So reduzieren Sie Rattern beim CNC-Fräsen – Tipps zur Minimierung von Bearbeitungsvibrationen
2023-10-30
CNC-Fräsen ist leistungsstark und vielseitig Bearbeitungsprozess Dies ermöglicht eine präzise und komplexe Teilefertigung. Ein häufiges Problem, auf das Maschinisten beim CNC-Fräsen jedoch stoßen, ist das Rattern. Unter Rattern versteht man im Zusammenhang mit der Bearbeitung unerwünschte Vibrationen oder Schwingungen, die beim Schneiden auftreten. Dies kann zu einer schlechten Oberflächengüte, einer verkürzten Werkzeugstandzeit und sogar zu Schäden an der Maschine führen. In diesem umfassenden Leitfaden untersuchen wir die Ursachen von Rattern beim CNC-Fräsen und stellen eine breite Palette von Tipps und Techniken zur Verfügung, um diese effektiv zu reduzieren oder zu beseitigen.
Chatter verstehen in CNC Fräsen
Was ist Rattern beim CNC-Fräsen?
Rattern ist im Kontext des CNC-Fräsens ein störendes und schädliches Phänomen, das während des Bearbeitungsprozesses auftritt. Es äußert sich in unerwünschten Vibrationen oder Schwingungen der Werkzeugmaschine, des Werkstücks oder des Schneidwerkzeugs. Dieses Phänomen ist oft durch ein deutliches, unangenehmes Geräusch gekennzeichnet und kann schwerwiegende Auswirkungen auf die Bearbeitungsvorgänge haben. Um Chatter umfassender zu verstehen, analysieren wir seine wichtigsten Komponenten und Dynamiken.Hauptkomponenten von Chatter:
- Werkzeugmaschine: Die CNC-Werkzeugmaschine, einschließlich ihrer Strukturkomponenten, Spindel und Lagers, können eine Quelle von Rattern sein, wenn es ihnen an Stabilität mangelt oder sie nicht ordnungsgemäß gewartet werden.
- Werkstück: Das zu bearbeitende Material und seine Eigenschaften wie Härte und Befestigung können das Rattern beeinflussen.
- Werkzeugbau: Die Wahl der Schneidwerkzeuge, ihre Geometrie, ihr Zustand und ihr Material können eine erhebliche Rolle beim Auftreten von Rattern spielen.
- Schnittparameter: Die Auswahl der Schnittparameter, einschließlich Vorschubgeschwindigkeit, Schnittgeschwindigkeit und Schnitttiefe, kann die Stabilität des Bearbeitungsprozesses beeinflussen.
Dynamik des Chatters:
Rattern entsteht, wenn ein Ungleichgewicht zwischen den auf das Schneidwerkzeug wirkenden Kräften und dem Widerstand des Werkstückmaterials besteht. Dieses Ungleichgewicht führt zu Vibrationen, die eine Reihe negativer Folgen haben können, darunter:- Schlechte Oberflächenbeschaffenheit: Durch Rattern verursachte Vibrationen können unregelmäßige und raue Oberflächen auf dem bearbeiteten Teil hinterlassen und dessen Qualität und Präzision beeinträchtigen.
- Reduzierte Werkzeugstandzeit: Die ständigen, schnellen Schwingungen im Werkzeug können zu übermäßigem Werkzeugverschleiß führen und dessen Lebensdauer erheblich verkürzen.
- Maschinenschaden: Eine längere Einwirkung von Vibrationen kann die Integrität der CNC-Maschine selbst gefährden. Im Laufe der Zeit kann die angesammelte mechanische Belastung zu kostspieligen Reparaturen und Ausfallzeiten führen.
- Produktivitätsverlust: Rattern machen häufig eine Reduzierung der Schnittgeschwindigkeit oder des Vorschubs erforderlich, um das Problem zu mildern, was zu längeren Bearbeitungszeiten und einer verringerten Gesamtproduktivität führen kann.
