehrere gemeinsame Merkmale:
- Härte: Schneidwerkzeuge für Drehmaschinen bestehen typischerweise aus Schnellarbeitsstahl (HSS), Hartmetall oder anderen speziellen Werkzeugmaterialien. Diese Materialien werden aufgrund ihrer Härte ausgewählt, sodass das Werkzeug den hohen Temperaturen und Drücken beim Schneiden standhalten kann.
- Innovativ, auf dem neuesten Stand: Die Schneidkante eines Drehwerkzeugs ist der Teil, der tatsächlich Material vom Werkstück entfernt. Es ist scharf und präzise konzipiert und die Geometrie der Schneidkante kann je nach der spezifischen Aufgabe, für die das Werkzeug bestimmt ist, variieren.
- Schaft: Der Schaft des Drehmeißels ist das Teil, das in den Werkzeughalter eingespannt wird. Es verleiht dem Werkzeug während der Arbeit Stabilität und Steifigkeit Bearbeitungsprozess. Schaftausführungen können je nach Werkzeugtyp und Herstellerangaben unterschiedlich sein.
- Werkzeughalter: Der Werkzeughalter ist insbesondere beim CNC-Drehen ein entscheidendes Bauteil, da er das Drehwerkzeug sicher an Ort und Stelle hält. Es muss Stabilität, Präzision und einfache Einstellung bieten, um eine optimale Werkzeugleistung zu gewährleisten.
- Geometrie: Die Geometrie des Schneidwerkzeugs, einschließlich Spanwinkel, Freiwinkel und Spanbrecher, spielt eine wichtige Rolle bei der Bestimmung der Leistung des Werkzeugs. Die richtige Geometrie ist für eine effiziente Materialentfernung und Spanabfuhr von entscheidender Bedeutung.
- Beschichtung: Viele Schneidwerkzeuge für Drehmaschinen sind mit speziellen Beschichtungen wie TiN (Titannitrid) oder TiAlN (Titanaluminiumnitrid) ausgestattet, um die Standzeit zu verlängern, die Reibung zu verringern und die Leistung zu verbessern.
Funktionen von Drehschneidwerkzeugen
Drehschneidwerkzeuge erfüllen im Bearbeitungsprozess mehrere grundlegende Funktionen:
- Materialentfernung: Die Hauptfunktion von Drehschneidwerkzeugen besteht darin, Material von einem Werkstück zu entfernen. Dieser Abtrag kann durch Drehen (Drehen des Werkstücks beim Schneiden), Planen (Erzeugen einer ebenen Oberfläche) oder andere Vorgänge erfolgen.
- Dimensionskontrolle: Schneidwerkzeuge sind dafür verantwortlich, dass die Abmessungen des bearbeiteten Teils den gewünschten Spezifikationen entsprechen. Um genaue und konsistente Ergebnisse zu erzielen, ist eine präzise Steuerung unerlässlich.
- Oberflächenfinish: Die Qualität der Oberflächenbeschaffenheit wird durch die Schärfe des Schneidwerkzeugs, die Geometrie und die verwendeten Schneidparameter bestimmt. Ein gut gewartetes und richtig eingestelltes Schneidwerkzeug trägt zu einer glatten und feinen Oberflächenbeschaffenheit bei.
- Chipkontrolle: Eine wirksame Spankontrolle ist unerlässlich, um die Bildung von Spänen zu verhindern und eine saubere und sichere Arbeitsumgebung aufrechtzuerhalten. Der Spanbrecher einiger Werkzeuge erleichtert die Spanentfernung.
- Effizienz: Drehschneidwerkzeuge sind darauf ausgelegt, Bearbeitungsprozesse effizient und kostengünstig zu gestalten. Sie tragen dazu bei, Materialverschwendung zu minimieren, die Werkzeuglebensdauer zu optimieren und so die Produktionskosten zu senken.
Arten von Drehschneidwerkzeugen
Schneidwerkzeuge für Drehmaschinen sind in verschiedenen Ausführungen erhältlich, die jeweils auf spezifische Bearbeitungsaufgaben zugeschnitten sind. Hier sind einige gängige Typen:
- Drehwerkzeuge: Diese Werkzeuge sind vielseitig einsetzbar und werden für zylindrische Drehbearbeitungen verwendet. Sie können die Außen- und Innenflächen eines Werkstücks formen.
- Bohrwerkzeuge: Bohrwerkzeuge werden eingesetzt, um bestehende Löcher zu vergrößern oder fertigzustellen. Sie sind auf Präzision und Genauigkeit bei der Lochbearbeitung ausgelegt.
- Trennwerkzeuge: Trennwerkzeuge werden verwendet, um ein Werkstück von einem größeren Werkstück zu trennen. Sie erzeugen definierte Trennlinien mit minimalem Abfall.
- Gewindeschneidwerkzeuge: Gewindeschneidwerkzeuge werden zum Schneiden von Gewinden an einem Werkstück verwendet. Sie sind in verschiedenen Formen und Größen für unterschiedliche Gewindeanforderungen erhältlich.
- Nutwerkzeuge: Nutwerkzeuge erzeugen Nuten oder Vertiefungen in einem Werkstück, typischerweise zur Aufnahme von O-Ringen, Sicherungsringen oder anderen Merkmalen.
- Planwerkzeuge: Plandrehwerkzeuge dienen dazu, flache Oberflächen am Ende eines Werkstücks zu erzeugen. Sie werden häufig verwendet, um senkrechte Flächen zu erzielen oder Material von einem Werkstückende abzutragen.
