Analyse gängiger Qualitätsprobleme von Stahl und deren Ursachen
Die häufigsten Qualitätsprobleme von Stahl sind hauptsächlich: Oberflächenfehler, Innenfehler und Außenmaßfehler. Diese drei Probleme werden im Folgenden vorgestellt:
1. Oberflächenfehler
1. Oberflächenrisse:
bezieht sich auf die linearen Risse auf der Oberfläche des Stahls, die im Allgemeinen mit den Schmieden oder Rollrichtung.
Entstehungsursachen: hauptsächlich durch den bei der Verarbeitung (Schmieden, Walzen, Wärmebehandeln und Anlassen) entstehenden Haaransatz durch Oberflächenüberbrennen, Entkohlung, Lockerheit, Verformung, übermäßige Eigenspannung und hohe Oberflächenverunreinigungen mit Schwefel und Phosphor, Heißrisse und kalte Risse.
Prüfmethode: Oberflächenrisse können mit bloßem Auge, Beizen, Magnetpulverprüfung, Farbprüfung und Goldäquivalentverfahren geprüft werden. Beim Bestätigen von Rissen müssen Sie darauf achten, dass die Risse, die auf der Oberfläche des Stahls auftreten, spröde und locker sind, während der Stahl selbst keine Risse aufweist.
2. Schweres Leder und Falten:
die zungen- oder schuppigen metallplättchen, die auf der oberfläche des stahls aufgeklebt sind und sich an einigen flächen der oberfläche überlappen, weisen deutliche falten auf.
Entstehungsursachen: aufgrund von Graten, Graten, Vertiefungen, Einschlüssen, subkutanen Poren und Oberflächenlockerungen am Barren während der Warmumformung, der Metallrheologie bei der thermischen Verformung und der Öffnung bildet sich eine schwere Haut und Falten an der Oberfläche.
3. Ohren:
bezieht sich auf die Konkavitäten auf der Oberfläche des Stahls, die sich entlang der Walzrichtung erstrecken.
Ursache: Der Stichspalt des Walzwerks ist zu groß, wodurch sich die Oberfläche des Stahls entlang der Poren ausbeult.
4. Kratzer:
Auch Kratzer genannt, bezieht sich auf die gerade oder bogenförmige Rillenmarkierung auf der Oberfläche des Stahls unter Einwirkung von äußerer Kraft (sichtbar bis zum Boden der Rille).
2. Interne Mängel
1. Trennung:
Tatsächlich ist es ein allgemeiner Begriff für das Phänomen der ungleichmäßigen chemischen Zusammensetzung in Stahl. Bei der Säureauslaugungsprobe ist die Seigerung, wenn es sich um erodierbare Substanzen oder Gaseinschlüsse handelt, von dunkler Farbe, unregelmäßiger Form, leicht konkav, am Boden flach und es gibt viele dichte mikroporöse Flecken. Wenn die Korrosionsschutzelemente gesammelt werden, ist es blass, unregelmäßig geformt und hat relativ glatte Grübchen.
Je nach Lage und Form der Seigerung werden sie in der Regel in folgende Kategorien eingeteilt: ① Zentrale Seigerung: erscheinen im zentralen Teil und zeigen unregelmäßig geformte dunkle Flecken. ② Barrenseigerung: dunkle Flecken konzentriert auf einem geschlossenen Band mit unterschiedlichen Breiten und unterschiedlichen Breiten und mit der Querschnittsform des ursprünglichen Stahlbarrens (meist quadratisch), daher wird Barrenseigerung auch als Kastenseigerung bezeichnet. ③Punctate Segregation: Die Flecken sind im Allgemeinen größer, mit dunkleren, leicht eingesunkenen Mustern, ovalen oder Melonenkernen. Allgemein verteilt, sogenannte allgemeine Punktseigerung: Am Rand des Stahls verteilt, genannt Kanten-Punktseigerung.
