Die Entwicklung und der Trend der Vakuum-Induktions-Schmelztechnologie
Mit der rasanten Entwicklung der modernen Industrietechnologie werden die Anforderungen der Menschen an die Verwendung mechanischer Teile immer höher, und die härtere Nutzungsumgebung stellt höhere Anforderungen an die hohe Temperaturbeständigkeit, Verschleißfestigkeit, Ermüdungsbeständigkeit und andere Eigenschaften von Metallwerkstoffen .
Für einige spezifische Metalle oder Legierungsmaterialien, sei es bei F&E-Tests in einem frühen Stadium oder bei der Massenproduktion in einem späteren Stadium und deren Einsatz, die Erforschung oder Beschaffung von Hochleistungsmetalllegierungsmaterialien erfordert die Unterstützung von Metallschmelzanlagen, Oberflächenwärmebehandlungsanlagen usw. Unter Bei den vielen speziellen Erwärmungs- oder Schmelzverfahren wird die Induktionserwärmungstechnik zum Schmelzen und Aufbereiten von Metallwerkstoffen oder zum Sintern und Wärmebehandeln von Werkstoffen in einem bestimmten Verfahren eingesetzt, was eine entscheidende Rolle gespielt hat.
Dieser Artikel stellt den Entwicklungsprozess der Vakuuminduktionsschmelztechnologie und die Anwendung der Induktionsschmelztechnologie bei verschiedenen Gelegenheiten vor. Vergleichen Sie je nach Aufbau der verschiedenen Vakuum-Induktionsofentypen deren Vor- und Nachteile. Mit Blick auf die zukünftige Entwicklungsrichtung von Vakuuminduktionsöfen, erläutert deren Entwicklungstrend. Die Entwicklung und der Fortschritt der Vakuum-Induktionsöfen spiegeln sich vor allem in der sukzessiven Verbesserung der Gesamtstruktur der Anlagen, dem immer deutlicher werdenden Trend zur Modularisierung und der intelligenteren Steuerung wider.
1. Vakuum-Induktions-Schmelztechnologie
1.1 Prinzip
__kindeditor_temp_url__Induktionserwärmungstechnologie bezieht sich normalerweise auf eine Technologie, die das Prinzip der elektromagnetischen Induktion verwendet, um einen Induktionsstrom für Materialien mit besserer magnetischer Empfindlichkeit zu erhalten, um den Zweck der Erwärmung unter Vakuumbedingungen zu erreichen. Der elektrische Strom fließt mit einer bestimmten Frequenz durch die elektromagnetische Spule, die das Metallmaterial umgibt. Der sich ändernde elektrische Strom erzeugt ein induziertes Magnetfeld, das einen induzierten Strom im Metall verursacht und eine große Wärmemenge erzeugt, um das Material zu erhitzen. Wenn die Wärme relativ gering ist, kann sie bei der Vakuuminduktionswärmebehandlung und anderen Prozessen verwendet werden. Wenn die Hitze hoch ist, reicht die erzeugte Hitze aus, um das Metall zu schmelzen und zur Herstellung von Metall- oder Legierungsmaterialien verwendet zu werden.
1.2, Anwendung
1.2.1, Vakuuminduktionsschmelzen
Die Vakuum-Induktions-Schmelztechnologie ist derzeit die effizienteste, schnellste, verbrauchsärmste, energiesparende und umweltfreundlichste Induktionserwärmungstechnologie zum Erwärmen von metallischen Materialien. Diese Technologie wird hauptsächlich in Induktionsschmelzöfen und anderen Geräten eingesetzt und hat ein breites Anwendungsspektrum. Die massiven Metallrohstoffe werden in einen Tiegel gelegt, der von einer Spule umwickelt ist. Wenn der Strom durch die Induktionsspule fließt, wird eine induzierte elektromotorische Kraft erzeugt und ein Wirbelstrom wird innerhalb der Metallladung erzeugt. Wenn die aktuelle Wärme größer ist als die Wärmeabfuhrrate der Metallcharge, sammelt sich die Wärme immer mehr an. Bei Erreichen eines bestimmten Niveaus schmilzt das Metall von einem festen in einen flüssigen Zustand, um den Zweck des Schmelzens von Metallen zu erfüllen. Da bei diesem Verfahren der gesamte Vorgang in einer Vakuumumgebung stattfindet, ist es vorteilhaft, die Gasverunreinigungen im Inneren des Metalls zu entfernen, und das erhaltene Metalllegierungsmaterial ist reiner. Gleichzeitig kann während des Schmelzprozesses durch die Steuerung der Vakuumumgebung und Induktionserwärmung die Schmelztemperatur eingestellt und das Legierungsmetall rechtzeitig ergänzt werden, um den Raffinationszweck zu erreichen. Während des Schmelzprozesses kann aufgrund der Eigenschaften der Induktionsschmelztechnologie das flüssige Metallmaterial im Inneren des Tiegels aufgrund der Wechselwirkung elektromagnetischer Kräfte automatisch gerührt werden, um die Zusammensetzung zu vereinheitlichen. Dies ist auch ein großer Vorteil der Induktionsschmelztechnologie.