Warum Chatter wichtig ist
Für jeden CNC-Fräsvorgang ist es von entscheidender Bedeutung zu verstehen, warum Rattern wichtig ist. Auch wenn es als Ärgernis oder Unannehmlichkeit erscheinen mag, geht seine Wirkung weit darüber hinaus. Aus folgenden Gründen gibt Chatter Anlass zu großer Sorge:- Qualität des fertigen Teils: Rattern kann die Qualität und Präzision des bearbeiteten Teils erheblich beeinträchtigen. Wenn es Ihr Ziel ist, hochpräzise Bauteile herzustellen, können Rattern ein großes Hindernis darstellen.
- Werkzeuglebensdauer: Durch Rattern verursachte Vibrationen können zu schnellem Werkzeugverschleiß und -bruch führen. Dies führt zu höheren Werkzeugwechselkosten und häufigeren Unterbrechungen des Bearbeitungsprozesses.
- Maschinenintegrität: Eine längere Einwirkung von Vibrationen kann zu Schäden an der CNC-Maschine selbst führen. Dazu gehören Verschleiß an Maschinenkomponenten, Spindelschäden und andere strukturelle Probleme.
- Produktivität: Chatter zwingt Maschinisten dazu, Schnittgeschwindigkeiten und Vorschübe zu reduzieren, um weitere Probleme zu vermeiden. Dieses langsamere Tempo verringert die Gesamtproduktivität und kann zu Verzögerungen bei der Erledigung von Bearbeitungsaufgaben führen.
- Sicherheitsbedenken: Rattern kann sogar ein Sicherheitsrisiko in der Werkstatt darstellen. Die dadurch entstehenden Vibrationen und Instabilitäten können zu Unfällen, Werkzeugauswürfen oder Werkstückschäden führen.
Was sind Bearbeitungsvibrationen?
Bearbeitungsvibrationen, im Zusammenhang mit Bearbeitungsprozessen oft einfach als „Vibrationen“ bezeichnet, sind unerwünschte und oszillierende Bewegungen oder Schwingungen, die beim Schneiden oder Bearbeiten von Materialien auftreten. Dieses Phänomen äußert sich in schnellen Hin- und Herbewegungen, typischerweise in Form von Vibrationen, Erschütterungen oder Schwingungen, in der Werkzeugmaschine, dem Werkstück, dem Schneidwerkzeug oder einer Kombination dieser Komponenten. Bearbeitungsvibrationen sind ein häufiges Problem bei verschiedenen Bearbeitungsprozessen, einschließlich Drehen, Fräsen, Bohren und Schleifen. Zu den wichtigsten Merkmalen der Bearbeitungsvibration gehören:- Unerwünschte Bewegung: Vibration stellt eine unerwünschte Bewegung im Bearbeitungssystem dar. Dies kann zu Instabilität führen und die Genauigkeit und Qualität der bearbeiteten Teile beeinträchtigen.
- Wiederholte Schwingung: Vibrationen treten typischerweise bei einer oder mehreren bestimmten Frequenzen auf und führen zu wiederholten Hin- und Herbewegungen. Diese Schwingungen machen sich in der Bewegung des Werkstücks, des Schneidwerkzeugs oder der gesamten Maschine bemerkbar.
- Noise: Vibrationen erzeugen häufig ein charakteristisches Geräusch, das darauf zurückzuführen sein kann, dass sich Komponenten gegeneinander bewegen oder vibrieren. Dieses Geräusch kann als akustischer Hinweis auf Vibrationen dienen.
- Reduzierte Oberflächenbeschaffenheit: Vibrationen können zu unebenen oder unregelmäßigen Oberflächenbeschaffenheiten der bearbeiteten Teile führen und deren Qualität und Präzision beeinträchtigen.
- Verkürzte Werkzeugstandzeit: Die mit Vibrationen verbundenen schnellen und unregelmäßigen Bewegungen können zu übermäßigem Verschleiß und Werkzeugschäden führen, was einen häufigen Werkzeugwechsel erforderlich macht.
- Maschinenverschleiß und -schäden: Eine längere Einwirkung von Vibrationen kann den Verschleiß und die Beschädigung von Maschinenkomponenten, einschließlich Spindeln, Lagern und Strukturelementen, beschleunigen.
- Ungenauigkeiten und Maßabweichungen: Vibrationen können zu einer Durchbiegung des Werkstücks oder Werkzeugs führen, was zu Ungenauigkeiten und Maßabweichungen im Endprodukt führt.