Entstehungsursache: Seigerung ist die Ansammlung bestimmter Elemente durch selektive Kristallisation und Diffusion während des Gießens und Erstarrens des Stahlbarrens. Unter normalen Produktionsbedingungen ist eine Entmischung unvermeidbar.
2. Porosität:
Die Poren im Inneren des Stahls. Die Poren erscheinen im Allgemeinen als unregelmäßige Polygone auf Proben mit geringer Vergrößerung, und die scharfen und schmalen Vertiefungen am Boden erscheinen normalerweise in den Segregationspunkten. In schweren Fällen besteht die Tendenz, sich zu einer schwammigen Form zu verbinden. Entsprechend ihrer lockeren Verteilung können sie in zwei Kategorien eingeteilt werden: Zentrum lose und allgemein lose: ① Zentrum lose: Es gibt konzentrierte Hohlräume und dunkle Punkte in der Mitte der Probe mit niedriger Leistung. Am Längsriss befindet sich eine leichte Zwischenschicht, und unter dem Mikroskop ist die Zunahme von Perlit im losen Kern zu erkennen, was auf einen erhöhten Kohlenstoffgehalt im losen Kern hinweist. ②Im Allgemeinen locker: Die Struktur ist auf der Probe mit geringer Vergrößerung dicht und zeigt vereinzelte kleine Poren und kleine schwarze Flecken. Die Poren sind meist unregelmäßige Vielecke oder Muster, die bis auf die Kanten über den gesamten Querschnitt verteilt sind. Die Porosität in der Mitte tritt im Allgemeinen im Kopf und in der Mitte des Stahlblocks auf, und der Unterschied zur allgemeinen Porosität besteht darin, dass sie im Stahlabschnitt und in der Mitte statt im gesamten Abschnitt verteilt ist. Im Allgemeinen ist die Porosität im Zentrum umso schwerwiegender, je höher der Kohlenstoffgehalt ist.
Gründe für die Bildung: Während der Erstarrung des Stahlbarrens erstarrt das interkristalline niedrigschmelzende Material schließlich und schrumpft und gibt Gas unter Bildung von Hohlräumen ab, und das geschweißte Rohr wird während des Warmumformprozesses nicht ausgerüstet.
Bei Stahl sind leichte Seigerungen und höhere Porosität zulässig.
3. Einschlüsse:
Einschlüsse werden in metallische Einschlüsse und nichtmetallische Einschlüsse unterteilt. ①Metalleinschlüsse: Hauptsächlich Fehler durch Metallstangen, Bleche, Blöcke, die versehentlich in die Stahlkokille fallen, oder Ferrolegierungsblöcke, die am Ende des Schmelzvorgangs während des Gießprozesses hinzugefügt werden. Bei Proben mit geringer Vergrößerung sind die Kanten klar. Geometrische Formen mit Farben, die sich deutlich von der Umgebung unterscheiden. ②Nichtmetallische Einschlüsse: Während des Gießvorgangs bleibt keine Zeit zum Ausschwimmen der Schlacke oder des Feuerfestmaterials an der Ofenauskleidung und der Innenwand des Gießsystems, die sich in die Stahlschmelze abgeblättert hat. Die größeren nichtmetallischen Einschlüsse sind leicht zu erkennen, während die kleineren korrodieren. Nach dem Abziehen kleine runde Löcher hinterlassen.
4. Schrumpfhohlräume:
Bei Proben mit geringer Vergrößerung befinden sich die Schrumpfungshohlräume in der Mitte und die umgebenden Bereiche sind oft entmischt, gemischt oder locker und dicht. Manchmal sind Höhlen oder Spalten vor der Korrosion zu sehen. Nach der Korrosion sind die Hohlräume teilweise verdunkelt und zeigen unregelmäßige Falten.
Entstehungsursache: Beim Gießen des Stahlbarrens kann der endgültig erstarrte Teil (der Kernteil) der Stahlschmelze nach dem Erstarren und Schrumpfen nicht gefüllt werden. Die verbleibenden makroskopischen Hohlräume werden nicht gefüllt und der Schwindhohlraum wird hauptsächlich im Kopf des Stahlbarrens (dem Ende der Kappe) gebildet.