Im Vergleich zum traditionellen Schmelzen hat das Vakuuminduktionsschmelzen große Vorteile aufgrund der Energieeinsparung, des Umweltschutzes, des guten Arbeitsumfelds für die Arbeiter und der geringen Arbeitsintensität. Durch die Induktionsschmelztechnologie weist das endgültige Legierungsmaterial weniger Verunreinigungen auf und der Anteil der hinzugefügten Legierung ist besser geeignet, wodurch die Anforderungen des Prozesses an die Eigenschaften des Materials besser erfüllt werden können.
Die Vakuuminduktionsschmelztechnologie wurde in großem Maßstab eingesetzt, von Induktionsöfen von mehreren Kilogramm für experimentelle Forschung bis hin zu großen Induktionsöfen mit einer Kapazität von mehreren zehn Tonnen für die eigentliche Produktion. Aufgrund seiner einfachen Bedientechnologie ist der Schmelzprozess leicht zu kontrollieren und die Schmelztemperatur ist schnell. Das geschmolzene Metall hat die Vorteile einer einheitlichen Zusammensetzung und hat große Anwendungsaussichten und wurde in den letzten Jahren schnell entwickelt.
1.2.2, Vakuuminduktionssintern
Vakuumsintern bezieht sich auf das Sintern von Metall-, Legierungs- oder Metallverbindungspulver zu Metallprodukten und Metallrohlingen bei einer Temperatur unterhalb des Schmelzpunktes in einer Umgebung mit einem Vakuumgrad von (10-10-3Pa). Beim Sintern unter Vakuumbedingungen gibt es keine Reaktion zwischen Metall und Gas und keinen Einfluss von adsorbiertem Gas. Der Verdichtungseffekt ist nicht nur gut, sondern kann auch eine Rolle bei der Reinigung und Reduzierung spielen, die Sintertemperatur senken, und das Sinterverhältnis bei Raumtemperatur kann um 100℃~150℃ reduziert werden Lebensdauer des Sinterofens und erhalten hochwertige Produkte.
Bei einigen Materialien ist es notwendig, die Bindung zwischen den Partikeln durch die Übertragung von Atomen durch Erhitzen zu realisieren, und die Induktionssintertechnologie spielt dabei eine Rolle beim Erhitzen. Der Vorteil des Vakuuminduktionssinterns besteht darin, dass es hilft, Schadstoffe (Wasserdampf, Sauerstoff, Stickstoff und andere Verunreinigungen) in der Atmosphäre unter Vakuumbedingungen zu reduzieren und eine Reihe von Reaktionen wie Entkohlung, Nitrierung, Aufkohlung, Reduktion und Oxidation zu vermeiden . Dabei wird die Gasmenge in den Poren reduziert und die chemische Reaktion von Gasmolekülen reduziert. Gleichzeitig wird der Oxidfilm auf der Oberfläche des Materials entfernt, bevor das Material in der flüssigen Phase erscheint, so dass das Material beim Schmelzen und Verbinden des Materials dichter verbunden wird und seine Verschleißfestigkeit verbessert wird. Stärke. Darüber hinaus hat das Vakuuminduktionssintern auch einen gewissen Einfluss auf die Reduzierung der Produktkosten.
Da der Gasgehalt in einer Vakuumumgebung relativ gering ist, können Konvektion und Wärmeleitung vernachlässigt werden. Die Wärme wird hauptsächlich in Form von Strahlung vom Heizelement auf die Materialoberfläche übertragen. Die Auswahl richtet sich nach der spezifischen Sintertemperatur und den physikalischen und chemischen Eigenschaften des Materials. Auch die passenden Heizungskomponenten sind sehr wichtig. Im Vergleich zur Vakuum-Widerstandserwärmung verwendet das Induktionssintern eine Zwischenfrequenz-Leistungserwärmung, die das Hochtemperatur-Isolationsproblem von Vakuumöfen vermeidet, die bis zu einem gewissen Grad eine Widerstandserwärmung verwenden.