Das Verständnis der Eigenschaften und Funktionen von Drehschneidwerkzeugen ist für die Auswahl des richtigen Werkzeugs für eine bestimmte Bearbeitungsaufgabe von entscheidender Bedeutung. Die Wahl des Schneidwerkzeugs kann sich erheblich auf die Qualität und Effizienz des Bearbeitungsprozesses auswirken und ist daher eine entscheidende Entscheidung bei jedem Drehvorgang. Darüber hinaus sind eine ordnungsgemäße Wartung und Werkzeugeinrichtung von entscheidender Bedeutung, um konsistente und präzise Ergebnisse zu gewährleisten, worauf später in diesem Handbuch ausführlicher eingegangen wird.
Arten von Drehschneidwerkzeugen
Schneidwerkzeuge für Drehmaschinen gibt es in verschiedenen Ausführungen, die jeweils speziell für eine bestimmte Bearbeitungsaufgabe entwickelt wurden. Das Verständnis dieser verschiedenen Arten von Schneidwerkzeugen und ihrer Anwendungen ist für die Auswahl des richtigen Werkzeugs für eine bestimmte Aufgabe von entscheidender Bedeutung. Hier sind einige gängige Arten von Drehschneidwerkzeugen:
Drehwerkzeuge:
- Rundwerkzeug: Wird für allgemeine Dreharbeiten verwendet. Es verfügt über eine abgerundete Schneide und eignet sich sowohl für Schrupp- als auch Schlichtschnitte.
- Diamantwerkzeug: Benannt nach seiner rautenförmigen Schneidkante, eignet es sich ideal für die präzise Bearbeitung verschiedener Materialien, einschließlich Metallen und Kunststoffen.
- Vierkantwerkzeug: Verfügt über eine quadratische Schneidkante und wird typischerweise zum Plandrehen und Eckdrehen verwendet.
Bohrwerkzeuge:Innenbohrstange: Wird zum Vergrößern und Fertigstellen vorhandener Löcher in einem Werkstück verwendet. Es ist auf Präzision ausgelegt und kann genaue Innenmaße erstellen.
Trennwerkzeuge:Trennklinge: Mit diesen Werkzeugen wird ein Werkstück aus einem größeren Werkstück abgetrennt. Sie erzeugen eine definierte Trennlinie mit minimalem Abfall.
Gewindeschneidwerkzeuge:
- Gewindeschneidwerkzeug: Entwickelt zum Erstellen von Außengewinden an einem Werkstück. Sie sind in verschiedenen Formen und Größen für unterschiedliche Gewindeanforderungen erhältlich.
- Thread-Chasing-Tool: Wird zum Verfolgen oder Wiederherstellen vorhandener Threads verwendet. Diese Werkzeuge werden häufig zur Gewindereparatur verwendet.
Nutwerkzeuge:Nutwerkzeug: Diese Werkzeuge erzeugen Nuten oder Aussparungen in einem Werkstück, häufig um O-Ringe, Sicherungsringe oder andere Merkmale aufzunehmen.
Planwerkzeuge:Planwerkzeug: Wird verwendet, um flache Oberflächen am Ende eines Werkstücks zu erzeugen. Es wird häufig verwendet, um senkrechte Flächen zu erzielen oder Material von einem Werkstückende zu entfernen.
Werkzeuge zum Abstechen und Einstechen:Kombinationswerkzeug: Diese vielseitigen Werkzeuge sind sowohl zum Abstechen als auch zum Einstechen konzipiert und sparen Zeit und Werkzeugwechsel.
Werkzeuge zum Gewindeschneiden und Einstechen:Kombiniertes Gewinde- und Nutwerkzeug: Ideal für Arbeiten, die sowohl Gewindeschneiden als auch Nuten am selben Werkstück erfordern.
Anfaswerkzeuge:Anfaswerkzeug: Wird verwendet, um Fasen oder abgeschrägte Kanten am Werkstück zu erzeugen. Fasen werden häufig angewendet, um das Erscheinungsbild und die Montagefreundlichkeit bearbeiteter Teile zu verbessern.
Rändelwerkzeuge:Rändelwerkzeug: Beim Rändeln wird ein strukturiertes Muster auf einem Werkstück erzeugt, typischerweise zur Verbesserung der Griffigkeit oder Ästhetik. Rändelwerkzeuge gibt es in verschiedenen Mustern und Ausführungen.
Umformwerkzeuge:Formular-Tool: Diese Werkzeuge werden speziell für bestimmte Teilegeometrien entwickelt und häufig zur Herstellung komplexer und nicht standardmäßiger Formen verwendet.
Spezialwerkzeuge:Profil-Tools: Wird zum Erstellen komplexer Profile auf einem Werkstück verwendet.
Plan- und Drehwerkzeuge: Diese sind sowohl für Plan- als auch für Drehbearbeitungen konzipiert.
Trennwerkzeuge: Entwickelt zum Durchschneiden des Werkstücks, um separate Teile zu erstellen oder überschüssiges Material zu entfernen.
Die Auswahl des richtigen Schneidwerkzeugs hängt von Faktoren wie dem zu bearbeitenden Material, der gewünschten Oberfläche, den erforderlichen Abmessungen und der spezifischen auszuführenden Operation ab. Um eine effiziente und präzise Bearbeitung zu gewährleisten, ist es wichtig, das richtige Werkzeug auszuwählen und richtig zu warten. Die richtige Werkzeugauswahl sowie die richtige Einrichtung und Einstellung sind entscheidend für die Erzielung qualitativ hochwertiger Ergebnisse bei Dreharbeiten.
