Porositätsanalyse und Lösungen für Druckguss
Mit der rasanten Entwicklung der Automobilindustrie und der Nachfrage nach leichten Automobilen haben die Druckgussteile aus Aluminium, Magnesium und anderen Legierungen deutlich zugenommen, was eine breite Perspektive für die weitere Entwicklung der Druckgussindustrie bietet. Aufgrund der Nachfrage nach Leichtbauteilen sind die Anforderungen an die Leistungsfähigkeit des Legierungsmaterials, die Produktstruktur sowie die Prozessgestaltung und -kontrolle strenger.
Die Anforderungen an Druckgussteile verschiedener Automobilwerke werden immer strenger. Die Anforderungen an die Porosität von Druckgussteilen liegen in der Regel bei 5-10 %, bei bestimmten Teilen sogar bei 3 %. Für die Erkennungsmethode und Erkennungsposition von Druckguss Defekte ist es möglich, mithilfe von Computersimulationsanalysen experimentelle Untersuchungen bei der Auswahl von Druckguss Maschinen-, Formen- und Prozessdesign und nutzen die P-Q2-Software zur Optimierung.
Die Poren, Lunker und Schlackenlochfehler von Druckgussteilen treten im Inneren der Gussteile auf, und die Ursachen für die Fehler sind unterschiedlich. Um Fehler zu beseitigen, ist es wichtig, die Arten von Fehlern zu identifizieren und ihre Ursachen zu analysieren, und die Werkzeuge und Methoden zur Inspektion von Teilen beeinflussen die endgültige Beurteilung. Im Folgenden erläutert der Autor nur, wie das Problem der Poren beim Druckguss von Aluminium- und Magnesiumlegierungen gelöst werden kann.
1. Stoma-Check
Bei der Poreninspektion von Druckgussteilen sind mehrere Positionen zu berücksichtigen:
①Die maximale Spannungsposition der Finite-Elemente-Analyse;
②Teilesimulationsanalyse der Mitnahmeposition;
③Schlüsselteile von Teilen (wie Dichtfläche usw.).
Im Allgemeinen können Druckgussteile durch Röntgen untersucht werden; Nachdem Mängel festgestellt wurden, werden die Teile zur weiteren Prüfung geschnitten. Bei der Prozesskontrolle wird gemäß ASTM E505 Level 2 kontrolliert, und die wichtigsten Teile sollten gemäß ASTM E505 Level 1 kontrolliert werden.
Die Spaltöffnungen haben im Allgemeinen eine glatte Oberfläche, rund oder oval, manchmal isoliert, manchmal zusammengehäuft. Bild 1 zeigt die Porenoberfläche eines Druckgussteils.
Der Schrumpfhohlraum und die Schrumpfporosität sind unregelmäßig geformt und die Oberflächenfarbe ist dunkel und nicht glatt. Unter dem Mikroskop und Elektronenmikroskop findet man an der Defektstelle eine dendritische Struktur.
2. Stomabildung
2.1. Wasserstoffporen
Abbildung 3 zeigt die Wasserstoffporen. Die Wasserstoffporen sind winzig, nadelförmig und gleichmäßig verteilt, was man nach der Bearbeitung der Oberfläche des Teils beobachten kann. Aufgrund der dünnen Wand des Druckgussteils ist die Erstarrungsgeschwindigkeit des geschmolzenen Metalls schnell, und manchmal sind die Wasserstoffgasporen mit bloßem Auge schwer zu erkennen. Wasserdampf ist die Hauptquelle für Wasserstoff, der aus Ofengas, Schmelzwerkzeugen, Aluminiumbarren/recycelten Teilen, ölverunreinigten Bearbeitungsspänen und Nassraffinationsmitteln stammen kann.
Normalerweise wird beim Druckguss aus Aluminiumlegierungen eine rotierende Entgasungsvorrichtung verwendet (siehe Abbildung 4). Die Gasquelle verwendet im Allgemeinen Argon, Stickstoff oder Chlor. Das Gas wird in die Metallschmelze eingeleitet und durch den Rotor in viele kleine Bläschen zerschnitten. Durch den Konzentrationsunterschied zwischen der Innenseite und der Außenseite der Blasen wird Wasserstoff in die Blasen eingesaugt und gemeinsam aus der Metallschmelze ausgetragen (siehe Abbildung 5).
Der Entgasungseffekt wird durch Faktoren wie Ausrüstung, Gasauswahl, Entgasungsrotordrehzahl und Entgasungszeit beeinflusst und wird gemessen, indem die Dichte des geschmolzenen Metalls nach dem Entgasen erfasst wird. Sammeln Sie eine bestimmte Menge Aluminiumflüssigkeit und gießen Sie sie in einen kleinen Tiegel, geben Sie sie in eine Dekompressionskammer, erstarren Sie unter reduziertem Druck und wiegen Sie Luft bzw. Wasser ein und bestimmen Sie dann die relative Dichte der Probe gemäß der folgenden Formel.