Derzeit wird die Induktionssintertechnologie hauptsächlich in den Bereichen Stahl und Metallurgie eingesetzt. Darüber hinaus verbessert das Induktionssintern bei speziellen Keramikmaterialien die Bindung fester Partikel, fördert das Wachstum von Kristallkörnern, komprimiert Hohlräume und erhöht dann die Dichte, um dichte polykristalline Sinterkörper zu bilden. Auch bei der Erforschung neuer Materialien wird die Induktionssintertechnologie immer häufiger eingesetzt.
1.2.3, Vakuum-Induktionswärmebehandlung
Gegenwärtig sollte es mehr Technologien zur Induktionswärmebehandlung geben, die sich hauptsächlich auf die Induktionshärtetechnologie konzentrieren. Legen Sie das Werkstück in den Induktor (Spule), wenn ein Wechselstrom einer bestimmten Frequenz durch den Induktor geleitet wird, wird um ihn herum ein magnetisches Wechselfeld erzeugt. Die elektromagnetische Induktion des magnetischen Wechselfeldes erzeugt im Werkstück einen geschlossenen Wirbelstrom. Aufgrund des Skin-Effekts, dh die Verteilung des induzierten Stroms auf dem Querschnitt des Werkstücks ist sehr ungleichmäßig, die Stromdichte an der Oberfläche des Werkstücks ist sehr hoch und nimmt nach innen allmählich ab.
Die elektrische Energie des hochdichten Stroms an der Oberfläche des Werkstücks wird in Wärmeenergie umgewandelt, die die Temperatur der Oberfläche erhöht, dh eine Oberflächenerwärmung realisiert. Je höher die Stromfrequenz, desto größer der Stromdichteunterschied zwischen der Oberfläche und dem Inneren des Werkstücks und desto dünner die Heizschicht. Nachdem die Temperatur der Heizschicht die kritische Temperatur des Stahls überschritten hat, wird sie schnell abgekühlt, um eine Oberflächenabschreckung zu erreichen. Aus dem Prinzip der Induktionserwärmung ist bekannt, dass die Eindringtiefe des Stroms durch Einstellen der Frequenz des Stroms durch die Induktionsspule entsprechend verändert werden kann. Auch die einstellbare Tiefe ist ein großer Vorteil der Induktionswärmebehandlung. Für komplizierte mechanische Werkstücke ist die Induktionshärtetechnik jedoch aufgrund ihrer geringen Anpassungsfähigkeit nicht geeignet. Obwohl die Randschicht des abgeschreckten Werkstücks eine größere Druckeigenspannung aufweist, ist die Ermüdungsbruchfestigkeit höher. Es ist aber nur für die Fließbandfertigung einfacher Werkstücke geeignet.
Gegenwärtig wird die Induktionshärtungstechnologie hauptsächlich beim Oberflächenabschrecken von Kurbeln verwendetWelles und camWelles in der Automobilindustrie. Obwohl diese Teile eine einfache Struktur haben, aber die Arbeitsumgebung rau ist, haben sie ein gewisses Maß an Verschleißfestigkeit, Biegefestigkeit und Beständigkeit gegenüber der Leistung der Teile. Ermüdungsanforderungen durch Induktionshärten zur Verbesserung der Verschleißfestigkeit und Ermüdungsbeständigkeit ist auch die vernünftigste Methode, um die Leistungsanforderungen zu erfüllen. Es ist weit verbreitet in der Oberflächenbehandlung einiger Teile in der Automobilindustrie.