Komponenten eines Drehschneidwerkzeugs
Ein Drehschneidwerkzeug ist ein Präzisionsinstrument zum Formen, Schneiden und Entfernen von Material von einem Werkstück. Um zu verstehen, wie es funktioniert und wie man es richtig einrichtet, ist es wichtig, mit seinen verschiedenen Komponenten vertraut zu sein. Hier sind die wichtigsten Komponenten eines Drehschneidwerkzeugs:
- Werkzeughalter:Der Werkzeughalter ist der Teil, der das Schneidwerkzeug an seinem Platz sichert. Es wird am Werkzeughalter der Drehmaschine befestigt und sorgt für die nötige Steifigkeit und Stabilität für Bearbeitungsvorgänge. Werkzeughalter gibt es in verschiedenen Ausführungen, um verschiedene Arten von Schneidwerkzeugen aufzunehmen.
- Schaft:Der Schaft ist der Teil des Schneidwerkzeugs, der in den Werkzeughalter passt. Es ist typischerweise zylindrisch und wird sicher im Halter festgeklemmt. Die Abmessungen und die Form des Schafts können je nach Werkzeugtyp und Design variieren.
- Innovativ, auf dem neuesten Stand:Die Schneidkante ist der scharfe Teil des Werkzeugs, der das Werkstück berührt und Material davon abträgt. Die Qualität der Schneidkante und ihre Geometrie beeinflussen maßgeblich die Schnittleistung und Oberflächengüte. Es ist wichtig, die Schärfe und Präzision der Schneide zu erhalten.
- Einfügen:Viele moderne Schneidwerkzeuge verwenden austauschbare Einsätze, die typischerweise aus harten Materialien wie Hartmetall oder Keramik bestehen. Diese Wendeschneidplatten haben die Schneidgeometrie und werden in einer Tasche am Schneidwerkzeug befestigt. Sie können gedreht oder ausgetauscht werden, wenn sie abgenutzt oder beschädigt sind, was die Lebensdauer des Werkzeugs verlängert.
- Werkzeugnase:Die Werkzeugnase ist die Spitze des Schneidwerkzeugs, an der die Schneidkante und der Einsatz (falls verwendet) zusammenkommen. Für eine präzise Bearbeitung muss die Werkzeugspitze genau positioniert und ausgerichtet sein. Einige Schneidwerkzeuge für Drehmaschinen verfügen über einen einstellbaren Schneidenradius zur besseren Kontrolle der Werkzeugleistung.
- Werkzeugflanke:Die Freifläche ist die Seitenfläche des Schneidwerkzeugs, die nicht Teil der Schneidkante ist. Richtige Freiwinkel an der Werkzeugflanke sorgen für die Spanabfuhr und verringern die Reibung zwischen Werkzeug und Werkstück.
- Werkzeugspanfläche:Die Spanfläche ist die dem Werkstück zugewandte Fläche des Schneidwerkzeugs. Winkel und Zustand der Spanfläche beeinflussen die Spanbildung und die Effizienz des Schneidprozesses. Der Spanwinkel ist ein entscheidender Aspekt der Werkzeuggeometrie.
- Werkzeugfreiwinkel:Der Freiwinkel ist der Winkel zwischen der Werkzeugflanke und der Werkzeugachse. Es sorgt dafür, dass die Schneide nicht am Werkstück reibt, wodurch Reibung und Wärmeentwicklung reduziert werden.
- Werkzeugfreiwinkel:Der Freiwinkel ist der Winkel zwischen der Spanfläche und der Werkstückoberfläche. Es ermöglicht einen reibungslosen Spänefluss und verhindert Störungen zwischen Werkzeug und Werkstück.
- Spanbrecher (falls zutreffend):Einige Schneidwerkzeuge, insbesondere solche, die zum Schruppen verwendet werden, verfügen über einen Spanbrecher, eine Rille oder Kerbe auf der Spanfläche. Der Spanbrecher hilft bei der Kontrolle der Spanbildung und verbessert die Spanabfuhr.
Die ordnungsgemäße Montage, Ausrichtung und Wartung dieser Komponenten ist für eine präzise und effiziente Bearbeitung von entscheidender Bedeutung. Die Wahl des Schneidwerkzeugs und seine Einrichtung müssen auf den spezifischen Bearbeitungsvorgang und das zu bearbeitende Material abgestimmt sein. Um gleichbleibende und qualitativ hochwertige Ergebnisse zu gewährleisten, sind auch regelmäßige Inspektionen und Wartungen der Schneidwerkzeugkomponenten erforderlich.
Auswahl des richtigen Schneidwerkzeugs für den Job
Die Auswahl des richtigen Schneidwerkzeugs ist bei jedem Bearbeitungsvorgang eine entscheidende Entscheidung, da sie großen Einfluss auf die Qualität, Effizienz und Präzision der Arbeit hat. Bei der Auswahl des geeigneten Schneidwerkzeugs für eine bestimmte Aufgabe sollten mehrere Faktoren berücksichtigt werden. Hier finden Sie eine Anleitung zur Auswahl des richtigen Schneidwerkzeugs für Ihr Bearbeitungsprojekt:
1. Material des Werkstücks:
Das zu bearbeitende Material ist einer der kritischsten Faktoren bei der Werkzeugauswahl. Verschiedene Materialien weisen unterschiedliche Härte, Wärmeleitfähigkeit und Abrasivität auf. Folgendes berücksichtigen:
- Härte: Harte Materialien wie gehärteter Stahl oder Keramik erfordern Schneidwerkzeuge mit harten Schneidkanten, wie z. B. Hartmetalleinsätze, um den hohen Schnittkräften standzuhalten.
- Weiche Materialien: Für weichere Materialien wie Aluminium oder Kunststoffe können Schnellarbeitsstahl (HSS) oder andere Werkzeugmaterialien ausreichend sein.