In der Formel ist ρs die relative Dichte der erstarrten Probe; ma ist die Masse der Probe in Luft, g; mw ist die Masse der Probe in Wasser, g.
2.2. Windspalten
Die Lüftungsschlitze sind rund, innen sauber und die Oberfläche ist relativ glatt und glänzend. Die Luft existiert manchmal allein oder zusammengeballt. Abbildung 6 und Abbildung 7 sind die makroskopischen und rasterelektronenmikroskopischen Merkmale von Windspalten. Mitnahme erfolgt in der Regel im Stempelsystem, Angusssystem und Kavität.
2.2.1 Mitnahme des Stanzsystems
Beim Fließen von geschmolzenem Metall von der Druckkammer oder dem Schwanenhals zum inneren Anguss wird viel Luft angesaugt. Der allgemeine Druckgussprozess kann das turbulente Flüssigkeitsströmungsmuster nicht ändern, aber das Zufuhrsystem kann verbessert werden, um die Mitnahmevolumen des geschmolzenen Metalls zum inneren Anguss.
Beim Kaltkammer-Druckguss ist der Füllgrad zu berücksichtigen, also das Verhältnis der in die Kaltkammer-Druckgussmaschine eingefüllten Flüssigmetallmenge zum Volumen der Druckkammer. Bei der Auslegung von Prozessparametern sollte die Fülle größer als 50 % sein, vorzugsweise 70-80 %. Bild 8 zeigt den Zusammenhang zwischen Fülle und Mitnahmevolumen eines Druckgussteils.
Bei der Auswahl der Druckgussmaschine und der Formkonstruktion wird sie im Allgemeinen von der P-Q2-Software berechnet (P ist Druck, Q ist Durchfluss) und die geeignete Druckkammergröße und Fülle werden ausgewählt. Nachdem die Größe des Schießrohres bestimmt wurde, sollte die Gießgeschwindigkeit von der Schöpfkelle zum Schießrohr berücksichtigt werden. Wenn die Fülle weniger als 50% beträgt, ist der obere Raum der Druckkammer groß und das geschmolzene Metall erzeugt Wellen und bewegt sich zwischen dem Stempel und der Matrize hin und her. Wenn der Stempel beginnt, sich vorwärts zu bewegen, verschmelzen die reflektierten Wellen von der Vorderseite des Stempels und der Mitte des Schussrohrs, und es kommt zu Turbulenzen und Mitreißen. Dadurch wird die Porosität des Gussstücks erhöht und gleichzeitig das flüssige Metall in der Druckkammer abgekühlt, was für die Befüllung ungünstig ist.
Die beste Lösung besteht darin, dass der Stempel begonnen hat, sich zu bewegen, bevor die Metallwelle reflektiert wird, dh die Richtung des Stempels und der Anfangswelle ist gleich, was das Mitreißen stark reduzieren kann. Verwenden Sie außerdem die P-Q2-Software, um sinnvollere Designparameter auszuwählen, um eine Fülle von mindestens 50 % zu erreichen.
Bei der Produktentwicklung und -konstruktion sollten auch die folgenden Prozessfaktoren berücksichtigt werden: ①Für Kaltkammer-Druckguss, einschließlich Gießgeschwindigkeit, Einspritzverzögerungszeit, Niederdruck-Einspritzbeschleunigung, Angussgeschwindigkeit, Umschaltpunkt Anguss zu Niederdrehzahl-Spritzen, Einspritzgeschwindigkeit bei niedrigem Druck und schneller Startpunkt der Einspritzung; ②Für Heißkammer-Druckguss beinhaltet es den Umschaltpunkt von Niederdruck-Einspritzbeschleunigung, Niederdruck-Einspritzgeschwindigkeit zu Schnelleinspritzung. Passen Sie die obigen Parameter entsprechend an und überwachen Sie sie, um den Grad des Mitreißens zu minimieren.
2.2.2. Mit- und Absaugung des Läufersystems
Sobald das geschmolzene Metall bei einer Geschwindigkeit von 64-160 km/h auf eine Änderung der Form des Angusskanals trifft, bewirkt die Impulskraft, dass das geschmolzene Metall einen Wirbel erzeugt, was zu Defekten mit eingeschlossenen Luftlöchern führt.
Um diese Art des Mitreißens durch eine rationelle Gestaltung der Gießrinne zu lösen, ist es notwendig, die Stabilität der Metallschmelze während des gesamten Füllvorgangs zu gewährleisten und die Wölbung und Größe der Gießrinne sinnvoll zu wählen.