2. Vakuuminduktionsschmelzanlage
Vakuum-Induktions-Schmelzanlagen verwenden die Induktions-Schmelztechnologie, um das Prinzip im tatsächlichen Gebrauch durch die Anpassung der mechanischen Struktur zu verwirklichen. Das Gerät verwendet normalerweise das Prinzip der elektromagnetischen Induktion, um die Induktionsspule und das Material in einen geschlossenen Hohlraum zu bringen, das Gas im Behälter durch ein Vakuumpumpsystem zu extrahieren und dann die Stromversorgung zu verwenden, um den Strom durch die Induktionsspule zu leiten erzeugen eine induzierte elektromotorische Kraft und befinden sich im Material Ein Wirbel wird gebildet, und wenn die Wärmeentwicklung ein bestimmtes Niveau erreicht, beginnt das Material zu schmelzen. Während des Schmelzprozesses werden eine Reihe von Vorgängen wie Leistungsregelung, Temperaturmessung, Vakuummessung und Nachspeisung durch andere tragende Komponenten an der Anlage realisiert, und schließlich wird das flüssige Metall durch die Tiegelumkehrung in die Form gegossen, um a Metallbarren. Stint. Die Hauptstruktur der Vakuum-Induktions-Schmelzanlage umfasst die folgenden Teile:
Zusätzlich zu den oben genannten Komponenten sollte der Vakuumschmelzofen auch mit einer Stromversorgung, einem Steuerungssystem und einem Kühlsystem ausgestattet sein, um die Energiezufuhr für die Ausrüstung zum Schmelzen des Materials bereitzustellen und eine gewisse Kühlung in Schlüsselteilen bereitzustellen um eine Überhitzung des Systems zu verhindern, die zu einer Verringerung der Lebensdauer oder zu Schäden führt. Für Induktionsschmelzanlagen mit besonderen Prozessanforderungen gibt es entsprechende Hilfskomponenten wie Transportwagen, Ofentüröffnung und -schließung, Schleudergusspfanne, Sichtfenster usw. Bei Anlagen mit stärkeren Verunreinigungen sollte sie zusätzlich mit einem Gasfilter ausgestattet sein System usw. . Es ist ersichtlich, dass zusätzlich zu den notwendigen Komponenten ein kompletter Satz von Induktionsschmelzanlagen auch verschiedene Funktionen durch Hinzufügen anderer Komponenten gemäß spezifischer Prozessanforderungen realisieren kann und bequeme Bedingungen und Implementierungsmethoden für die Metallaufbereitung bietet.
2.1. Vakuum-Induktions-Schmelzofen
Der Vakuuminduktionsschmelzofen ist eine Schmelzausrüstung, die zuerst Metall durch Induktionserwärmung unter Vakuum schmilzt und dann flüssiges Metall in eine Form gießt, um einen Metallbarren zu erhalten. Die Entwicklung von Vakuum-Induktionsöfen begann um 1920 und wurde hauptsächlich zum Schmelzen von Nickel-Chrom-Legierungen verwendet. Bis der Zweite Weltkrieg die Weiterentwicklung der Vakuumtechnologie förderte, wurde der Vakuum-Induktions-Schmelzofen wirklich entwickelt. Während dieser Zeit entwickelten sich die Vakuuminduktionsschmelzöfen aufgrund der Nachfrage nach Legierungsmaterialien weiter zu großen Induktionsöfen, von anfänglich mehreren Tonnen bis zu Dutzenden von Tonnen ultragroßer Induktionsöfen. Zur Anpassung an die Massenproduktion hat sich neben der veränderten Anlagenkapazität auch der Aufbau des Induktionsofens von einem Taktofen mit Takt als Einheit zu einem kontinuierlichen oder halbkontinuierlichen Vakuum-Induktionsschmelzen zum Chargieren weiterentwickelt Vorbereitung, Schmelzen und Gießen. Der kontinuierliche Betrieb ohne Ofenstopp spart die Chargierzeit und die Wartezeit auf das Abkühlen des Barrens. Die kontinuierliche Produktion erhöht die Effizienz und erhöht auch den Legierungsausstoß. Erfüllen Sie besser die Anforderungen der tatsächlichen Produktion. Im Vergleich zum Ausland haben die frühen Vakuum-Induktionsöfen in meinem Land eine relativ geringe Kapazität, hauptsächlich unter 2 Tonnen. Große Schmelzöfen sind noch immer auf Importe aus dem Ausland angewiesen. Mit der Entwicklung der letzten Jahrzehnte kann mein Land auch selbst großflächige Vakuuminduktionsschmelzen entwickeln. Ofen erreicht die maximale Schmelze mehr als zehn Tonnen. Der früher entwickelte VIM-Vakuuminduktionsschmelzofen mit einfacher Struktur, bequemer Verwendung und geringen Wartungskosten ist in der tatsächlichen Produktion weit verbreitet.
Die Grundform eines Vakuum-Induktions-Schmelzofens. Über einen drehbaren Revolver werden dem Schmelztiegel metallische Materialien zugeführt. Die andere Seite ist auf den Tiegel ausgerichtet und die Temperaturmessung erfolgt durch Einführen des Thermoelements nach unten in die Metallschmelze. Das geschmolzene Metall wird durch den Drehmechanismus angetrieben und in die Form gegossen, um das Schmelzen des Metalls zu realisieren. Der gesamte Vorgang ist einfach und bequem zu bedienen. Für jede Verhüttung sind ein oder zwei Arbeiter erforderlich. Während des Schmelzprozesses kann eine Echtzeit-Temperaturüberwachung und Anpassung der Materialzusammensetzung erreicht werden, und das endgültige Metallmaterial entspricht mehr den Prozessanforderungen.