Ursachen für Chatter
Rattern beim CNC-Fräsen ist ein komplexes Phänomen, das durch eine Kombination verschiedener Faktoren beeinflusst wird. Das Verständnis dieser Ursachen ist von grundlegender Bedeutung für die wirksame Bekämpfung und Eindämmung von Diskussionen. Diese Faktoren lassen sich grob in vier Schlüsselbereiche einteilen:1. Werkzeugmaschinenfaktoren
Die Eigenschaften und der Zustand der CNC-Maschine selbst tragen maßgeblich zum Rattern bei. Mehrere maschinenbezogene Faktoren können das Auftreten von Rattern beeinflussen:A. Steifigkeit:
Steifheit bezieht sich auf die Fähigkeit der Maschine, Verformungen oder Biegungen während des Bearbeitungsprozesses zu widerstehen. Eine steifere Maschine neigt weniger zum Rattern. Maschinenkomponenten wie Maschinenbett, Säulen und Spindel sollten im Hinblick auf eine hohe Steifigkeit konstruiert und gebaut werden. Die Steifigkeit der Maschine sorgt für stabile Schnittbedingungen und verringert die Wahrscheinlichkeit von Rattern.B. Spulengeschwindigkeit:
Das Spulengeschwindigkeit ist ein entscheidender Faktor bei der Kontrolle von Chatter. Die Spindeldrehzahl sollte auf das Werkstückmaterial und das verwendete Schneidwerkzeug abgestimmt sein. Der Betrieb mit der richtigen Spindeldrehzahl hilft, Rattern zu vermeiden, indem ein stabiler und ausgewogener Schneidprozess aufrechterhalten wird.C. Dämpfung:
Einige CNC-Maschinen sind mit einer integrierten Steuerung ausgestattet Dämpfungssysteme Entwickelt, um Vibrationen während der Bearbeitung zu absorbieren. Diese Dämpfungssysteme tragen dazu bei, Vibrationen zu reduzieren, insbesondere bei Bearbeitungsvorgängen mit hoher Geschwindigkeit. Die Investition in eine Maschine mit fortschrittlichen Dämpfungsfunktionen kann eine praktische Lösung zur Minimierung von Vibrationen sein.D. Genauigkeit und Präzision:
Maschinen mit höherem Niveau Präzision und Genauigkeit Es ist weniger wahrscheinlich, dass sie Geschwätz erleben. Die Präzision der Maschine stellt sicher, dass sie konstante Schnittbedingungen aufrechterhält, wodurch das Risiko von Vibrationen und Instabilität während der Bearbeitung verringert wird.2. Werkstückfaktoren
Das Werkstück, einschließlich seiner Materialeigenschaften, Größe und Befestigung, kann das Rattern erheblich beeinflussen. Zu den werkstückbezogenen Faktoren gehören:A. Materialeigenschaften:
Das Materialeigenschaften des Werkstückmaterials sind entscheidende Überlegungen. Die Härte, Dichte und Wärmeleitfähigkeit des Materials beeinflussen seine Fähigkeit, bei der Bearbeitung entstehende Wärme aufzunehmen und abzuleiten. Diese Eigenschaften können entweder stabile Schnittbedingungen fördern oder zu Rattern führen.B. Werkstückbefestigung:
Befestigung bezieht sich darauf, wie das Werkstück während der Bearbeitung sicher eingespannt bzw. an Ort und Stelle gehalten wird. Eine ordnungsgemäße Befestigung ist wichtig, um Rattern zu verhindern, da jede Bewegung oder Vibration im Werkstück den Schneidvorgang stören kann. Das sichere Einspannen des Werkstücks sorgt für Stabilität und verringert die Gefahr von Rattern.C. Überhang:
Das Überhang ist der Abstand zwischen Werkstück und Werkzeughalter. Längere Überhänge können aufgrund der stärkeren Werkzeugablenkung das Rattern verstärken. Eine Reduzierung des Überhangs oder die Verwendung kürzerer Werkzeuge kann helfen, diesen Effekt abzumildern.3. Werkzeugfaktoren