2.2.3 Hohlraummitnahme
Um die Defekte von Hohlraumeinschlüssen und Luftlöchern zu reduzieren, muss sichergestellt werden, dass das Überlaufsystem vernünftig konstruiert ist und die Absaugung ungehindert ist. Abbildung 9 zeigt ein Überlaufsystem für ein Druckgussteil. Das Überlaufsystem besteht aus Überlaufrillen, Abluftrillen und Überlaufkanälen.
Das Überlaufsystem sollte die Ableitung des Front-End-Gases der Metallschmelze sicherstellen. Üblicherweise wird ein Z-förmiger oder fächerförmiger Auspuff verwendet, und die Tiefe ist gering und befindet sich am Rand der Form, um Spritzer zu vermeiden.
Die Überlaufrille und die Auslassrille werden im Allgemeinen auf die endgültige Füllposition des Flüssigmetalls eingestellt. Die Position kann durch Moldflow-Analyse bestimmt werden, während eine ausreichende Abgasgröße sichergestellt wird; Die Abluftrille an der Trennfläche wird normalerweise am hinteren Ende der Überlaufrille angebracht, um die Wirkung von Überlauf und Absaugung zu verstärken. Der zahnförmige Abluftkanal hat eine gute Abluftwirkung. Bei der Gestaltung der Form ist am besten darauf zu achten, dass mindestens ein zahnförmiger Abluftkanal vorhanden ist.
Vakuumdruckguss hilft, solche Probleme zu lösen. Bevor die Metallschmelze eintrifft, hat die Vakuumanlage bereits ihren Betrieb aufgenommen. Im Betriebsstandard die Zeit, die der Stempel benötigt, um das Vakuum zu erreichen Ventil vom Tor aus überwacht werden. Im Allgemeinen sollte sie mindestens 1 Sekunde betragen. Manchmal ist es notwendig, die Startposition der Low-Speed-Einspritzung anzupassen.
Beim traditionellen Druckguss werden die Überlaufrille und das Abgassystem verwendet, und der Anfangsdruck am inneren Anguss kann 180 kPa erreichen und die Endfüllung kann 400 kPa erreichen; Beim Vakuum-Druckguss werden ein Vakuumkanal und ein Vakuumventil verwendet, um den Vordruck am inneren Anguss zu erreichen. 20kPa, die Endfüllung kann 18kPa erreichen. Im Allgemeinen erreicht der Gasdruck in der Kavität unter Vakuumbedingungen 2-7 kPa; und ohne Vakuum erreicht der Gasdruck in der Kavität mehr als 300 kPa. Daher kann die Vakuumtechnologie den Druck in der Kavität effektiv reduzieren.
Achten Sie bei der Prozessgestaltung auf folgende Punkte:
①Das Kufensystem sollte eckige Ecken vermeiden und eine glatte Oberfläche des Kufens gewährleisten;
②Das Überlaufsystem sollte in der besten Position so konstruiert sein, dass es den Rand der Form erreicht und die Absaugfläche ausreichend ist und eine ausreichende Absaugung gewährleistet ist;
③Das Vakuumsystem ist auf der Tastenoberfläche und dem Anschlussteil angebracht, um Leckagen und Störungen durch die Umgebung zu vermeiden; die Größe des Vakuumkanals ist richtig, insbesondere am Eingang der Kavität; der Druck in der Kavität wird gemessen und überwacht, und wenn er den Überwachungsbereich überschreitet, ein Alarm und automatisch Ausschussteile; das Vakuumventil funktioniert normal; das Vakuumsystem wird regelmäßig gereinigt.
2.2.4. Simulationsanalyse
Die Simulationstechnologie des Druckgussverfahrens kann den Füllprozess (Strömungsfeld) des Gussstücks simulieren, um die Lufteinschlüsse in Schussrohr, Lauf und Kavität vorherzusagen. Die numerische Simulation des Gussfüllprozesses kann den Technikern helfen, die Größe, den Ort und den Zeitpunkt des Auftretens der verschiedenen Mitnahmedrücke, die im Gussprozess auftreten können, effektiv vorherzusagen, wodurch die Gestaltung des Gussprozesses optimiert und die Qualität der Gussteile sichergestellt wird, und Verkürzung des Probeproduktionszyklus senkt die Produktionskosten. Abbildung 10 zeigt die Simulationsanalyse eines bestimmten Druckgussgasmitrisses, und die tatsächliche Porenposition stimmt mit der Mitrissposition der simulierten Strömungsfeldanalyse überein.
Wenn sich die Formparameter und das Design der Prozessparameter ändern, sollte die Simulationsanalyse erneut durchgeführt und sorgfältig ausgewertet werden, um den effektiven Betrieb des Überlaufsystems sicherzustellen.