2.2. Vakuum-Induktions-Membran-Gasofen
Bei bestimmten Materialien ist es nicht erforderlich, dabei das Gießen in einer Vakuumkammer abzuschließen, sondern nur die Wärmekonservierung und das Entgasen in einer Vakuumumgebung. Auf Basis des VIM-Ofens wird sukzessive der Vakuum-Induktions-Membran-Gasofen des VID-Entgasungsofens weiterentwickelt.
Das Hauptmerkmal des Vakuum-Induktions-Entgasungsofens ist die kompakte Struktur und das kleine Ofenvolumen. Ein kleineres Volumen ist für eine schnelle Gasextraktion und ein besseres Vakuum förderlicher. Im Vergleich zu herkömmlichen Entgasungsöfen hat die Anlage ein relativ kleines Volumen, einen geringen Temperaturverlust, eine bessere Flexibilität und Wirtschaftlichkeit und ist für flüssige oder feste Beschickung geeignet. Der VID-Ofen kann zum Schmelzen und Entgasen von Edelstahl und NE-Metallen verwendet werden und muss unter den Bedingungen einer atmosphärischen Umgebung oder einer Schutzatmosphäre in die Form gegossen werden. Der gesamte Schmelzprozess kann die Entfernung von Verunreinigungen wie Entkohlung und Raffination von Materialien, Dehydrierung, Desoxidation und Entschwefelung realisieren, was einer präzisen Anpassung der chemischen Zusammensetzung an die Prozessanforderungen förderlich ist.
Unter einer bestimmten Vakuumbedingung oder Schutzatmosphäre wird das Metallmaterial durch die Beheizung des Induktions-Entgasungsofens nach und nach aufgeschmolzen und das innere Gas kann dabei entfernt werden. Wenn dem Verfahren ein geeignetes Reaktionsgas zugesetzt wird, verbindet es sich mit dem Kohlenstoffelement im Inneren des Metalls, um gasförmige Karbide zu erzeugen, die aus dem Ofen entfernt werden, wodurch der Zweck der Entkohlung und Raffination erreicht wird. Beim Gießprozess muss eine gewisse Schutzatmosphäre eingeführt werden, um sicherzustellen, dass das entgaste Metallmaterial vom Gas in der Atmosphäre isoliert wird und schließlich die Entgasung und Veredelung des Metallmaterials abgeschlossen ist.
2.3. Vakuum-Induktions-Entgasungs-Gießofen
Der Vakuum-Induktions-Entgasungs-Gießofen wurde auf Basis der ersten beiden Schmelztechnologien entwickelt. 1988 fertigte Leybold-Heraeus, der Vorgänger der deutschen Firma ALD, den ersten VIDP-Ofen. Das technische Herzstück dieses Ofentyps ist eine kompakte Vakuumschmelzkammer, die in den Induktionsspulentiegel integriert ist. Es ist nur wenig größer als die Induktionsspule und enthält nur die Induktionsspule und den Tiegel. Kabel, Wasserkühlleitungen und hydraulische Wendeeinrichtungen sind alle außerhalb der Schmelzkammer installiert. Der Vorteil besteht darin, Kabel und wassergekühlte Rohrleitungen vor Schäden durch Spritzer geschmolzenen Stahls und periodische Temperatur- und Druckänderungen zu schützen. Aufgrund der bequemen Demontage und des leichteren Austauschens des Tiegels ist der VIDP-Ofenmantel mit drei Ofenkörpern ausgestattet. Eine Vorbereitung des Tiegelofens verkürzt den Produktionszyklus und verbessert die Produktionseffizienz.
Der Ofendeckel wird vakuumdicht auf dem Ofenrahmen und zwei Hydraulikzylindersäulen getragen LagerS. Beim Gießen decken zwei Hydraulikzylinder den Ofendeckel seitlich ab, und der Ofendeckel treibt die Schmelzkammer zum Kippen um das Vakuum Lager. Im geneigten Gießzustand findet keine Relativbewegung zwischen der Schmelzkammer und dem Induktionsspulentiegel statt. Der Läufer ist ein wichtiger Bestandteil des VIDP-Ofens. Da die Konstruktion des VIDP-Ofens die Schmelzkammer von der Barrenkammer isoliert, muss der geschmolzene Stahl durch den Vakuumkanal in die Barrenkammer gelangen. Die Barrenkammer ist mit einer quadratischen Schrägseite offen und geschlossen. Es besteht aus zwei Teilen. Der feststehende Teil befindet sich neben der Angusskammer, und der bewegliche Teil bewegt sich horizontal entlang der Bodenschiene, um das Öffnen und Schließen der Barrenkammer abzuschließen. Bei einigen Geräten ist der bewegliche Teil auf 30 Grad ausgelegt, nach links und rechts nach oben geöffnet, was zum Be- und Entladen von Kokillen und zur täglichen Wartung und Reparatur von Kränen praktisch ist. Zu Beginn des Schmelzvorgangs wird der Ofenkörper durch den darunter liegenden hydraulischen Mechanismus angehoben, mit dem oberen Ofendeckel des Ofens verbunden und mit einem speziellen Mechanismus verriegelt. Das obere Ende des Ofendeckels ist über ein Vakuum mit der Beschickungskammer verbunden Ventil.