Die Wahl der Schneidwerkzeuge, ihr Zustand, ihre Geometrie und ihr Material können das Rattern erheblich beeinflussen. Zu den zu berücksichtigenden werkzeugbezogenen Faktoren gehören:A. Werkzeugmaterial:
Auswahl der entsprechenden Werkzeugmaterial abhängig vom Werkstückmaterial ist entscheidend. Verschiedene Materialien bieten unterschiedliche Grade an Verschleißfestigkeit und Hitzebeständigkeit. Die Wahl des richtigen Werkzeugmaterials kann den Werkzeugverschleiß und die Wahrscheinlichkeit von Rattern verringern.B. Werkzeuggeometrie:
Das Werkzeuggeometrie, einschließlich der Anzahl der Spannuten, des Spanwinkels und des Spiralwinkels, können die Schnittkräfte und damit das Rattern beeinflussen. Werkzeuggeometrien, die eine bessere Spankontrolle ermöglichen und die Schnittkräfte reduzieren, sind für ratteranfällige Materialien vorzuziehen.C. Werkzeugzustand:
Das Zustand der Schneidwerkzeuge spielt eine wesentliche Rolle beim Auftreten von Rattern. Abgenutzte oder beschädigte Werkzeuge verursachen eher Rattern. Um sicherzustellen, dass die Werkzeuge in optimalem Zustand sind, sind eine regelmäßige Inspektion und Wartung der Werkzeuge unerlässlich.4. Schnittparameter
Die Wahl der Schnittparameter wie Vorschubgeschwindigkeit, Schnittgeschwindigkeit und Schnitttiefe wirkt sich direkt auf das Auftreten von Rattern aus. Zu den schneidparameterbezogenen Faktoren gehören:A. Vorschubgeschwindigkeit:
An unangemessene Vorschubgeschwindigkeit Ein zu hoher Wert kann zu übermäßigen Schnittkräften und in der Folge zu Rattern führen. Um Rattern zu verhindern, ist es wichtig, die Vorschubgeschwindigkeit mit anderen Schnittparametern in Einklang zu bringen.B. Schneidgeschwindigkeit:
Das Schneidgeschwindigkeit müssen je nach verwendetem Material und Werkzeug richtig ausgewählt werden. Eine falsche Schnittgeschwindigkeit, egal ob zu hoch oder zu niedrig, kann zu Rattern führen. Die richtige Schnittgeschwindigkeit hängt von Faktoren wie Materialart, Werkzeugmaterial und Werkzeuggeometrie ab.C. Schnitttiefe:
Das Schnitttiefe beeinflusst die Spanbelastung und die auf das Werkzeug wirkenden Kräfte. Ein tiefer Schnitt kann das Werkzeug überlasten und zu Vibrationen und Rattern führen. Durch die Verringerung der Schnitttiefe kann Rattern vermieden werden, insbesondere bei der Bearbeitung anspruchsvoller Materialien. Das Verständnis des Zusammenspiels dieser Faktoren und ihrer spezifischen Auswirkungen auf das Rattern ist entscheidend für die Entwicklung effektiver Strategien zur Minimierung oder Beseitigung dieses schädlichen Phänomens beim CNC-Fräsen. In den folgenden Abschnitten werden wir uns mit verschiedenen Strategien und Best Practices zur Reduzierung von Chatter durch die Beseitigung dieser Grundursachen befassen.Strategien zur Reduzierung von Chatter
Rattern beim CNC-Fräsen kann eine dauerhafte Herausforderung sein, es gibt jedoch zahlreiche wirksame Strategien und Techniken, um sie zu minimieren oder zu beseitigen. Diese Strategien umfassen Verbesserungen an Werkzeugmaschinen, die richtige Werkstückvorbereitung, Werkzeugauswahl und -wartung, Optimierung von Schnittparametern, Werkzeugwegplanung, Dämpfungstechniken und den Einsatz von Überwachungs- und Steuerungssystemen. Lassen Sie uns jede dieser Strategien im Detail untersuchen:1. Verbesserungen an Werkzeugmaschinen