5. Luftblasen:
Bei Proben mit geringer Vergrößerung gibt es Risse, die ungefähr senkrecht zur Oberfläche stehen. Es gibt eine leichte Oxidation und Entkohlung in der Nähe. Die subkutanen Luftblasen werden als subkutane Luftblasen bezeichnet, und die tieferen subkutanen Luftblasen werden als Pinholes bezeichnet.
Entstehungsursachen: Defekte, die durch das beim Gießen des Stahlbarrens erzeugte und freigesetzte Gas verursacht werden.
6. Risse:
Bei geringer Vergrößerung reißt die axiale Position entlang der Interkristalle und bildet ein Spinnennetz, und in schweren Fällen reißt es radial.
Ursachen der Bildung: Es gibt hauptsächlich zwei Arten, eine ist das innere Reißen, das aus bestimmten Gründen beim Erstarren und Abkühlen des Barrens verursacht wird, und es wird während des Schmiede- und Walzprozesses nicht geschweißt; das andere sind interne Risse, die durch unsachgemäßes Schmieden verursacht werden.
7. Weiße Flecken:
dünne und kurze Risse bei Proben mit geringer Vergrößerung sind im Allgemeinen im Inneren des Stahls konzentriert und in der Oberflächenschicht mit einer Dicke von 20-30 mm fast nicht vorhanden. Da die Risse nicht leicht zu unterscheiden sind, sollten sie durch einen Bruchtest nachgewiesen werden. Die weißen Flecken erscheinen als grobkörnige silberne hellweiße Flecken auf dem Bruch.
Gründe für die Bildung: Es wird allgemein angenommen, dass es die Wirkung von Wasserstoff und Gewebespannung ist, d Phasenumwandlung von Stahl.
3. die Größe des Defekts
1. Maßabweichung:
Die Abmessungen einschließlich Länge, Durchmesser, Dicke, Plus- und Minustoleranz, Schleiftiefe und Breite des Stahls entsprechen nicht den Anforderungen der Bestellnorm.
2. Ovalität:
bezieht sich auf den Unterschied in Größe und Durchmesser auf dem Stahlprofil eines kreisförmigen Profils.
3. Krümmung: Der Stahl ist in Längs- und Breitenrichtung nicht gerade und die Biegungen verschiedener Materialien haben unterschiedliche Namen. Das Profil wird durch die Biegung dargestellt; Platte und Band werden durch die Sichelbiegung, die Wellenbiegung und den Krümmungsgrad dargestellt.
4. Torsion:
Der Bandstahl wird in axialer Richtung spiralförmig verdrillt.
4. Analyse von White-Spot-Fehlern in Stahl
White-Spot-Fehler in Stahl sind die Quelle von Rissen, die zu Stahlbrüchen und katastrophalen Unfällen führen können. White-Spot-Fehler in Stahl werden durch die kombinierte Wirkung von hohem Wasserstoffgehalt in Stahl und inneren Spannungen verursacht. Weiße Flecken sind innere Risse im Stahl, bei denen es sich um metallurgische Fehler handelt, die im fertigen Stahl nicht zulässig sind.
Im Allgemeinen erzeugt kohlenstoffarmer niedriglegierter Stahl keine White-Spot-Fehler. Einige Studien haben jedoch gezeigt, dass auch bei einigen kohlenstoffarmen und niedriglegierten Stählen (wie 16Mn-Stahl) White-Spot-Fehler auftreten können. Es wird berichtet, dass gewöhnlicher Kohlenstoffstahl mit einem Kohlenstoff-Massenanteil von etwa 0.20% und einem Wasserstoff-Massenanteil von 0.0004% weiße Fleckdefekte aufweist.
Als nächstes werden wir die White-Spot-Fehler in kohlenstoffarmen niedriglegierten Stählen mit Inspektionsmethoden wie Ultraschallfehlererkennung, geringer Vergrößerung, Makrobruch, Metallographie und Rasterelektronenmikroskopie untersuchen und diskutieren.