2. Bearbeitungsvorgang:
Der spezifische Vorgang, den Sie ausführen, wie Drehen, Fräsen, Bohren, Gewindeschneiden oder Nuten, bestimmt die Art des Schneidwerkzeugs, das Sie benötigen. Verschiedene Werkzeuge sind für unterschiedliche Aufgaben konzipiert und die Wahl des richtigen Werkzeugs gewährleistet eine optimale Leistung.
3. Schnittgeschwindigkeit und Vorschub:
Bestimmen Sie die erforderliche Schnittgeschwindigkeit und Vorschubgeschwindigkeit basierend auf dem Material und dem Bearbeitungsvorgang. Hersteller von Schneidwerkzeugen geben Empfehlungen für diese Parameter basierend auf der Konstruktion des Werkzeugs und dem zu bearbeitenden Material. Die Einhaltung dieser Empfehlungen ist entscheidend für das Erreichen der gewünschten Ergebnisse.
4. Werkzeuggeometrie:
Berücksichtigen Sie die Geometrie des Schneidwerkzeugs, einschließlich Spanwinkel, Freiwinkel und Schneidenradius. Die Werkzeuggeometrie sollte zum Material und zur Schnittart passen. Beispielsweise eignet sich ein positiver Spanwinkel für weichere Materialien, während ein negativer Spanwinkel für härtere Materialien besser ist.
5. Werkstückabmessungen:
Auch die Größe und Abmessungen des Werkstücks beeinflussen die Werkzeugauswahl. Einige Schneidwerkzeuge eignen sich besser für Schruppvorgänge, um großes Material schnell zu entfernen, während andere für die Schlichtbearbeitung konzipiert sind, um präzise Abmessungen und Oberflächengüten zu erzielen.
6. Anforderungen an die Oberflächenbeschaffenheit:
Wenn Sie eine bestimmte Oberflächenbeschaffenheit benötigen, wählen Sie ein Schneidwerkzeug mit der entsprechenden Geometrie und Schärfe. Schlichtwerkzeuge sorgen für eine glattere Oberflächengüte, während Schruppwerkzeuge effizienter für den Materialabtrag sind.
7. Werkzeugmaterial:
Die Wahl des Werkzeugmaterials ist entscheidend. Hartmetall-, Schnellarbeitsstahl- (HSS), Keramik- und beschichtete Werkzeuge haben alle ihre Vorteile und Einschränkungen. Berücksichtigen Sie bei Ihrer Entscheidung Faktoren wie Standzeit, Verschleißfestigkeit und die Kosten des Werkzeugmaterials.
8. Kühlmittel und Schmierung:
Überlegen Sie, ob der Schneidvorgang Kühlmittel oder Schmierung erfordert. Einige Materialien erzeugen während der Bearbeitung übermäßige Hitze, und die Verwendung des richtigen Kühl- oder Schmiermittels kann die Standzeit des Werkzeugs verlängern und die Schneidleistung verbessern.
9. Werkzeugbeschichtungen:
Viele moderne Schneidwerkzeuge sind mit speziellen Beschichtungen wie TiN (Titannitrid) oder TiAlN (Titanaluminiumnitrid) ausgestattet, um die Verschleißfestigkeit zu verbessern und die Reibung zu verringern. Wählen Sie ein Werkzeug mit einer geeigneten Beschichtung für Ihre spezifische Anwendung.
10. Kostenüberlegungen:
Es ist von entscheidender Bedeutung, die Kosten des Schneidwerkzeugs mit seiner Leistung und Langlebigkeit in Einklang zu bringen. Auch wenn Premium-Werkzeuge eine längere Standzeit und eine bessere Leistung bieten, ist es wichtig, ein Gleichgewicht zu finden, das mit dem Budget Ihres Projekts übereinstimmt.
11. Werkzeughalter- und Maschinenkompatibilität:
Stellen Sie sicher, dass das gewählte Schneidwerkzeug mit dem Werkzeughaltersystem Ihrer Drehmaschine oder Ihres Bearbeitungszentrums kompatibel ist. Der Werkzeughalter sollte dem Schneidwerkzeug während des Bearbeitungsprozesses Stabilität und Steifigkeit verleihen.
Letztendlich hängt das richtige Schneidwerkzeug für die jeweilige Aufgabe von einer Kombination dieser Faktoren ab. Konsultieren Sie immer die Empfehlungen des Werkzeugherstellers und ziehen Sie in Betracht, sich von erfahrenen Maschinenschlossern oder Werkzeugexperten beraten zu lassen, wenn Sie sich nicht sicher sind. Die richtige Werkzeugauswahl und -einrichtung ist von grundlegender Bedeutung für die Erzielung effizienter und präziser Bearbeitungsergebnisse.
Einrichten des Drehschneidwerkzeugs
Das Einrichten eines Drehschneidwerkzeugs für das CNC-Drehen ist ein systematischer Prozess, der mehrere entscheidende Schritte umfasst. Jeder Schritt ist entscheidend, um sicherzustellen, dass das Schneidwerkzeug richtig positioniert und ausgerichtet ist, was letztendlich zu einer präzisen und effizienten Bearbeitung führt. Lassen Sie uns den Prozess Schritt für Schritt durchgehen:
Schritt 1: Vorbereiten der Drehmaschine und des Werkstücks
Bevor Sie das Schneidwerkzeug einrichten können, müssen Sie sowohl die Drehmaschine als auch das Werkstück vorbereiten:
- Sichern Sie das Werkstück: Stellen Sie sicher, dass das Werkstück sicher im Drehfutter oder der Spannzange eingespannt ist. Stellen Sie sicher, dass es sich reibungslos dreht, ohne zu wackeln oder zu vibrieren.