2.3. Wasserdampfporen
Das Aussehen der Wasserdampfporen ist im Allgemeinen rund, grau, trüb, ungleichmäßig und trocken schuppig, wie in Abbildung 11 gezeigt. Wenn dieses Merkmal auftritt, überprüfen Sie das Spritzen des Trennmittels und die Undichtigkeit der Kühlwasserleitung der Form.
Wenn geschmolzenes Metall während des Füllvorgangs auf Wasser trifft, entsteht Wasserdampf. Bei der Umwandlung von Wasser in Dampf kommt es zur Expansion. An der Stelle der Wassertröpfchen bilden sich Wasserdampfblasen. Der Raum, den die Blasen einnehmen, beträgt etwa das 1500-fache der ursprünglichen Wassertröpfchen. Das Gas lässt sich nur schwer durch das Überlaufsystem abführen, existiert irgendwo im Metall und seine Position ist schwer vorherzusagen.
Etwa 98% der allgemeinen Wasserdampfporen stammen von Druckgussbeschichtungen. Tritt hauptsächlich bei folgenden Druckgussverfahren auf: ①Es wird zu viel Farbe auf Wasserbasis auf die Form gesprüht, und wenn die Form zu schließen beginnt, ist die Kavität nicht vollständig trocken; ②Die Wasserleitung ist undicht;
③Das Anschlussgewinde der Wasserleitung undicht;
④Die Form reißt und Wasser sickert ein;
⑤Wenn das Werkzeug geschlossen ist, fließen die Wassertropfen am oberen Ende des Werkzeugs in die Kavität;
⑥Die wasserbasierte Hydraulikflüssigkeit verbleibt auf der Form.
Link zu diesem Artikel: Porositätsanalyse und Lösungen für Druckguss
Nachdruck-Erklärung: Sofern keine besonderen Hinweise vorliegen, sind alle Artikel auf dieser Seite Originale. Bitte geben Sie die Quelle für den Nachdruck an: https://www.cncmachiningptj.com/,thanks!
PTJ® bietet eine vollständige Palette von Custom Precision CNC-Bearbeitung China Dienstleistungen.ISO 9001:2015 & AS-9100 zertifiziert. 3, 4 und 5-Achsen schnelle Präzision CNC-Bearbeitung Dienstleistungen wie Fräsen, Blech nach Kundenspezifikation,Bearbeitung von Metall- und Kunststoffteilen mit einer Toleranz von +/-0.005 mm.Sekundäre Dienstleistungen umfassen CNC- und konventionelles Schleifen, Laser schneiden,Bohren,Druckguss,Blech und Stempeln.Bereitstellung von Prototypen, vollständigen Produktionsläufen, technischem Support und vollständiger Inspektion. Dient den Automobilindustrie, Luft-und Raumfahrt, Form & Befestigung, LED-Beleuchtung,sowie medizinische,Fahrrad und Verbraucher Elektronik Branchen. Pünktliche Lieferung.Erzählen Sie uns ein wenig über das Budget Ihres Projekts und die voraussichtliche Lieferzeit. Wir werden mit Ihnen Strategien entwickeln, um die kostengünstigsten Dienstleistungen anzubieten, damit Sie Ihr Ziel erreichen können. Willkommen bei uns ( sales@pintejin.com ) direkt für Ihr neues Projekt.
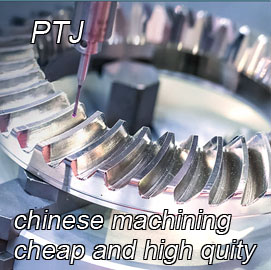
- 5-Achsen-Bearbeitung
- CNC-Fräsen
- CNC drehen
- Bearbeitungsindustrie
- Bearbeitungsprozess
- Oberflächenbearbeitung
- Metallbearbeitung
- Kunststoffbearbeitung
- Pulvermetallurgie-Form
- Druckguss
- Teile Galerie
- Autoteile aus Metall
- Maschinenteile
- LED-Kühlkörper
- Gebäudeteile
- Mobilteile
- Medizinische Teile
- Electronic Parts
- Maßgeschneiderte Bearbeitung
- Fahrradteile
- Aluminiumbearbeitung
- Titanbearbeitung
- Edelstahlbearbeitung
- Kupferbearbeitung
- Messingbearbeitung
- Bearbeitung von Superlegierungen
- Peek-Bearbeitung
- UHMW-Bearbeitung
- Einzelbearbeitung
- PA6-Bearbeitung
- PPS-Bearbeitung
- Teflon-Bearbeitung
- Inconel-Bearbeitung
- Werkzeugstahlbearbeitung
- Mehr Material