Die chemische Zusammensetzung und der H-Gehalt von Stahl sind in Tabelle 1 aufgeführt und die Prüfgegenstände und -mengen sind in Tabelle 2 aufgeführt.
1. Ultraschallfehlererkennung und Schwachstromprüfung
Um den Ort des Fehlers zu bestimmen, wird das Ultraschall-Fehlererkennungsverfahren zur Messung verwendet. Die horizontalen und longitudinalen thermischen Säureätztests mit niedriger Leistung (6-10 mal) werden an den schweren und dichten Stellen des Fehlers durchgeführt. Beide für den Weißpunkt charakteristischen Risse sind zu finden. Die weißen Risse mit Emission oder konzentrischen Kreisen werden beobachtet, und es ist zu erkennen, dass es schwierig ist, die weißen Fleckenrisse in der Stahlplatte auf dem Prüfstück mit niedriger Leistung zu identifizieren.
2. Makrobruchtest
Nehmen Sie in ähnlicher Weise Proben an Stellen, an denen die Fehlerwellen bei der Ultraschallfehlererkennung stark und dicht sind und an der Fraktur entenschnabelförmige Risse gefunden werden können.
3. Mechanischer Leistungstest
Die Stahlplatten wurden Z-Richtungs-Zugversuchen und Z-Richtungs--40ºC-Schlagtests unterzogen. Die Testergebnisse sind in Tabelle 3 aufgeführt. Die Festigkeitskennzahlen der Proben mit weißen Flecken am Zugbruch in Z-Richtung nahmen leicht ab, während die Plastizitäts- und Schlagzähigkeitskennzahlen deutlich abnahmen.
4. Metallographische Prüfung
Nehmen Sie die metallographische Probe an der Stelle, an der sich bei der Probe mit geringer Vergrößerung ein Riss mit weißen Flecken mit offensichtlichen Zickzack-Eigenschaften befindet, wie in Abbildung 3 gezeigt.
Die Ergebnisse der metallographischen Untersuchung zeigen, dass die spröden Einschlüsse 1 bis 1.5 Grad aufweisen, die plastischen Einschlüsse 0.5 bis 1.5 Grad aufweisen und die gebänderte Struktur ernsthaft ist und 3 bis 4 Grad erreicht.
5. Rasterelektronenmikroskopische Beobachtung
Analysieren Sie die verschiedenen Strukturen in der Nähe des weißen Punktrisses durch das Rasterelektronenmikroskopie-Energiespektrum. Die Ergebnisse zeigen, dass der Mangangehalt in den Perlitstreifen relativ hoch ist, insbesondere im körnigen Bainitbereich. Der Massenanteil von Mangan erreicht 2.51 %, während der Massenanteil von Mangan in der Matrix nur etwa 1.5 % beträgt.
6 Fazit
(1) Die Eigenschaften von weißen Flecken auf der Bruchfläche der Zugproben aus Stahlblech sind weiße Fleckendefekte, die im Stahlbarren gebildet werden, und es gibt keine sekundären weißen Flecken, die durch Schweißen verursacht werden, wenn das Stahlblech gewalzt wird.
(2) Die weißen Flecken in der Stahlplatte sind nicht so offensichtlich wie die weißen Flecken in kohlenstoffreichem Stahl, legiertem Stahl, Vierkant- und Rundstahl auf der Oberfläche mit niedrigem Säureangriff. Es kann durch Ultraschall-Fehlererkennung und horizontale Bruchprüfungsmethoden beurteilt werden. Sie kann auch durch metallographische Untersuchung und rasterelektronenmikroskopische Untersuchungsverfahren weiter bestätigt werden.