- Sicherheit: Stellen Sie sicher, dass alle Sicherheitsmaßnahmen vorhanden sind, einschließlich der Verwendung geeigneter persönlicher Schutzausrüstung (PSA) und der richtigen Drehmaschineneinstellungen.
Schritt 2: Auswahl des richtigen Werkzeughalters
Der Werkzeughalter ist eine entscheidende Komponente im Rüstprozess. Wählen Sie den geeigneten Werkzeughalter basierend auf Faktoren wie der Art des Schneidwerkzeugs, der durchgeführten Operation und dem Werkzeughaltersystem der Drehmaschine.
- Passen Sie den Werkzeughalter an das Schneidwerkzeug an: Stellen Sie sicher, dass der Werkzeughalter mit der Art und Größe des Schneidwerkzeugs kompatibel ist, das Sie verwenden möchten.
- Steifigkeit des Werkzeughalters: Wählen Sie einen Werkzeughalter, der Stabilität und Steifigkeit bietet. Dies ist insbesondere bei hochpräzisen Anwendungen wichtig.
Schritt 3: Montage des Schneidwerkzeugs
Um das Schneidwerkzeug zu montieren, müssen Sie es im Werkzeughalter befestigen und sicherstellen, dass es fest und richtig positioniert ist:
- Sichern Sie das Schneidwerkzeug: Setzen Sie das Schneidwerkzeug in den Werkzeughalter ein und ziehen Sie alle Klemmmechanismen wie Stellschrauben oder Spannzangen fest. Stellen Sie sicher, dass das Werkzeug sicher gehalten wird.
- Orientierung: Stellen Sie sicher, dass das Schneidwerkzeug in Bezug auf das Werkstück richtig ausgerichtet ist. Das Werkzeug sollte so positioniert werden, dass es im gewünschten Winkel und in der gewünschten Tiefe in das Werkstück eingreift.
Schritt 4: Anpassen der Werkzeughöhe und Mittellinienausrichtung
Die richtige Werkzeughöhe und Mittellinienausrichtung sind entscheidend für das Erreichen präziser Bearbeitungsmaße:
- Einstellung der Werkzeughöhe: Passen Sie die Höhe des Werkzeugs an, um es an der Spindelmittellinie der Drehmaschine auszurichten. Verwenden Sie eine Werkzeughöhenlehre oder einen Prüfstab, um das Werkzeug auf die richtige Höhe einzustellen.
- Mittellinienausrichtung: Stellen Sie sicher, dass das Werkzeug mit der Spindelmittellinie der Drehmaschine ausgerichtet ist. Eine Fehlausrichtung kann zu einer außermittigen Bearbeitung führen und die Teilegenauigkeit beeinträchtigen.
Schritt 5: Einstellen der Schneidenradiuskompensation
Beim CNC-Drehen berücksichtigt die Schneidenradiuskompensation die Geometrie des Schneidwerkzeugs. Dies ist besonders wichtig beim Einsatz von Einsteckwerkzeugen:
- Bestimmen Sie den Schneidenradius: Messen Sie den genauen Nasenradius des von Ihnen verwendeten Schneidwerkzeugeinsatzes oder schauen Sie nach.
- Geben Sie den Radiuswert ein: Geben Sie in der CNC-Steuerungssoftware den gemessenen Werkzeugschneidenradiuswert ein, um sicherzustellen, dass die Maschine bei der Bearbeitung die Werkzeuggeometrie ausgleicht.
Schritt 6: Werkzeugversätze einstellen
Werkzeugversätze berücksichtigen Variationen in den Werkzeugabmessungen und der Werkstückgeometrie. Sie sorgen dafür, dass die Position des Werkzeugs für die Bearbeitung genau angepasst ist:
- Wählen Sie den richtigen Werkzeugversatz: Bestimmen Sie den geeigneten Werkzeugversatzwert basierend auf der Werkzeuggeometrie und dem Bearbeitungsvorgang. Dieser Offsetwert gleicht eventuelle Abweichungen aus.
- Versatzwerte eingeben: Geben Sie die gewählten Versatzwerte in die CNC-Steuerungssoftware ein. Diese Werte weisen die Maschine an, wie die Position des Werkzeugs genau eingestellt werden muss.
Verwenden Sie während des gesamten Werkzeugeinrichtungsprozesses Präzisionsmessgeräte wie Mikrometer, Höhenmessgeräte und Messuhren, um die Werkzeugausrichtung zu überprüfen und zu optimieren. Überprüfen und warten Sie das Schneidwerkzeug regelmäßig, um sicherzustellen, dass es scharf und in gutem Zustand bleibt, da ein gut gewartetes Werkzeug zu konsistenten und genauen Bearbeitungsergebnissen beiträgt.
Das richtige Einrichten des Drehschneidwerkzeugs in diesen Schritten ist entscheidend für die Erzielung optimaler Ergebnisse bei CNC-Drehvorgängen. Präzision und Liebe zum Detail bei der Werkzeugeinrichtung sind Schlüsselfaktoren für die Herstellung hochwertiger bearbeiteter Teile.
Optimierung der Schnittparameter für das CNC-Drehen
Die Optimierung der Schnittparameter ist für die Erzielung effizienter und qualitativ hochwertiger CNC-Drehvorgänge von entscheidender Bedeutung. Die vier wichtigsten Aspekte, die bei der Optimierung der Schnittparameter berücksichtigt werden müssen, sind Geschwindigkeiten und Vorschübe, Schnitttiefe, Schneidflüssigkeiten und Schmiermittel sowie die Verwaltung der Werkzeuglebensdauer.