Da nur der Schmelzteil in der Vakuumkammer eingeschlossen ist und durch die Umlenkrille ausgegossen wird, ist der Ofenaufbau kompakt, die Schmelzkammer kleiner und das Vakuum kann besser und schneller kontrolliert werden. Im Vergleich zum traditionellen Induktionsschmelzofen zeichnet er sich durch eine kurze Evakuierungszeit und eine geringe Leckrate aus. Die optimale Druckregelung lässt sich durch die Ausstattung der PLC-Logic-Steuerung erreichen. Gleichzeitig kann das elektromagnetische Rührsystem das Schmelzbad stabil rühren, und die hinzugefügten Elemente werden gleichmäßig von oben nach unten im Schmelzbad aufgelöst, wodurch die Temperatur nahezu konstant gehalten wird. Beim Ausgießen von Geld wird der Ausguss durch das externe Heizsystem erhitzt, um die anfängliche Blockierung des Ausgussanschlusses und die thermische Rissbildung des Ausgusses zu reduzieren. Durch Hinzufügen von Filterleitblechen und anderen Maßnahmen kann es die Auswirkungen von geschmolzenem Stahl mildern und die Metallreinheit verbessern. Aufgrund des geringen Volumens des VIDP-Ofens sind die Erkennung und Reparatur von Vakuumlecks einfacher und die Reinigungszeit im Ofen kürzer. Außerdem kann die Temperatur im Ofen mit einem kleinen, leicht austauschbaren Thermoelement gemessen werden.
2.4, wassergekühlter Induktionstiegel
Das elektromagnetische Induktions-Vakuumschwebe-Schmelzverfahren mit wassergekühltem Tiegel ist ein Schmelzverfahren, das sich in den letzten Jahren schnell entwickelt hat. Es wird hauptsächlich verwendet, um hochschmelzende, hochreine und extrem aktive metallische oder nichtmetallische Materialien herzustellen. Durch das Schneiden des Kupfertiegels in gleiche Teile der kupfernen Blütenblattstruktur und das Durchleiten von Wasserkühlung durch jeden Blütenblattblock erhöht diese Struktur den elektromagnetischen Schub, so dass das geschmolzene Metall in der Mitte zusammengedrückt wird, um einen Höcker zu bilden und sich von der Tiegelwand. Das Metall wird in ein elektromagnetisches Wechselfeld gebracht. Das Gerät konzentriert die Kapazität im Volumenraum des Tiegels und bildet dann einen starken Wirbelstrom an der Oberfläche der Charge. Einerseits gibt er Joulesche Wärme ab, um die Ladung zu schmelzen, und andererseits bildet er die Lorentz-Kraft zum Schmelzen. Der Körper schwebt und erzeugt starkes Rühren. Die zugesetzten Legierungselemente lassen sich schnell und gleichmäßig in der Schmelze vermischen, wodurch die chemische Zusammensetzung gleichmäßiger und die Temperaturführung ausgeglichener wird. Durch die Magnetschwebewirkung hat die Schmelze keinen Kontakt mit der Innenwand des Tiegels, was eine Verunreinigung der Schmelze durch den Tiegel verhindert. Gleichzeitig reduziert es die Wärmeleitung und verstärkt die Wärmeabstrahlung, wodurch die Wärmeableitung der Metallschmelze verringert und eine höhere Temperatur erreicht wird. Für die hinzugefügte Metallcharge kann es je nach gewünschter Zeit und eingestellter Temperatur geschmolzen und warm gehalten werden, und die Charge muss nicht vorher verarbeitet werden. Wassergekühltes Tiegelschmelzen kann hinsichtlich der Entfernung von Metalleinschlüssen und Entgasungsraffination das Niveau des Elektronenstrahlschmelzens erreichen, während der Verdampfungsverlust geringer und der Energieverbrauch geringer ist und die Produktionseffizienz verbessert wird. Aufgrund der berührungslosen Erwärmungseigenschaften der Induktionserwärmung ist der Einfluss auf die Schmelze geringer und es wirkt sich gut auf die Herstellung von hochreinen oder hochaktiven Metallen aus. Aufgrund des komplexen Aufbaus der Anlagen ist eine Magnetschwebebahn-Verhüttung für Großanlagen noch immer schwierig zu realisieren. In dieser Phase gibt es keine wassergekühlten Kupfertiegel-Schmelzanlagen mit großer Kapazität. Die derzeitige wassergekühlte Tiegelausrüstung wird nur für experimentelle Untersuchungen zum kleinvolumigen Metallschmelzen verwendet.