Die Verbesserung der CNC-Maschine selbst ist eine wirksame Möglichkeit, Rattern zu reduzieren. Hier sind einige Ansätze, die Sie in Betracht ziehen sollten:A. Upgrade auf eine steifere Maschine:
Wenn es Ihrer aktuellen Maschine an Steifigkeit und Stabilität mangelt, sollten Sie ein Upgrade auf eine robustere Maschine in Betracht ziehen. Eine starre Maschine minimiert die Durchbiegung und kann Vibrationen während des Bearbeitungsprozesses wirksam dämpfen, wodurch die Wahrscheinlichkeit von Rattern verringert wird.B. Dämpfungssysteme:
Einige Maschinen sind mit eingebautem ausgestattet Dämpfungssysteme Entwickelt, um Vibrationen zu absorbieren. Diese Systeme eignen sich besonders zur Reduzierung von Rattern bei Hochgeschwindigkeitsbearbeitungen. Durch die Aufrüstung auf eine Maschine mit erweiterten Dämpfungsfunktionen kann das Rattern erheblich reduziert werden.C. Regelmäßige Maschinenwartung:
Regelmäßige Wartung ist von entscheidender Bedeutung. Überprüfen und justieren Sie regelmäßig kritische Maschinenkomponenten, um sicherzustellen, dass die Maschine optimal funktioniert. Dazu gehören das Überprüfen und Anziehen von Schrauben, das Kalibrieren der Spindel und die Aufrechterhaltung des Gesamtzustands der Maschine.2. Werkstückvorbereitung
Um Rattern zu verhindern, ist eine ordnungsgemäße Werkstückvorbereitung unerlässlich. Betrachten Sie die folgenden Schritte:A. Sichere Befestigung:
Stellen Sie sicher, dass das Werkstück ist sicher eingespannt oder befestigt werden, um unbeabsichtigte Bewegungen oder Vibrationen zu verhindern. Die richtige Befestigung ist entscheidend für die Aufrechterhaltung der Stabilität während der Bearbeitung.B. Materialauswahl:
Wähle die entsprechendes Material für Ihr Werkstück basierend auf den spezifischen Bearbeitungsanforderungen. Die Eigenschaften des Materials wie Härte und Wärmeleitfähigkeit können sich auf das Rattern auswirken. Die Auswahl des richtigen Materials kann stabile Schnittbedingungen fördern.C. Überhang minimieren:
Lange Überhänge zwischen Werkstück und Werkzeug können aufgrund der stärkeren Werkzeugauslenkung das Rattern verstärken. Eine Reduzierung des Überhangs oder die Verwendung kürzerer Werkzeuge kann helfen, diesen Effekt abzumildern.3. Werkzeugauswahl und Wartung
Die Wahl der Schneidwerkzeuge und deren Zustand haben einen erheblichen Einfluss auf das Rattern. Zu den zu berücksichtigenden werkzeugbezogenen Faktoren gehören:A. Werkzeugmaterial:
Wähle aus optimales Werkzeugmaterial abhängig vom Werkstückmaterial. Verschiedene Materialien bieten unterschiedliche Grade an Verschleißfestigkeit und Hitzebeständigkeit. Die Wahl des richtigen Werkzeugmaterials kann den Werkzeugverschleiß und die Wahrscheinlichkeit von Rattern verringern.B. Werkzeuggeometrie:
Betrachten Sie die Werkzeuggeometrie, einschließlich der Anzahl der Spannuten, des Spanwinkels und des Spiralwinkels. Geeignete Werkzeuggeometrien, die eine gute Spankontrolle bieten und die Schnittkräfte reduzieren, sind für ratteranfällige Materialien vorzuziehen.C. Regelmäßige Werkzeugwartung:
Stellen Sie sicher, dass Schneidwerkzeuge vorhanden sind guter Zustand durch regelmäßige Inspektionen und Wartungen. Abgenutzte oder beschädigte Werkzeuge verursachen eher Rattern. Zur ordnungsgemäßen Werkzeugwartung gehören das Schärfen, die Aufbereitung und der Werkzeugwechsel bei Bedarf.4. Optimale Schnittparameter