1. Geschwindigkeiten und Vorschübe:
- A. Schnittgeschwindigkeit (Oberflächengeschwindigkeit):Die Schnittgeschwindigkeit, oft auch Oberflächengeschwindigkeit genannt, ist die Geschwindigkeit, mit der Werkstück und Schneidwerkzeug interagieren. Sie wird in Oberflächenfuß pro Minute (SFM) oder Metern pro Minute (m/min) gemessen. Um die Schnittgeschwindigkeit zu optimieren, berücksichtigen Sie das zu bearbeitende Material und das Material des Werkzeugs. Werkzeuge aus Schnellarbeitsstahl (HSS) haben beispielsweise niedrigere empfohlene Schnittgeschwindigkeiten als Hartmetallwerkzeuge. Konsultieren Sie die Daten der Werkzeughersteller oder Bearbeitungshandbücher, um die empfohlenen Schnittgeschwindigkeiten für bestimmte Materialien und Werkzeuge zu ermitteln.
- B. Vorschubgeschwindigkeit:Der Vorschub ist die lineare Geschwindigkeit, mit der das Schneidwerkzeug in das Werkstück vordringt. Sie wird in Zoll pro Umdrehung (IPR) oder Millimeter pro Umdrehung (mm/Umdrehung) gemessen. Um die Vorschubgeschwindigkeit zu optimieren, berücksichtigen Sie Faktoren wie Materialeigenschaften, Werkzeuggeometrie und die gewünschte Oberflächenbeschaffenheit. Höhere Vorschübe sind im Allgemeinen produktiver, erfordern jedoch möglicherweise robustere Werkzeuge.
- C. Zusammenhang zwischen Schnittgeschwindigkeit und Vorschub:Für einen effizienten Materialabtrag ist das Gleichgewicht zwischen Schnittgeschwindigkeit und Vorschub entscheidend. Eine Erhöhung der Schnittgeschwindigkeit ermöglicht normalerweise eine höhere Vorschubgeschwindigkeit, beide müssen jedoch zusammen angepasst werden, um Werkzeugverschleiß und Überhitzung zu verhindern.
2. Schnitttiefe:
- A. Schnitttiefe (DOC):Die Schnitttiefe ist die Tiefe, die das Schneidwerkzeug in das Werkstück eindringt. Es ist wichtig, die Fähigkeiten des Materials und des Werkzeugs zu berücksichtigen. Optimieren Sie die Schnitttiefe basierend auf der Härte des Materials sowie der Festigkeit und Steifigkeit des Werkzeugs. Bei härteren Materialien können flache Schnitte erforderlich sein, während bei weicheren Materialien tiefere Schnitte erzielt werden können.
- B. Axiale und radiale Schnitttiefe:Berücksichtigen Sie beim CNC-Drehen sowohl die axiale (entlang der Länge des Werkstücks) als auch die radiale (über den Werkstückdurchmesser) Schnitttiefe. Die jeweils optimale Tiefe variiert je nach Vorgang und Material.
3. Schneidflüssigkeiten und Schmierstoffe:
- A. Auswahl der richtigen Schneidflüssigkeit:Schneidflüssigkeiten sind für die Wärmeableitung, die Verringerung der Reibung und die Verbesserung der Spanabfuhr unerlässlich. Wählen Sie je nach Material und Bearbeitungsvorgang die geeignete Schneidflüssigkeit. Für verschiedene Materialien können wasserlösliche Kühlmittel, Kühlmittel auf Mineralölbasis oder synthetische Kühlmittel bevorzugt werden.
- B. Richtige Anwendung:Tragen Sie Schneidflüssigkeiten effektiv auf den Schneidbereich auf, um eine ausreichende Schmierung und Kühlung sicherzustellen. Dies kann je nach Leistungsfähigkeit der Maschine durch Flutkühlung, Nebelsysteme oder Kühlmittelzufuhr durch das Werkzeug erfolgen.
- C. Überwachung und Wartung:Überwachen Sie regelmäßig den Füllstand, den Zustand und die Verschmutzung der Schneidflüssigkeit, um sicherzustellen, dass sie wirksam bleiben. Warten Sie Schneidflüssigkeitssysteme, um Probleme wie Bakterienwachstum und -abbau zu verhindern.
4. Werkzeugstandzeitmanagement:
- A. Werkzeuginspektion und -wartung:Führen Sie ein Programm zur routinemäßigen Werkzeuginspektion und -wartung ein, um sicherzustellen, dass die Werkzeuge in gutem Zustand sind. Stumpfe oder beschädigte Werkzeuge können zu einer schlechten Bearbeitungsqualität und einer verkürzten Werkzeugstandzeit führen.
- B. Zeitplan für den Werkzeugaustausch:Erstellen Sie einen Werkzeugwechselplan basierend auf Faktoren wie Werkzeugverschleiß, Maschinenverfügbarkeit und Produktionsanforderungen. Dies trägt dazu bei, unerwartete Werkzeugausfälle zu verhindern und eine gleichbleibende Bearbeitungsqualität aufrechtzuerhalten.
- C. Optimierung der Werkzeuglebensdauer:Einige Werkzeugmaterialien und -beschichtungen bieten eine längere Standzeit. Erwägen Sie den Einsatz von Hochleistungswerkzeugen, um die Werkzeuglebensdauer zu optimieren und Produktionsausfallzeiten zu reduzieren.
- D. Werkzeugspankontrolle:Eine effektive Spankontrolle, einschließlich der Verwendung von Spanbrechern und der richtigen Werkzeuggeometrie, kann die Werkzeuglebensdauer verlängern, indem der spanbedingte Verschleiß reduziert wird.