3. Der zukünftige Entwicklungstrend von Induktionsschmelzanlagen
Mit der Entwicklung der Vakuum-Induktionserwärmungstechnologie ändern sich die Ofentypen ständig, um unterschiedliche Funktionen zu erfüllen. Von einer einfachen Schmelz- oder Erhitzungsstruktur hat sie sich nach und nach zu einer komplexen Struktur entwickelt, die unterschiedliche Funktionen realisieren kann und produktionsförderlicher ist. Bei komplexeren technologischen Prozessen in der Zukunft ist es die Entwicklungsrichtung von Induktionsschmelzanlagen, wie man eine präzise Prozesssteuerung erreicht, relevante Informationen misst und extrahiert und die Arbeitskosten so weit wie möglich senkt.
3.1, modular
In einem kompletten Gerätesatz sind unterschiedliche Komponenten für unterschiedliche Nutzungsanforderungen ausgestattet. Jeder Teil der Komponente erfüllt seine eigene Funktion, um seinen eigenen Verwendungszweck zu erreichen. Bei bestimmten Ofentypen hilft das Hinzufügen bestimmter Module, um die Ausrüstung zu vervollständigen, beispielsweise die Ausstattung mit einem vollständigen Temperaturmesssystem, dabei, die Veränderungen der Materialien im Ofen mit der Temperatur zu beobachten und eine vernünftigere Kontrolle der Temperatur zu erreichen; ausgestattet mit einem Massenspektrometer zur Erfassung der Materialzusammensetzung Passen Sie den Zeitpunkt und die Reihenfolge der Zugabe von Legierungselementen an, um die Leistung der Legierung in der Entwicklungsphase des Prozesses zu verbessern; ausgestattet mit einer Elektronenkanone und einer Ionenkanone, um das Problem des Schmelzens einiger hochschmelzender Metalle usw. zu lösen. In der zukünftigen induktionsmetallurgischen Ausrüstung sind unterschiedliche Kombinationen verschiedener Module zur Erzielung unterschiedlicher Funktionen und zur Erfüllung unterschiedlicher Prozessanforderungen zu einem unvermeidlichen Entwicklungstrend geworden, und sie sind auch eine Kombination und Referenz verschiedener Bereiche. Um den Metallschmelzprozess zu verbessern und Materialien mit besserer Leistung zu erhalten, werden modulare Geräte eine stärkere Wettbewerbsfähigkeit auf dem Markt haben.
3.2. Intelligente Steuerung
Im Vergleich zum herkömmlichen Schmelzen haben Vakuuminduktionsanlagen einen großen Vorteil bei der Realisierung der Prozesskontrolle. Aufgrund der Entwicklung der Computertechnologie können die freundliche Bedienung der Mensch-Maschine-Schnittstelle, die intelligente Signalerfassung und die vernünftige Programmeinstellung in der Ausrüstung leicht den Zweck der Steuerung des Schmelzprozesses erreichen, die Arbeitskosten senken und die Bedienung vereinfachen und praktisch.
In der zukünftigen Entwicklung werden die Vakuumgeräte um intelligentere Steuerungssysteme erweitert. Für den etablierten Prozess wird es für die Menschen einfacher sein, die Schmelztemperatur durch das intelligente Steuersystem präzise zu steuern, Legierungsmaterialien zu einem bestimmten Zeitpunkt hinzuzufügen und eine Reihe von Aktionen zum Schmelzen, Wärmekonservieren und Gießen durchzuführen. Und all dies wird vom Computer kontrolliert und aufgezeichnet, um unnötige Verluste durch menschliche Fehler zu reduzieren. Für den sich wiederholenden Schmelzprozess kann eine bequemere und intelligentere moderne Steuerung realisiert werden.