Um Rattern zu verhindern, ist die Auswahl der richtigen Schnittparameter von entscheidender Bedeutung. Zu den schneidparameterbezogenen Faktoren gehören:A. Vorschubgeschwindigkeit:
Wähle ein entsprechende Vorschubgeschwindigkeit das mit anderen Schnittparametern abgestimmt ist. Eine zu hohe Vorschubgeschwindigkeit kann zu erhöhten Schnittkräften und Rattern führen. Passen Sie die Vorschubgeschwindigkeit an, um eine stabile Bearbeitung zu gewährleisten.B. Schneidgeschwindigkeit:
Das Schneidgeschwindigkeit müssen je nach verwendetem Material und Werkzeug richtig ausgewählt werden. Eine falsche Schnittgeschwindigkeit kann zu Rattern führen. Die richtige Schnittgeschwindigkeit hängt von Faktoren wie Materialart, Werkzeugmaterial und Werkzeuggeometrie ab.C. Schnitttiefe:
Das Schnitttiefe wirkt sich auf die Spanlast und die Werkzeugkräfte aus. Ein tiefer Schnitt kann das Werkzeug überlasten und zu Vibrationen und Rattern führen. Eine Verringerung der Schnitttiefe kann dazu beitragen, Rattern zu vermeiden, insbesondere bei der Arbeit mit anspruchsvollen Materialien.5. Werkzeugwegoptimierung
Durch die Optimierung des Werkzeugwegs kann das Rattern minimiert werden, indem plötzliche Änderungen der Schnittkräfte vermieden werden. Betrachten Sie die folgenden Ansätze:A. Trochoides Fräsen:
Trochoides Fräsen ist eine Technik, die Folgendes erfordert kontrollierte, kontinuierliche Werkzeugwegmuster das kann das Rattern reduzieren. Dabei folgt das Werkzeug einem kreisförmigen oder gekrümmten Pfad, anstatt gerade Schnitte auszuführen.B. Gleichlauf vs. konventionelles Fräsen:
Wählen zwischen Gleichlauffräsen (wobei sich der Fräser in Vorschubrichtung dreht) und konventionelles Fräsen (wo sich der Fräser entgegen der Vorschubrichtung dreht) kann sich auf das Rattern auswirken. Beim Gleichlauffräsen kommt es oft zu weniger Rattern, da es die Auswirkungen der Schnittkräfte reduziert.6. Dämpfungstechniken
Um Vibrationen während der Bearbeitung entgegenzuwirken, können verschiedene Dämpfungstechniken eingesetzt werden:a. Werkzeugdämpfer:
Werkzeugdämpfer sind Anbauteile, die am Werkzeughalter angebracht werden können, um Vibrationen und Rattern zu reduzieren. Diese Dämpfer absorbieren Vibrationen und verbessern die Stabilität des Bearbeitungsprozesses.b. Ratterbeständige Werkzeughalter:
Erwägen Sie die Verwendung von Werkzeughaltern, die speziell zur Reduzierung von Rattern entwickelt wurden. Diese Werkzeughalter verfügen über fortschrittliche Dämpfungstechnologien, um die Bearbeitungsstabilität zu verbessern.c. Bearbeitung ratterbeständiger Wendeschneidplatten:
Das Schneidwerkzeug kann mit ratterfesten Wendeschneidplatten ausgestattet werden. Diese Einsätze sollen Vibrationen dämpfen und die Werkzeugstabilität verbessern.7. Überwachungs- und Kontrollsysteme
Um Chatter effektiv zu verwalten, sollten Sie den Einsatz von Überwachungs- und Kontrollsystemen in Betracht ziehen:a. Schwingungsüberwachungssysteme:
Installieren Schwingungsüberwachungssysteme auf der CNC-Maschine, um Rattern in Echtzeit zu erkennen. Diese Systeme können Schnittparameter oder Werkzeugwege automatisch anpassen, um auftretende Vibrationen zu reduzieren.b. Adaptive Steuerungssysteme:
Adaptive Steuerungssysteme nutzen Echtzeitdaten, um Schnittparameter und Werkzeugwege dynamisch anzupassen und so Rattern zu vermeiden. Diese Systeme können bei der Ratterreduzierung äußerst effektiv sein.c. Schnittkraftmessung:
Messen und Überwachen Schnittkräfte während der Bearbeitung können wertvolle Daten zur Vermeidung von Rattern liefern. Durch das Verständnis der wirkenden Kräfte können Anpassungen vorgenommen werden, um Vibrationen zu minimieren. Durch die Implementierung dieser Strategien und Techniken können Rattern beim CNC-Fräsen erheblich reduziert oder beseitigt werden, was zu einer verbesserten Teilequalität, längeren Werkzeuglebensdauer, Maschinenzuverlässigkeit und erhöhter Produktivität führt. Darüber hinaus können diese Ansätze an Ihre spezifischen Bedürfnisse angepasst werden CNC-Bearbeitung Betrieb und macht die Vibrationsreduzierung zu einem praktischen und erreichbaren Ziel.Fazit
Rattern beim CNC-Fräsen ist ein kritisches Problem, das die Qualität, Effizienz und Kosteneffizienz von Bearbeitungsvorgängen erheblich beeinträchtigen kann. Das Verständnis der Ursachen für Rattern, einschließlich Werkzeugmaschinenfaktoren, werkstückbezogener Probleme, Werkzeugfaktoren und Überlegungen zu Schnittparametern, ist für die wirksame Bewältigung dieser Herausforderung von entscheidender Bedeutung. Um Rattern zu reduzieren oder zu beseitigen, können Maschinisten eine breite Palette von Strategien und Techniken anwenden:- Verbesserungen an Werkzeugmaschinen: Durch die Aufrüstung auf steifere Maschinen, den Einsatz von Dämpfungssystemen und die Sicherstellung einer regelmäßigen Wartung kann die Maschinenstabilität verbessert und Vibrationen reduziert werden.
- Werkstückvorbereitung: Die richtige Befestigung, Materialauswahl und die Minimierung des Überhangs tragen zur Stabilität des Werkstücks und zur Reduzierung von Rattern bei.
- Werkzeugauswahl und -wartung: Durch die Wahl der richtigen Werkzeugmaterialien und -geometrien sowie durch die Aufrechterhaltung eines guten Zustands der Werkzeuge können Vibrationen minimiert werden.
- Optimale Schnittparameter: Die Anpassung von Vorschubgeschwindigkeiten, Schnittgeschwindigkeiten und Schnitttiefen zur Aufrechterhaltung ausgewogener Schnittkräfte ist für die Ratterreduzierung von entscheidender Bedeutung.
- Werkzeugwegoptimierung: Der Einsatz von Wirbelfräsen und die Wahl der geeigneten Fräsrichtung (Gleichlauf oder konventionell) können zur Vermeidung von Rattern beitragen.
- Dämpfungstechniken: Durch den Einsatz von Werkzeugdämpfern, vibrationsfesten Werkzeughaltern und Bearbeitungseinsätzen zur Vibrationsdämpfung kann das Rattern gemindert werden.
- Überwachungs- und Kontrollsysteme: Mithilfe von Vibrationsüberwachungssystemen, adaptiven Steuerungssystemen und Schnittkraftmessungen können Vibrationen in Echtzeit erkannt und behoben werden.
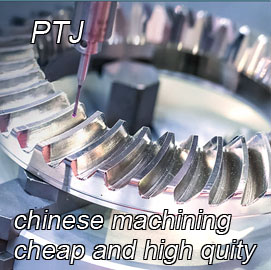
Unsere Leistungen
- 5-Achsen-Bearbeitung
- CNC-Fräsen
- CNC drehen
- Bearbeitungsindustrie
- Bearbeitungsprozess
- Oberflächenbearbeitung
- Metallbearbeitung
- Kunststoffbearbeitung
- Pulvermetallurgie-Form
- Druckguss
- Teile Galerie
Fallstudien
- Autoteile aus Metall
- Maschinenteile
- LED-Kühlkörper
- Gebäudeteile
- Mobilteile
- Medizinische Teile
- Electronic Parts
- Maßgeschneiderte Bearbeitung
- Fahrradteile
Material Liste
- Aluminiumbearbeitung
- Titanbearbeitung
- Edelstahlbearbeitung
- Kupferbearbeitung
- Messingbearbeitung
- Bearbeitung von Superlegierungen
- Peek-Bearbeitung
- UHMW-Bearbeitung
- Einzelbearbeitung
- PA6-Bearbeitung
- PPS-Bearbeitung
- Teflon-Bearbeitung
- Inconel-Bearbeitung
- Werkzeugstahlbearbeitung
- Mehr Material
Teile Galerie