(3) Die White-Spot-Risse in der Stahlplatte treten in der körnigen Bainzone des Perlitstreifens auf, und die gebänderte Struktur liefert die strukturelle Spannung, die erforderlich ist, um den White-Spot-Fehler zu bilden. Die Bandstruktur wird durch die Entmischung von Mangan (und Kohlenstoff und Schwefel) verursacht. Diese Entmischung führt zu einer Erhöhung des lokalen Wasserstoffgehalts und schafft Bedingungen für die Bildung von weißen Flecken mit höherem Wasserstoff. Es wird unter der kombinierten Wirkung von Gewebestress und lokalem Wasserstoff produziert. Weißer Fleck defekt.
(4) Die White-Spot-Risse in der Stahlplatte haben einen geringen Einfluss auf die mechanischen Längs- und Längseigenschaften, verringern jedoch den Plastizitätsindex in z-Richtung und den Schlagzähigkeitswert erheblich.
(5) Obwohl Platten aus kohlenstoffarmem und niedriglegiertem Stahl nicht so leicht weiße Fleckfehler erzeugen wie kohlenstoffreicher Stahl und legierter Stahl, können sie auch weiße Fleckfehler erzeugen, ohne auf die Kontrolle des Wasserstoffgehalts beim Schmelzen zu achten und das langsame Abkühlen von Knüppeln.
Link zu diesem Artikel: Analyse gängiger Qualitätsprobleme von Stahl und deren Ursachen
Nachdruck-Erklärung: Sofern keine besonderen Hinweise vorliegen, sind alle Artikel auf dieser Seite Originale. Bitte geben Sie die Quelle für den Nachdruck an: https://www.cncmachiningptj.com/,thanks!
PTJ® bietet eine vollständige Palette von Custom Precision CNC-Bearbeitung China Dienstleistungen.ISO 9001:2015 & AS-9100 zertifiziert. 3, 4 und 5-Achsen schnelle Präzision CNC-Bearbeitung Dienstleistungen wie Fräsen, Blech nach Kundenspezifikation,Bearbeitung von Metall- und Kunststoffteilen mit einer Toleranz von +/-0.005 mm.Sekundäre Dienstleistungen umfassen CNC- und konventionelles Schleifen, Laser schneiden,Bohren,Druckguss,Blech und Stempeln.Bereitstellung von Prototypen, vollständigen Produktionsläufen, technischem Support und vollständiger Inspektion. Dient den Automobilindustrie, Luft-und Raumfahrt, Form & Befestigung, LED-Beleuchtung,sowie medizinische,Fahrrad und Verbraucher Elektronik Branchen. Pünktliche Lieferung.Erzählen Sie uns ein wenig über das Budget Ihres Projekts und die voraussichtliche Lieferzeit. Wir werden mit Ihnen Strategien entwickeln, um die kostengünstigsten Dienstleistungen anzubieten, damit Sie Ihr Ziel erreichen können. Willkommen bei uns ( sales@pintejin.com ) direkt für Ihr neues Projekt.
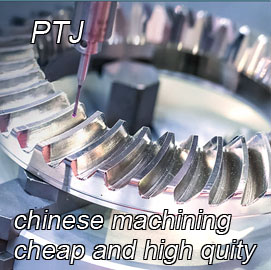
- 5-Achsen-Bearbeitung
- CNC-Fräsen
- CNC drehen
- Bearbeitungsindustrie
- Bearbeitungsprozess
- Oberflächenbearbeitung
- Metallbearbeitung
- Kunststoffbearbeitung
- Pulvermetallurgie-Form
- Druckguss
- Teile Galerie
- Autoteile aus Metall
- Maschinenteile
- LED-Kühlkörper
- Gebäudeteile
- Mobilteile
- Medizinische Teile
- Electronic Parts
- Maßgeschneiderte Bearbeitung
- Fahrradteile
- Aluminiumbearbeitung
- Titanbearbeitung
- Edelstahlbearbeitung
- Kupferbearbeitung
- Messingbearbeitung
- Bearbeitung von Superlegierungen
- Peek-Bearbeitung
- UHMW-Bearbeitung
- Einzelbearbeitung
- PA6-Bearbeitung
- PPS-Bearbeitung
- Teflon-Bearbeitung
- Inconel-Bearbeitung
- Werkzeugstahlbearbeitung
- Mehr Material