Die Optimierung der Schnittparameter beim CNC-Drehen ist ein kontinuierlicher Prozess. Möglicherweise sind Experimente und Feinabstimmungen erforderlich, um die besten Parameter für eine bestimmte Anwendung zu finden. Überwachen und passen Sie diese Parameter regelmäßig an, um eine optimale Bearbeitungsleistung, Werkzeuglebensdauer und Teilequalität sicherzustellen. Richtig optimierte Schnittparameter verbessern nicht nur die Bearbeitungseffizienz, sondern reduzieren auch den Werkzeugverschleiß und letztendlich die Produktionskosten.
Beheben häufiger Probleme bei der Werkzeugeinstellung
Die Behebung häufiger Probleme bei der Werkzeugeinstellung ist eine wesentliche Fähigkeit für Maschinisten und CNC-Bediener. Das Verständnis und die Bewältigung dieser Probleme können dazu beitragen, die Präzision und Qualität der Bearbeitungsvorgänge aufrechtzuerhalten. Hier sind einige häufige Probleme bei der Werkzeugeinstellung und ihre Lösungen:
1. Tool-Chatter:
Problem: Werkzeugrattern entsteht, wenn das Schneidwerkzeug während des Bearbeitungsprozesses vibriert, was zu einer schlechten Oberflächengüte, Werkzeugverschleiß und möglichen Schäden am Werkstück führt.
Lösung:
- Geschwindigkeit reduzieren oder Vorschub erhöhen: Passen Sie die Schnittparameter an, indem Sie entweder die Schnittgeschwindigkeit verringern oder den Vorschub erhöhen. Diese Änderung kann Vibrationen dämpfen und Rattern reduzieren.
- Werkzeugsteifigkeit prüfen: Stellen Sie sicher, dass Werkzeughalter und Werkzeug ordnungsgemäß befestigt sind und dass das Werkzeug nicht zu weit aus dem Halter herausragt.
- Werkstückspannung prüfen: Stellen Sie sicher, dass das Werkstück sicher eingespannt ist, um werkstückbedingte Vibrationen zu vermeiden.
- Verwenden Sie Dämpfungstechniken: Einige Maschinen verfügen über Funktionen zur Vibrationsdämpfung. Falls verfügbar, erwägen Sie deren Verwendung.
- Wählen Sie ein steiferes Werkzeug: Ein steiferes Werkzeug, beispielsweise eines mit weniger Rillen, kann zur Reduzierung von Rattern beitragen.
2. Schlechte Oberflächenbeschaffenheit:
Problem: Eine schlechte Oberflächengüte kann aus Problemen mit der Werkzeugeinrichtung oder den Schnittparametern resultieren und zu rauen oder inkonsistenten Oberflächen auf dem Werkstück führen.
Lösung:
- Werkzeuggeometrie prüfen: Stellen Sie sicher, dass die Geometrie des Schneidwerkzeugs für die Operation geeignet ist. Ein scharfes Werkzeug mit der richtigen Geometrie ist entscheidend für die Erzielung einer guten Oberflächengüte.
- Schnittparameter optimieren: Passen Sie Schnittgeschwindigkeit, Vorschubgeschwindigkeit und Schnitttiefe an, um die beste Kombination für das jeweilige Material und den jeweiligen Vorgang zu finden.
- Auf Werkzeugverschleiß prüfen: Überprüfen Sie das Werkzeug auf Anzeichen von Abnutzung oder Beschädigungen, wie z. B. abgebrochene Kanten. Tauschen Sie das Werkzeug nach Bedarf aus oder schleifen Sie es nach.
- Verwenden Sie geeignete Schneidflüssigkeit: Eine ordnungsgemäße Schmierung und Kühlung kann die Oberflächenbeschaffenheit erheblich beeinflussen. Verwenden Sie die richtige Schneidflüssigkeit für das Material und den Einsatz.
- Vibrationen minimieren: Beheben Sie Vibrationsprobleme, um die Entstehung von Oberflächenunregelmäßigkeiten zu vermeiden.
3. Maßungenauigkeiten:
Problem: Teile können aufgrund falsch ausgerichteter Werkzeuge oder Werkzeugverschleiß falsche Abmessungen haben.
Lösung:
- Überprüfen Sie das Werkzeug-Setup: Stellen Sie sicher, dass das Werkzeug korrekt eingerichtet ist und in Bezug auf das Werkstück die richtige Höhe und Ausrichtung hat.
- Maschine kalibrieren: Stellen Sie sicher, dass die CNC-Maschine ordnungsgemäß kalibriert ist und die Werkzeugversätze und Werkzeugdaten genau interpretiert.
- Werkzeugversätze anpassen: Korrigieren Sie etwaige Fehler bei den Werkzeugversätzen, indem Sie das Werkzeug genau vermessen und die richtigen Versatzwerte in die CNC-Steuerung eingeben.
- Werkzeugverschleiß prüfen: Überprüfen Sie das Schneidwerkzeug regelmäßig auf Verschleiß und ersetzen oder schleifen Sie es bei Bedarf nach.
4. Probleme mit der Spankontrolle:
Problem: Eine unsachgemäße Spankontrolle kann zu Problemen wie Spanverstopfung, schlechter Spanabfuhr und Schäden am Werkstück oder Werkzeug führen.
Lösung:
- Wählen Sie die richtige Werkzeuggeometrie: Wählen Sie ein Schneidwerkzeug mit dem passenden Spanbrecher oder der passenden Geometrie für das Material und den Vorgang.
- Schnittparameter optimieren: Passen Sie Vorschübe, Schnittgeschwindigkeiten und Schnitttiefen an, um die Spanbildung und -abfuhr zu optimieren.
- Verwenden Sie eine ausreichende Schmierung: Der richtige Einsatz von Schneidflüssigkeiten kann zur Schmierung beitragen und die Spanabfuhr erleichtern.