3.3. Informatisierung
Induktionsschmelzanlagen erzeugen während des gesamten Schmelzvorgangs eine große Menge an Schmelzinformationen, die Echtzeit-Parameteränderungen der Stromversorgung der Induktionsheizung, das Temperaturfeld der Charge, des Tiegels, das von der Induktionsspule erzeugte elektromagnetische Feld, die physikalische Eigenschaften der Metallschmelze und so weiter. Gegenwärtig realisiert die Ausrüstung nur eine einfache Datensammlung, und der Analyseprozess wird ausgeführt, nachdem die Daten extrahiert wurden, nachdem das Schmelzen abgeschlossen ist. Die Entwicklung der Informatisierung, Datenerhebung und -verarbeitung sowie der Analyseprozess werden in Zukunft zwangsläufig nahezu synchron mit dem Schmelzprozess erfolgen. Vollständige Datensammlung für die intern erschmolzenen Materialien von metallurgischen Geräten, Computerverarbeitung der Daten, Echtzeitanzeige des internen Temperaturfelds und des elektromagnetischen Felds der Ausrüstung unter der aktuellen Situation und Signalübertragung durch Echtzeit-Feedback verschiedener Daten, bequem für Menschen Echtzeit-Beobachtung und -Einstellung des Schmelzprozesses verstärkte die menschliche Intervention und Kontrolle. Beim Schmelzprozess werden rechtzeitige Anpassungen vorgenommen, um den Prozess zu verbessern und die Legierungsleistung zu verbessern.
4 Fazit
Mit dem Fortschritt der Industrie hat sich die Vakuum-Induktions-Schmelztechnologie mit ihren einzigartigen Vorteilen in den letzten Jahrzehnten enorm weiterentwickelt und spielt eine wichtige Rolle im industriellen Bereich. Obwohl die Vakuuminduktionsschmelztechnologie meines Landes derzeit noch hinter dem Ausland zurückbleibt, bedarf es immer noch der unermüdlichen Bemühungen der einschlägigen Praktiker, die Marktwettbewerbsfähigkeit der speziellen Schmelzausrüstungen meines Landes zu verbessern und ihr Bestes zu geben, um die erstklassige Schmelzausrüstung der Welt zu werden . Vordergrund.
Link zu diesem Artikel: Die Entwicklung und der Trend der Vakuum-Induktions-Schmelztechnologie
Nachdruck-Erklärung: Sofern keine besonderen Hinweise vorliegen, sind alle Artikel auf dieser Seite Originale. Bitte geben Sie die Quelle für den Nachdruck an: https://www.cncmachiningptj.com
PTJ® ist ein kundenspezifischer Hersteller, der ein vollständiges Sortiment an Kupferschienen anbietet, Messingteile und Kupferteile. Zu den gängigen Herstellungsverfahren gehören Stanzen, Prägen, Kupferschmieden, Drahterodierdienste, Ätzen, Umformen und Biegen, Stauchen, Heiß Schmieden und Pressen, Perforieren und Stanzen, Gewinderollen und Rändeln, Scheren, Mehrspindelbearbeitung, Extrusion und Metallschmieden und Stempeln. Zu den Anwendungen gehören Sammelschienen, elektrische Leiter, Koaxialkabel, Wellenleiter, Transistorkomponenten, Mikrowellenröhren, blanke Formröhren und Pulvermetallurgie Extrusionsbehälter.
Erzählen Sie uns ein wenig über das Budget Ihres Projekts und die voraussichtliche Lieferzeit. Wir werden mit Ihnen Strategien entwickeln, um die kostengünstigsten Dienstleistungen zu erbringen, damit Sie Ihr Ziel erreichen. Sie können uns gerne direkt kontaktieren ( sales@pintejin.com ).
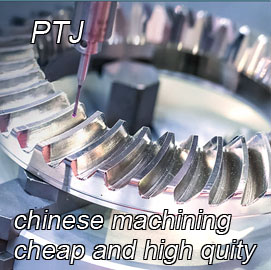
- 5-Achsen-Bearbeitung
- CNC-Fräsen
- CNC drehen
- Bearbeitungsindustrie
- Bearbeitungsprozess
- Oberflächenbearbeitung
- Metallbearbeitung
- Kunststoffbearbeitung
- Pulvermetallurgie-Form
- Druckguss
- Teile Galerie
- Autoteile aus Metall
- Maschinenteile
- LED-Kühlkörper
- Gebäudeteile
- Mobilteile
- Medizinische Teile
- Electronic Parts
- Maßgeschneiderte Bearbeitung
- Fahrradteile
- Aluminiumbearbeitung
- Titanbearbeitung
- Edelstahlbearbeitung
- Kupferbearbeitung
- Messingbearbeitung
- Bearbeitung von Superlegierungen
- Peek-Bearbeitung
- UHMW-Bearbeitung
- Einzelbearbeitung
- PA6-Bearbeitung
- PPS-Bearbeitung
- Teflon-Bearbeitung
- Inconel-Bearbeitung
- Werkzeugstahlbearbeitung
- Mehr Material