- Werkzeug- und Werkstückausrichtung prüfen: Stellen Sie sicher, dass das Werkzeug korrekt zum Werkstück ausgerichtet ist, um Probleme durch Späne zu vermeiden.
5. Werkzeugbruch:
Problem: Werkzeugbrüche können durch übermäßige Krafteinwirkung, falsche Werkzeugeinstellung oder Materialprobleme verursacht werden.
Lösung:
- Schnittparameter optimieren: Reduzieren Sie die Schnittkräfte, indem Sie Parameter wie Vorschubraten, Schnittgeschwindigkeiten und Schnitttiefen anpassen.
- Überprüfen Sie das Werkzeug-Setup: Stellen Sie sicher, dass das Werkzeug sicher im Werkzeughalter montiert ist und richtig ausgerichtet ist.
- Verwenden Sie das richtige Werkzeugmaterial: Wählen Sie das richtige Werkzeugmaterial für das spezifische Material, das Sie bearbeiten. Hartmetallwerkzeuge eignen sich beispielsweise besser für harte Materialien.
- Auf Werkzeugverschleiß prüfen: Überprüfen Sie das Werkzeug regelmäßig auf Verschleißerscheinungen und tauschen Sie es aus, bevor es übermäßig abgenutzt ist und zum Bruch neigt.
Die Lösung dieser häufigen Probleme bei der Werkzeugeinstellung erfordert eine Kombination aus angemessener Schulung, regelmäßiger Wartung und einem systematischen Ansatz zur Fehlerbehebung. Die Fähigkeit, werkzeugbezogene Probleme zu diagnostizieren und zu lösen, ist entscheidend für die Erzielung hochwertiger und effizienter Bearbeitungsergebnisse.
Fazit
Der Prozess der Einrichtung und Optimierung von Drehschneidwerkzeugen für das CNC-Drehen ist ein entscheidender Aspekt der Bearbeitung, der sich erheblich auf die Qualität, Effizienz und Präzision von Fertigungsprozessen auswirkt. Ein tiefes Verständnis der Komponenten und Funktionen von Schneidwerkzeugen sowie der Faktoren, die bei der Werkzeugauswahl eine Rolle spielen, ist für Maschinisten und CNC-Bediener unerlässlich.
Das richtige Einrichten eines Schneidwerkzeugs erfordert einen systematischen Ansatz, von der Vorbereitung der Drehmaschine und des Werkstücks über die Auswahl des richtigen Werkzeughalters, die Montage des Werkzeugs, die Einstellung der Werkzeughöhe und Mittellinienausrichtung bis hin zur Konfiguration der Schneidenradiuskompensation und der Werkzeugversätze. Jeder Schritt spielt eine entscheidende Rolle für die Erzielung präziser und effizienter Bearbeitungsergebnisse.
Die Optimierung der Schnittparameter, einschließlich Geschwindigkeiten und Vorschübe, Schnitttiefe, Schneidflüssigkeiten und Werkzeuglebensdauermanagement, ist ein weiterer wichtiger Aspekt beim CNC-Drehen. Durch die sorgfältige Auswahl der richtigen Parameter können Maschinisten die Produktivität steigern, die Langlebigkeit der Werkzeuge aufrechterhalten und die Qualität der Oberflächengüte verbessern.
Schließlich ist die Fähigkeit, häufig auftretende Probleme bei der Werkzeugeinstellung wie Werkzeugrattern, schlechte Oberflächengüte, Maßungenauigkeiten, Probleme bei der Spankontrolle und Werkzeugbruch beheben zu können, für die Aufrechterhaltung konsistenter und qualitativ hochwertiger Bearbeitungsergebnisse von entscheidender Bedeutung. Durch die Identifizierung dieser Probleme und die Implementierung geeigneter Lösungen wird sichergestellt, dass der Bearbeitungsprozess reibungslos und effizient bleibt.
Insgesamt befähigt ein umfassendes Verständnis der Schneidwerkzeuge von Drehmaschinen und ihrer Einrichtung in Kombination mit der Fähigkeit, Schneidparameter zu optimieren und Probleme zu beheben, Maschinenführer dazu, bei CNC-Drehvorgängen die besten Ergebnisse zu erzielen. Kontinuierliches Lernen, Training und Erfahrung sind der Schlüssel zur Weiterentwicklung dieser Fähigkeiten und zur Gewährleistung erfolgreicher Bearbeitungsprozesse.
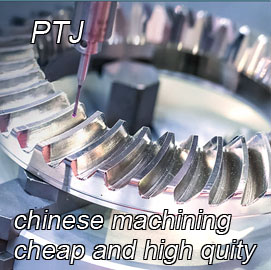
- 5-Achsen-Bearbeitung
- CNC-Fräsen
- CNC drehen
- Bearbeitungsindustrie
- Bearbeitungsprozess
- Oberflächenbearbeitung
- Metallbearbeitung
- Kunststoffbearbeitung
- Pulvermetallurgie-Form
- Druckguss
- Teile Galerie
- Autoteile aus Metall
- Maschinenteile
- LED-Kühlkörper
- Gebäudeteile
- Mobilteile
- Medizinische Teile
- Electronic Parts
- Maßgeschneiderte Bearbeitung
- Fahrradteile
- Aluminiumbearbeitung
- Titanbearbeitung
- Edelstahlbearbeitung
- Kupferbearbeitung
- Messingbearbeitung
- Bearbeitung von Superlegierungen
- Peek-Bearbeitung
- UHMW-Bearbeitung
- Einzelbearbeitung
- PA6-Bearbeitung
- PPS-Bearbeitung
- Teflon-Bearbeitung
- Inconel-Bearbeitung
- Werkzeugstahlbearbeitung
- Mehr Material